The process of electron beam (E-beam) technology involves using a focused beam of electrons to modify materials or deposit thin films in a controlled manner. This process is widely used in industries for applications such as polymer crosslinking, material degradation, sterilization, and thin-film deposition. The technology operates in a vacuum environment, where electrons are emitted from a heated tungsten filament, accelerated by high voltage, and focused into a beam using magnetic fields. The beam's kinetic energy is converted into thermal energy upon impact with a target material, causing it to evaporate or sublimate. The resulting vapor then condenses onto a substrate, forming a thin film. The process is highly precise, energy-efficient, and versatile, making it suitable for applications in electronics, optics, medical devices, and more.
Key Points Explained:
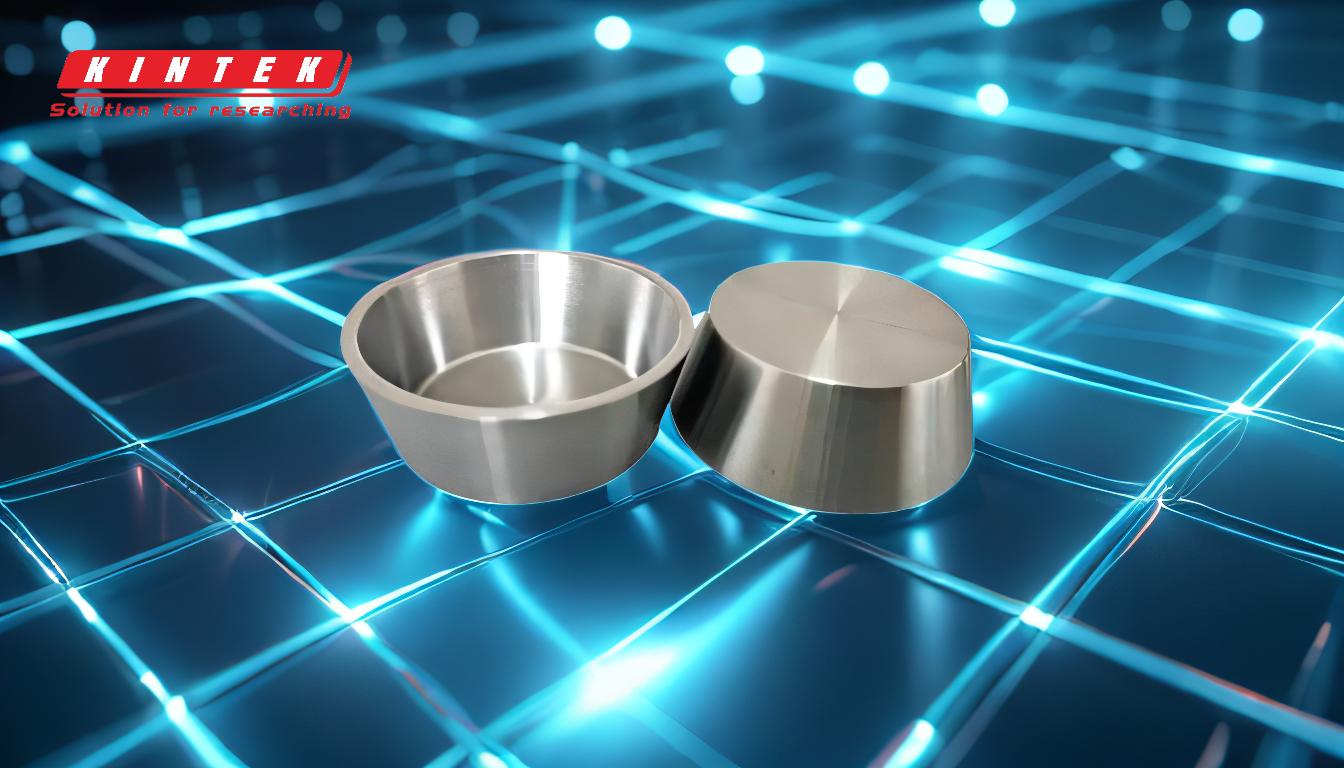
-
Electron Beam Generation:
- Electrons are emitted from a heated tungsten filament through thermionic emission.
- A high voltage (typically between 5 and 10 kV) accelerates these electrons.
- Magnetic fields focus the electrons into a fine, high-energy beam.
-
Vacuum Environment:
- The entire process occurs in a vacuum chamber to prevent interference from air molecules.
- The vacuum ensures that the electron beam travels unimpeded and that the evaporated material deposits uniformly on the substrate.
-
Energy Transfer and Material Evaporation:
- The electron beam is directed toward a target material (e.g., metals, ceramics) placed in a water-cooled crucible.
- The kinetic energy of the electrons is converted into thermal energy upon impact, heating the material.
- Metals typically melt and then evaporate, while ceramics sublimate directly into a vapor phase.
-
Thin-Film Deposition:
- The evaporated material travels through the vacuum chamber and condenses onto a substrate.
- The thickness and uniformity of the deposited film are controlled by adjusting parameters such as electron beam intensity, substrate position, and rotation.
-
Applications of Electron Beam Processing:
- Polymer Crosslinking: Enhances mechanical, thermal, and chemical properties of polymers.
- Material Degradation: Used in recycling processes to break down materials.
- Sterilization: Effective for medical and pharmaceutical products.
- Thin-Film Deposition: Used in semiconductor manufacturing, optical coatings, and electronics.
-
Advantages of Electron Beam Technology:
- High precision and control over the deposition process.
- Ability to deposit a wide range of materials, including metals, ceramics, and composites.
- Energy-efficient and environmentally friendly compared to other deposition methods.
- Suitable for creating dense, robust coatings with minimal stress.
-
Enhancements to the Process:
- Reactive gases (e.g., oxygen, nitrogen) can be introduced to deposit non-metallic films.
- Ion beam assistance can improve adhesion and density of the deposited films.
- Computer-controlled systems enable precise control over vacuum levels, heating, and substrate movement.
-
Industrial Applications:
- Electronics: Deposition of thin films for semiconductors and electronic components.
- Optics: Creation of precision optical coatings for lenses and mirrors.
- Medical Devices: Sterilization and coating of implants and surgical tools.
- Food Processing: Sterilization and preservation of food products.
In summary, electron beam processing is a versatile and efficient technology that leverages the controlled application of high-energy electrons to modify materials and deposit thin films. Its precision, energy efficiency, and wide range of applications make it a valuable tool in industries ranging from electronics to healthcare.
Summary Table:
Key Aspect | Details |
---|---|
Electron Beam Generation | Electrons emitted from a tungsten filament, accelerated by high voltage. |
Vacuum Environment | Ensures unimpeded electron beam travel and uniform material deposition. |
Energy Transfer | Electron kinetic energy converts to thermal energy, evaporating materials. |
Thin-Film Deposition | Evaporated material condenses onto substrates, forming precise thin films. |
Applications | Polymer crosslinking, sterilization, material degradation, and more. |
Advantages | High precision, energy efficiency, and versatility. |
Industrial Use | Electronics, optics, medical devices, and food processing. |
Learn how electron beam technology can revolutionize your processes—contact our experts today!