Deposition in wafer fabrication is a critical process in the semiconductor industry, used to create high-quality thin films and solid materials on substrates. The process typically involves four main stages: ramp up, etching, coating, and ramp down. During ramp up, the chamber is prepared by adjusting temperature and pressure. Etching cleans the substrate to enhance adhesion, while coating involves projecting the desired material onto the substrate. Finally, the chamber is returned to ambient conditions during ramp down. Various deposition technologies, such as LPCVD, PECVD, ALD, and PVD, are employed depending on the material and application requirements. Materials like aluminum and tungsten are commonly used, with techniques like HDP-CVD and plasma-enhanced CVD ensuring precise deposition.
Key Points Explained:
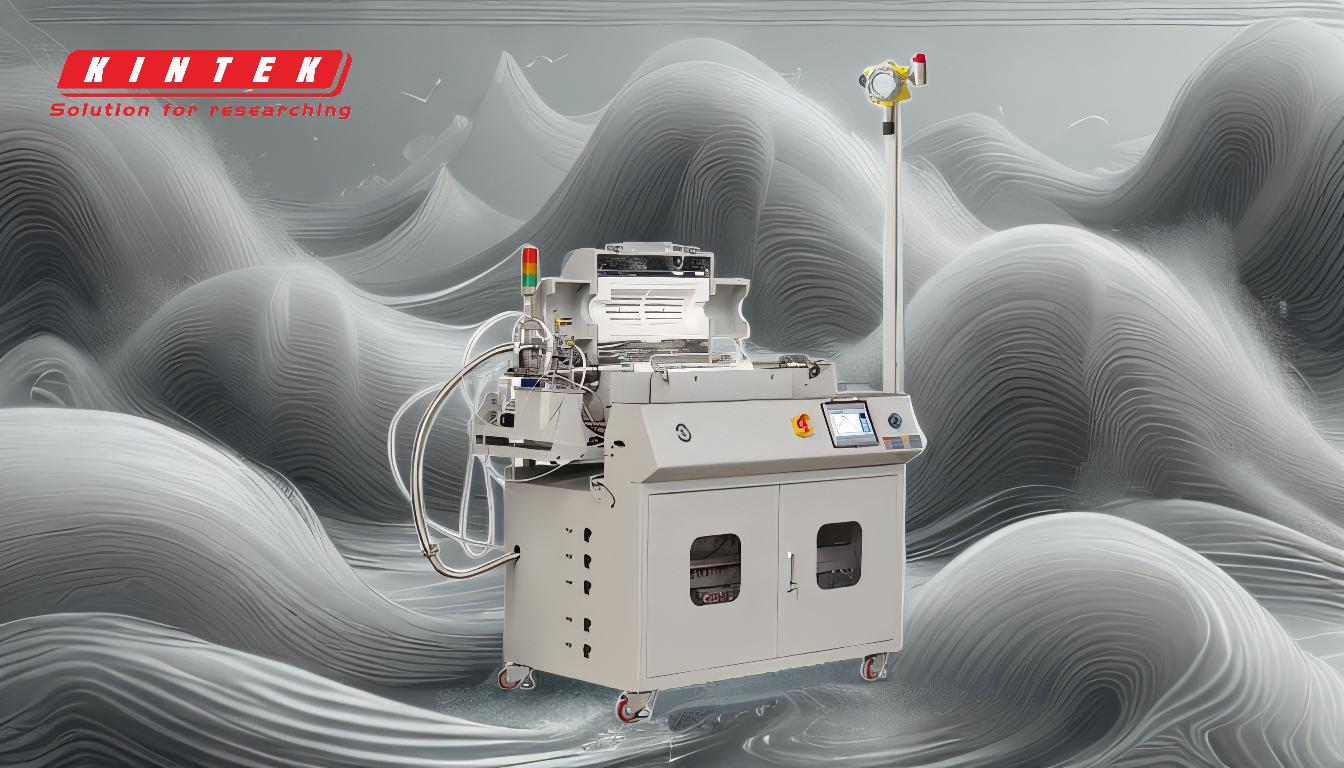
-
Overview of Deposition in Wafer Fabrication
- Deposition is a foundational process in semiconductor manufacturing, used to create thin films or layers of materials on a substrate (typically a silicon wafer).
