Calcination is a thermal treatment process applied to ores and other solid materials in the absence or limited supply of air or oxygen, primarily to bring about a thermal decomposition, phase transition, or removal of a volatile fraction. The process typically occurs in a furnace, where the material is heated to high temperatures, often between 800°C and 1300°C, depending on the material and desired outcome. Calcination is widely used in industries such as metallurgy, cement production, and chemical manufacturing to transform raw materials into more useful forms by driving off moisture, carbon dioxide, or other volatile substances. The process can also alter the physical and chemical properties of the material, making it more suitable for further processing or use.
Key Points Explained:
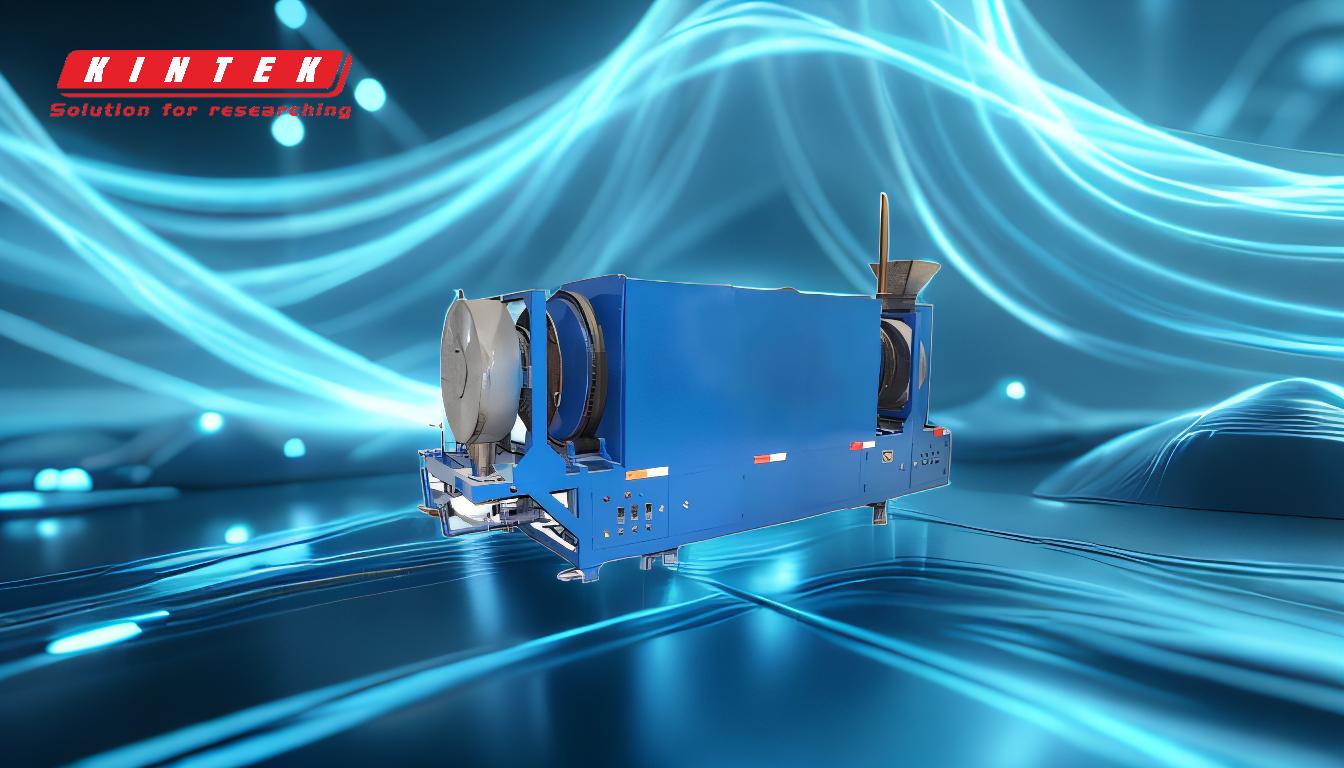
-
Definition and Purpose of Calcination:
- Calcination is a heat treatment process used to decompose or alter materials by heating them to high temperatures in a controlled environment, typically in a furnace.
