Coating deposition is a sophisticated process used to apply thin layers of material onto a substrate, enhancing its properties such as durability, conductivity, or appearance. The process varies depending on the technique used, such as Physical Vapor Deposition (PVD) or Chemical Vapor Deposition (CVD). Generally, it involves preparing the substrate, creating a vacuum or controlled environment, vaporizing the coating material, and depositing it onto the substrate. Quality control and finishing steps ensure the coating meets desired specifications. Each method has unique steps and considerations, but the core principles of preparation, deposition, and validation remain consistent.
Key Points Explained:
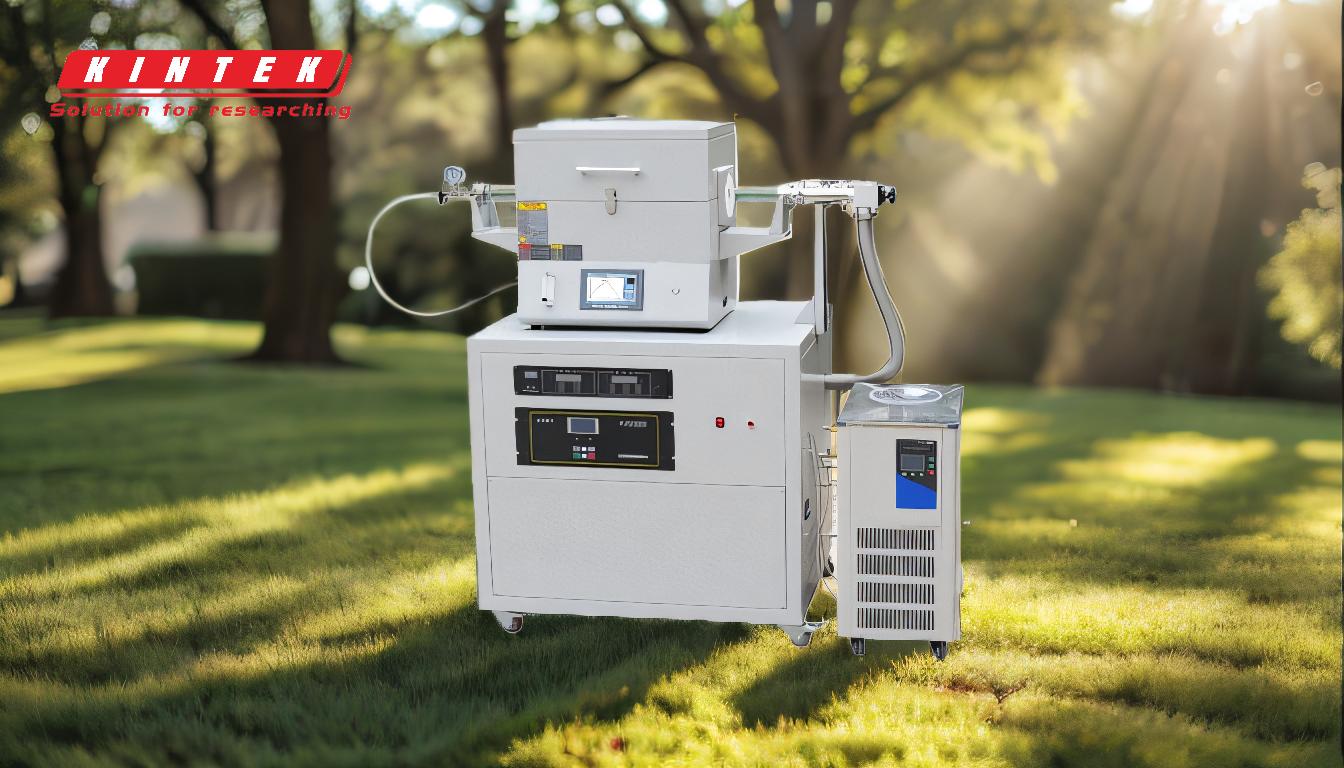
-
Preparation of the Substrate:
- The substrate must be thoroughly cleaned to remove contaminants like oils, dust, or oxides that could interfere with adhesion.
- Pretreatment processes, such as etching or applying adhesion-promoting layers, may be used to enhance bonding between the coating and substrate.
-
Creating a Controlled Environment:
- For PVD and CVD, a vacuum or controlled atmosphere is essential to prevent contamination and ensure uniform deposition.
- In PVD, a vacuum chamber is used to eliminate air and gases, while CVD relies on precise control of gas flow and pressure.
-
Vaporization of the Coating Material:
- In PVD, the coating material is vaporized through methods like sputtering (using ions to knock atoms off a target) or evaporation (heating the material until it turns into vapor).
- In CVD, gaseous reactants are introduced into the chamber, where they react on the substrate surface to form the coating.
-
Deposition onto the Substrate:
- The vaporized material is transported to the substrate, where it condenses and forms a thin film.
- Uniformity is critical, and techniques like rotating the substrate or using monitoring tools (e.g., quartz crystal microbalance) ensure even distribution.
-
Reaction and Film Formation:
- In CVD, the reaction between gases and the substrate creates the desired coating, often involving a metal catalyst to facilitate the process.
- In PVD, the properties of the coating, such as hardness or color, are determined during the reaction phase.
-
Cooling and Venting:
- After deposition, the system is cooled to stabilize the coating.
- The chamber is vented to return to atmospheric pressure, allowing the coated substrate to be removed.
-
Quality Control and Testing:
- Each batch of coated components is tested for consistency in composition, thickness, and performance.
- Tools like X-ray fluorescence (XRF) machines and spectrophotometers are used to verify specifications.
-
Finishing and Post-Treatment:
- Additional steps, such as annealing or polishing, may be applied to enhance the coating's properties or appearance.
- These steps ensure the final product meets the required standards for its intended application.
-
Applications and Variations:
- PVD is commonly used for decorative coatings, wear-resistant layers, and electronic components.
- CVD is ideal for creating high-purity films, such as graphene or semiconductor materials.
- Both methods can be tailored to specific needs by adjusting parameters like temperature, pressure, and material choice.
By understanding these steps, purchasers of equipment and consumables can better evaluate the suitability of different coating deposition methods for their specific applications.
Summary Table:
Step | Description |
---|---|
1. Substrate Preparation | Clean and pretreat the substrate to remove contaminants and enhance adhesion. |
2. Controlled Environment | Create a vacuum or controlled atmosphere to ensure uniform deposition and prevent contamination. |
3. Vaporization | Vaporize the coating material using PVD (sputtering/evaporation) or CVD (gas reactions). |
4. Deposition | Transport and condense the vaporized material onto the substrate for uniform thin film formation. |
5. Reaction & Film Formation | Facilitate reactions (CVD) or determine coating properties (PVD) during the process. |
6. Cooling & Venting | Cool the system and vent the chamber to stabilize the coating and remove the substrate. |
7. Quality Control | Test for consistency in composition, thickness, and performance using advanced tools. |
8. Finishing | Apply post-treatments like annealing or polishing to enhance properties and appearance. |
9. Applications | Tailor methods (PVD/CVD) for decorative, wear-resistant, or high-purity coatings. |
Ready to enhance your materials with advanced coating deposition? Contact us today to find the perfect solution for your needs!