- These layers form the basis for constructing integrated circuits and other semiconductor devices.
- The process ensures high-quality, high-performance materials are deposited uniformly and precisely.
-
Four Key Stages of Deposition
-
Ramp Up:
- The chamber is prepared by gradually increasing temperature and decreasing pressure to create a controlled environment.
- This step ensures the substrate and chamber are ready for the deposition process.
-
Etching:
- Plasma etching is used to clean the substrate surface, removing contaminants and improving adhesion for the deposited material.
- This step is crucial for ensuring the quality and reliability of the deposited layer.
-
Coating:
- The material to be deposited is projected onto the substrate using techniques like sputtering, evaporation, or chemical reactions.
- The choice of technique depends on the material and the desired properties of the film.
-
Ramp Down:
- After deposition, the chamber is gradually cooled and returned to ambient pressure.
- This step prevents thermal stress and ensures the stability of the deposited layer.
-
Ramp Up:
-
Common Deposition Technologies
-
Chemical Vapor Deposition (CVD):
- Includes Low Pressure CVD (LPCVD), Plasma Enhanced CVD (PECVD), and Sub-Atmospheric CVD (SACVD).
- CVD involves chemical reactions to deposit materials like silicon dioxide, silicon nitride, or tungsten.
-
Atomic Layer Deposition (ALD):
- A precise technique that deposits materials layer by layer, ensuring uniform thickness and high conformity.
-
Physical Vapor Deposition (PVD):
- Techniques like sputtering or evaporation are used to deposit metals such as aluminum or copper.
-
Epitaxial Deposition (Epi):
- Used to grow crystalline layers on a substrate, often for creating high-performance semiconductor materials.
-
Chemical Vapor Deposition (CVD):
-
Materials Used in Deposition
-
Aluminum:
- Commonly used for the main conductive layer in semiconductor devices.
-
Tungsten:
- Deposited using CVD techniques for interconnects and contacts due to its high conductivity and durability.
-
Silicon-Based Materials:
- Silicon dioxide and silicon nitride are deposited for insulation and passivation layers.
-
Diamond-Like Carbon (DLC):
- Used for specialized applications requiring high hardness and wear resistance.
-
Aluminum:
-
Applications and Importance of Deposition
- Deposition is essential for creating the intricate layers and structures in modern semiconductor devices.
- It enables the production of transistors, interconnects, and insulating layers, which are critical for device functionality.
- The quality of the deposition process directly impacts the performance, reliability, and yield of semiconductor devices.
-
Factors Influencing Deposition Process
-
Temperature and Pressure:
- Precise control is required to ensure uniform deposition and avoid defects.
-
Substrate Preparation:
- Cleaning and etching are critical for achieving strong adhesion and high-quality films.
-
Material Properties:
- The choice of deposition technique depends on the material's properties, such as melting point and reactivity.
-
Temperature and Pressure:
-
Challenges in Deposition
- Achieving uniform thickness across large wafers.
- Minimizing defects such as voids, cracks, or impurities.
- Ensuring compatibility with subsequent processing steps, such as lithography and etching.
By understanding the deposition process and its key components, semiconductor manufacturers can optimize their fabrication processes to produce high-performance devices efficiently.
Summary Table:
Aspect | Details |
---|---|
Key Stages | Ramp Up, Etching, Coating, Ramp Down |
Common Technologies | LPCVD, PECVD, ALD, PVD, Epitaxial Deposition |
Materials Used | Aluminum, Tungsten, Silicon Dioxide, Silicon Nitride, Diamond-Like Carbon |
Applications | Transistors, Interconnects, Insulating Layers |
Challenges | Uniform Thickness, Defect Minimization, Compatibility with Other Processes |
Optimize your wafer fabrication process with expert insights—contact us today!