- The primary purpose is to remove volatile components such as water, carbon dioxide, or organic matter, or to induce a phase change in the material.
- This process is essential in industries like metallurgy, where it is used to convert metal carbonates or hydroxides into oxides, and in cement production, where limestone is calcined to produce lime.
-
Types of Furnaces Used for Calcination:
- Rotary Kilns: These are cylindrical furnaces that rotate to ensure uniform heating of the material. They are commonly used for large-scale calcination processes, such as in cement production.
- Muffle Furnaces: These are enclosed furnaces where the material is heated indirectly, protecting it from direct contact with combustion gases. They are often used in laboratory settings or for small-scale calcination.
- Shaft Furnaces: These are vertical furnaces where the material is loaded from the top and heated as it moves downward. They are typically used for calcining limestone or other materials in bulk.
-
Temperature and Atmosphere Control:
- The temperature during calcination is critical and varies depending on the material being processed. For example, limestone calcination typically occurs at around 900°C, while other materials may require higher temperatures.
- The atmosphere within the furnace is controlled to limit the presence of oxygen, which prevents oxidation and ensures the desired chemical reactions occur.
-
Chemical Reactions During Calcination:
-
Decomposition Reactions: Many materials undergo decomposition during calcination. For example, calcium carbonate (limestone) decomposes into calcium oxide (lime) and carbon dioxide:
[ \text{CaCO}_3 \rightarrow \text{CaO} + \text{CO}_2 ] - Phase Transitions: Some materials may undergo a change in crystal structure or phase during calcination, which can improve their properties for further use.
- Removal of Volatiles: Calcination is often used to remove water, carbon dioxide, or other volatile components from materials, leaving behind a more stable product.
-
Decomposition Reactions: Many materials undergo decomposition during calcination. For example, calcium carbonate (limestone) decomposes into calcium oxide (lime) and carbon dioxide:
-
Applications of Calcination:
- Cement Production: Calcination of limestone is a key step in the production of cement, where it is used to produce lime, a primary ingredient in cement.
- Metallurgy: Calcination is used to convert metal carbonates or hydroxides into oxides, which are then reduced to produce metals.
- Chemical Industry: Calcination is used to produce various chemicals, such as alumina from bauxite or titanium dioxide from titanium ore.
- Ceramics and Glass Manufacturing: Calcination is used to prepare raw materials for ceramics and glass by removing impurities and altering their properties.
-
Advantages of Calcination:
- Purification: Calcination removes impurities and volatile components, resulting in a purer product.
- Improved Material Properties: The process can enhance the physical and chemical properties of materials, making them more suitable for specific applications.
- Energy Efficiency: Modern calcination furnaces are designed to be energy-efficient, reducing the overall cost of the process.
-
Challenges and Considerations:
- Energy Consumption: Calcination requires significant energy input, especially for high-temperature processes, which can be costly.
- Emissions: The process can release carbon dioxide and other gases, contributing to environmental concerns. Proper emission control systems are necessary to mitigate this impact.
- Material Handling: Handling materials at high temperatures requires specialized equipment and safety precautions to prevent accidents and ensure consistent quality.
In summary, calcination is a versatile and essential process in many industries, involving the controlled heating of materials in a furnace to achieve specific chemical and physical transformations. The choice of furnace, temperature, and atmosphere are critical factors that influence the success of the calcination process.
Summary Table:
Aspect | Details |
---|---|
Definition | Heat treatment process for decomposition or alteration of materials. |
Temperature Range | Typically 800°C to 1300°C, depending on material and desired outcome. |
Furnace Types | Rotary Kilns, Muffle Furnaces, Shaft Furnaces. |
Key Applications | Cement production, metallurgy, chemical manufacturing, ceramics, and glass. |
Advantages | Purification, improved material properties, energy efficiency. |
Challenges | High energy consumption, emissions, and material handling at high temps. |
Discover how calcination can optimize your industrial processes—contact us today for expert guidance!