Electron beam coating, also known as electron beam evaporation or E-Beam deposition, is a sophisticated thin-film deposition process used to create highly durable and precise coatings on substrates. The process involves vaporizing a source material using an electron beam in a vacuum chamber, allowing the vapor to condense onto a substrate, forming a thin film. This method is widely used in industries requiring high-performance coatings, such as optics, electronics, and aerospace. The process is enhanced by precise control of vacuum levels, substrate positioning, and sometimes ion beam assistance to improve adhesion and coating density.
Key Points Explained:
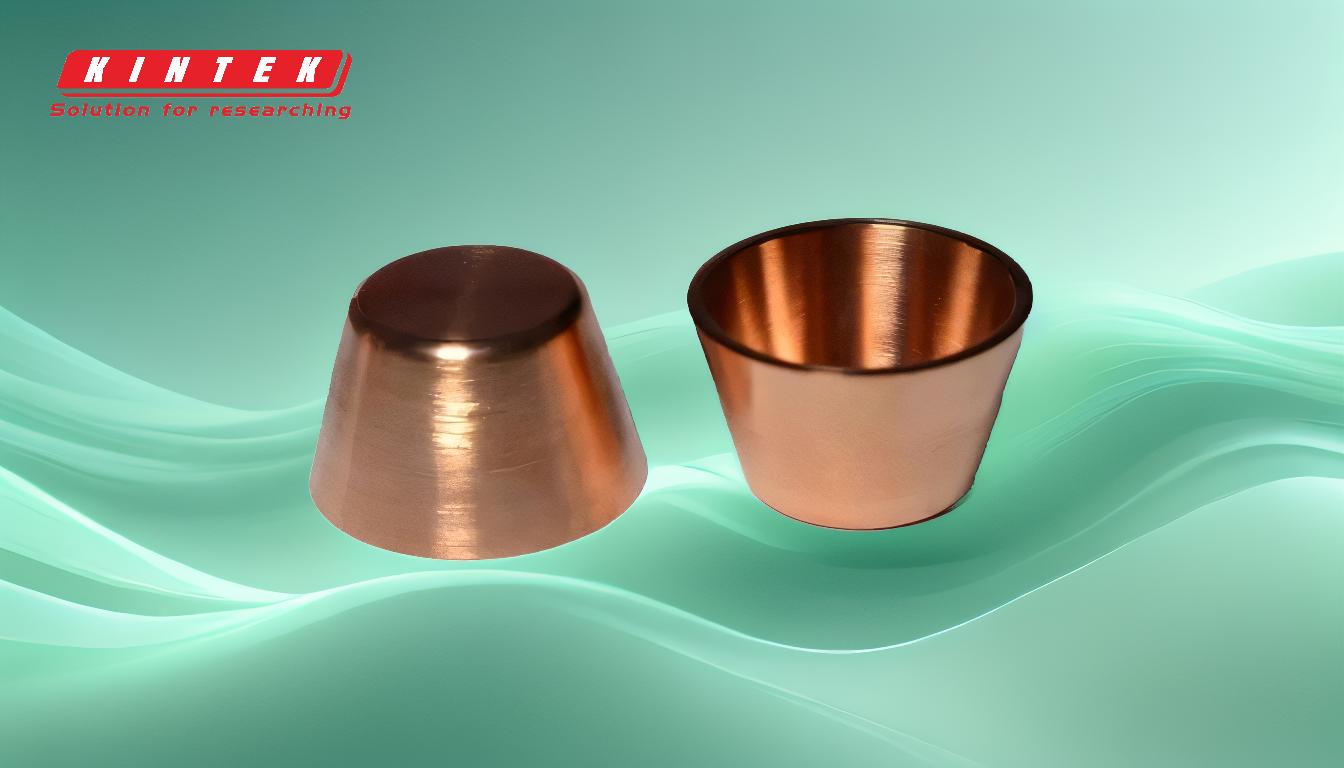
-
Overview of Electron Beam Coating:
- Electron beam coating is a vacuum-based thin-film deposition process.
- It uses an electron beam to heat and vaporize a source material, which then condenses onto a substrate to form a coating.
- The process is highly controlled, allowing for precise thickness and uniformity of the coating.
-
Components of the Electron Beam Coating System:
- Vacuum Chamber: The process occurs in a vacuum to prevent contamination and ensure high-quality coatings.
- Electron Beam Gun: Generates and focuses a high-energy electron beam onto the source material.
- Crucible: Holds the material to be evaporated, typically made of materials like tungsten or graphite.
- Substrate Holder: Holds the substrate to be coated, often with rotation capabilities for uniform coating.
- Ion Beam Source (Optional): Used to enhance adhesion and density of the coating by bombarding the substrate with ions.
-
Step-by-Step Process:
- Material Loading: The source material (e.g., metals, ceramics) is placed in the crucible.
- Vacuum Creation: The chamber is evacuated to create a high-vacuum environment.
- Electron Beam Generation: The electron beam gun generates a focused beam of electrons.
- Material Heating: The electron beam bombards the source material, causing it to heat rapidly and evaporate (or sublimate in the case of ceramics).
- Vapor Deposition: The vaporized material travels through the vacuum and condenses onto the substrate, forming a thin film.
- Substrate Rotation (Optional): The substrate may be rotated to ensure even coating distribution.
- Ion Beam Assistance (Optional): An ion beam may be used to improve coating adhesion and density.
-
Advantages of Electron Beam Coating:
- Precision: Allows for highly controlled and uniform coatings with precise thickness.
- Versatility: Can deposit a wide range of materials, including metals, ceramics, and alloys.
- Durability: Produces coatings with high abrasion, scratch, and chemical resistance.
- High Purity: The vacuum environment minimizes contamination, resulting in high-purity coatings.
- Enhanced Adhesion: Optional ion beam assistance improves coating adhesion and reduces stress.
-
Applications of Electron Beam Coating:
- Optical Coatings: Used for anti-reflective, reflective, and protective coatings on lenses and mirrors.
- Electronics: Applied in semiconductor manufacturing for thin-film deposition on wafers.
- Aerospace: Used for protective coatings on turbine blades and other critical components.
- Medical Devices: Provides biocompatible coatings on implants and surgical tools.
-
Challenges and Considerations:
- Cost: The equipment and process are expensive due to the need for high vacuum and precise control.
- Material Limitations: Some materials may not be suitable for electron beam evaporation due to their thermal properties.
- Complexity: The process requires skilled operators and careful calibration of parameters like beam intensity, vacuum level, and substrate positioning.
-
Future Trends:
- Integration with Other Technologies: Combining electron beam coating with other deposition methods, such as sputtering or chemical vapor deposition (CVD), to enhance functionality.
- Nanostructured Coatings: Developing coatings with nanoscale features for advanced applications in electronics and photonics.
- Sustainability: Exploring eco-friendly materials and processes to reduce environmental impact.
In summary, electron beam coating is a highly advanced and versatile thin-film deposition technique that offers exceptional precision, durability, and performance. Its applications span multiple industries, and ongoing advancements continue to expand its capabilities and efficiency.
Summary Table:
Aspect | Details |
---|---|
Process | Vaporizes source material using an electron beam in a vacuum chamber. |
Key Components | Vacuum chamber, electron beam gun, crucible, substrate holder, ion beam. |
Advantages | Precision, versatility, durability, high purity, enhanced adhesion. |
Applications | Optics, electronics, aerospace, medical devices. |
Challenges | High cost, material limitations, process complexity. |
Future Trends | Integration with other technologies, nanostructured coatings, sustainability. |
Discover how electron beam coating can elevate your projects—contact our experts today!