Atomic Layer Deposition (ALD) is a highly precise and controlled thin-film deposition technique used to create ultra-thin, uniform, and conformal layers of material at the atomic scale. It operates through a cyclic process involving sequential exposure of a substrate to two or more gas-phase precursors, separated by purge steps to remove excess reactants and by-products. Each cycle deposits a monolayer of material, and the process is repeated until the desired film thickness is achieved. ALD is renowned for its ability to produce films with exceptional uniformity, conformality, and control over thickness, even on complex geometries.
Key Points Explained:
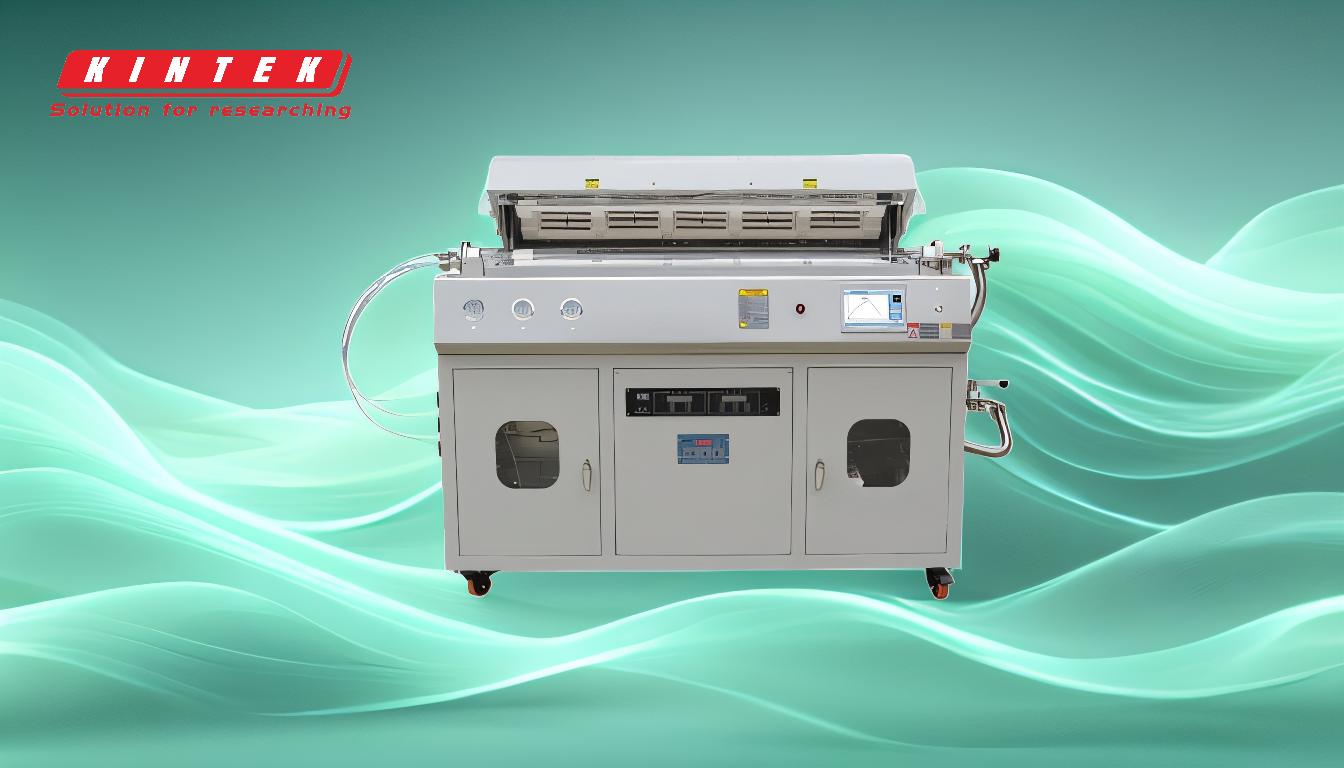
-
Sequential Precursor Exposure:
- ALD relies on the sequential introduction of two or more precursors into the reaction chamber.
- The first precursor is introduced and chemisorbs onto the substrate surface, forming a chemically-bound monolayer.
- The second precursor is then introduced, reacting with the first to form a stable, atomic-scale layer of the desired material.
- This sequential exposure ensures precise control over the deposition process.
-
Self-Limiting Reactions:
- Each precursor exposure is self-limiting, meaning the reaction stops once all available reactive sites on the substrate are occupied.
- This self-limiting nature ensures uniformity and prevents over-deposition, which is critical for achieving atomic-level precision.
-
Purge Steps:
- After each precursor exposure, the chamber is purged with an inert gas (e.g., nitrogen or argon) to remove excess precursor and reaction by-products.
- Purge steps are essential to prevent unwanted gas-phase reactions and ensure the purity of the deposited film.
-
Cyclic Repetition:
- The process of precursor exposure and purging is repeated in cycles.
- Each cycle deposits a monolayer of material, typically a few angstroms thick.
- The number of cycles determines the final film thickness, allowing for precise control down to the nanometer scale.
-
Conformality and Uniformity:
- ALD is known for its exceptional conformality, meaning it can uniformly coat complex 3D structures, including high-aspect-ratio features.
- This makes ALD ideal for applications requiring uniform thin films on intricate surfaces, such as semiconductor devices, MEMS, and nanostructures.
-
Temperature Control:
- ALD is performed within a controlled temperature range, typically between 100°C and 400°C, depending on the precursors and substrate.
- Temperature control ensures optimal reaction kinetics and film quality while avoiding thermal damage to the substrate.
-
Applications of ALD:
- ALD is widely used in industries such as semiconductors, optics, energy storage, and biomedical devices.
- It is particularly valuable for creating high-quality dielectric layers, barrier coatings, and functional thin films in advanced technologies.
-
Advantages of ALD:
- Precision: Enables atomic-level control over film thickness.
- Uniformity: Produces highly uniform and conformal coatings.
- Versatility: Compatible with a wide range of materials, including oxides, nitrides, and metals.
- Scalability: Suitable for both research and industrial-scale production.
-
Challenges in ALD:
- Slow Deposition Rate: The cyclic nature of ALD makes it slower compared to other deposition techniques like CVD or PVD.
- Precursor Cost: High-purity precursors can be expensive, impacting the overall cost of the process.
- Complexity: Requires precise control over process parameters, such as temperature, pressure, and precursor flow rates.
-
Future Trends in ALD:
- Development of new precursors to expand the range of materials that can be deposited.
- Integration of ALD with other deposition techniques for hybrid processes.
- Advancements in spatial ALD for faster deposition rates and industrial scalability.
In summary, ALD is a sophisticated and versatile deposition technique that offers unparalleled precision and control over thin-film growth. Its ability to produce uniform, conformal, and high-quality films makes it indispensable in cutting-edge technologies and industries. However, its relatively slow deposition rate and high precursor costs remain challenges that are being addressed through ongoing research and innovation.
Summary Table:
Key Aspect | Description |
---|---|
Process | Cyclic, sequential exposure to precursors with purge steps for atomic precision. |
Advantages | Precision, uniformity, conformality, versatility, and scalability. |
Applications | Semiconductors, optics, energy storage, biomedical devices. |
Challenges | Slow deposition rate, high precursor costs, and process complexity. |
Future Trends | New precursors, hybrid processes, and faster spatial ALD techniques. |
Learn how ALD can revolutionize your thin-film applications—contact us today!