The process of consumable electrode arc melting is a specialized technique used in metallurgy to melt and refine metals, particularly for producing high-quality alloys and pure metals. It involves using an electric arc to melt a consumable electrode, which is typically made of the same material as the desired final product. The molten metal drips into a water-cooled crucible, where it solidifies into an ingot. This method is known for its ability to produce clean, homogeneous, and high-purity metal ingots with minimal contamination. The process is widely used in industries such as aerospace, nuclear, and advanced manufacturing, where material quality is critical.
Key Points Explained:
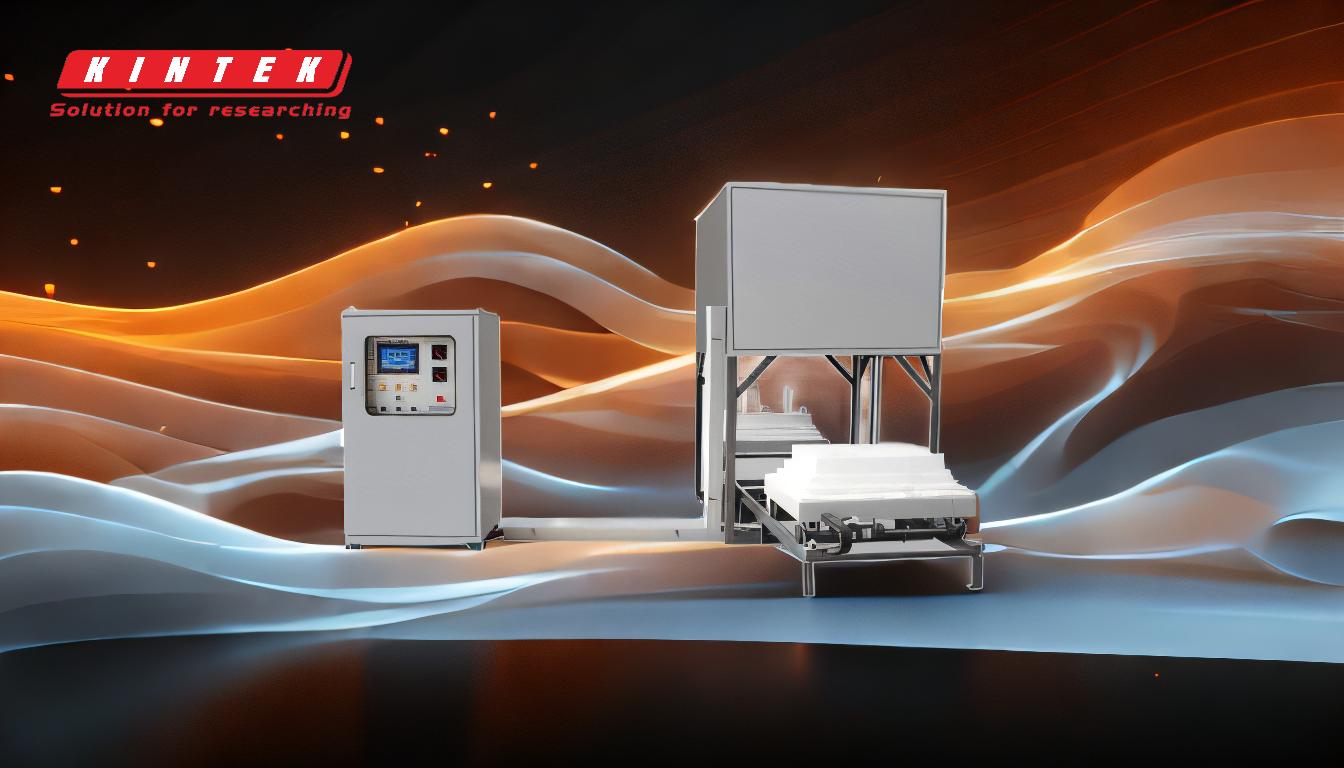
-
Overview of Consumable Electrode Arc Melting:
- Consumable electrode arc melting is a refining process used to produce high-quality metal ingots.
- It involves melting a consumable electrode using an electric arc, which generates intense heat to melt the electrode material.
- The molten metal is collected in a water-cooled crucible, where it solidifies into an ingot.
-
Components of the Process:
- Consumable Electrode: The electrode is made of the same material as the desired final product. It is consumed during the melting process.
- Electric Arc: The arc is created between the electrode and the crucible, providing the heat necessary to melt the electrode.
- Water-Cooled Crucible: The crucible collects the molten metal and is cooled by water to solidify the metal into an ingot.
- Vacuum or Inert Atmosphere: The process is often conducted under a vacuum or inert gas to prevent contamination and oxidation.
-
Steps in the Process:
- Electrode Preparation: The consumable electrode is prepared to the required size and composition.
- Melting: The electrode is melted using the electric arc, and the molten metal drips into the crucible.
- Solidification: The molten metal solidifies in the water-cooled crucible, forming a dense and homogeneous ingot.
- Cooling and Removal: The ingot is cooled further and then removed from the crucible for further processing.
-
Advantages of Consumable Electrode Arc Melting:
- High Purity: The process minimizes contamination, resulting in high-purity metal ingots.
- Homogeneity: The ingots produced are uniform in composition and structure.
- Control Over Composition: The process allows precise control over the chemical composition of the final product.
- Versatility: It can be used for a wide range of metals and alloys, including titanium, nickel, and zirconium.
-
Applications:
- Aerospace Industry: Used to produce high-strength, lightweight alloys for aircraft and spacecraft components.
- Nuclear Industry: Essential for producing pure metals and alloys used in nuclear reactors.
- Advanced Manufacturing: Used in the production of high-performance materials for various industrial applications.
-
Challenges and Considerations:
- Energy Consumption: The process requires significant energy to generate and maintain the electric arc.
- Equipment Cost: The specialized equipment, such as vacuum arc furnaces, can be expensive.
- Process Control: Precise control over the melting and solidification process is necessary to achieve the desired material properties.
By understanding the process of consumable electrode arc melting, manufacturers can produce high-quality metal ingots that meet the stringent requirements of advanced industries. This method is a cornerstone of modern metallurgy, enabling the production of materials with exceptional purity and performance.
Summary Table:
Aspect | Details |
---|---|
Overview | Refining process for high-quality metal ingots using an electric arc. |
Key Components | Consumable electrode, electric arc, water-cooled crucible, vacuum/inert gas. |
Steps | Electrode preparation, melting, solidification, cooling, and removal. |
Advantages | High purity, homogeneity, precise composition control, versatility. |
Applications | Aerospace, nuclear, advanced manufacturing. |
Challenges | High energy consumption, expensive equipment, precise process control. |
Interested in high-purity metal production? Contact our experts today to learn more!