Evaporation deposition is a key technique in thin-film fabrication, where a material is vaporized and then deposited onto a substrate to form a thin, uniform layer. The process involves heating the target material until it transitions into a gaseous state, followed by the transportation of these vaporized atoms or molecules to the substrate, where they condense and form a solid film. This method is widely used in industries such as semiconductor manufacturing, solar panel production, and display technologies. The process can be achieved through various methods, including thermal evaporation, electron-beam evaporation, and sputtering, each with its own advantages and applications.
Key Points Explained:
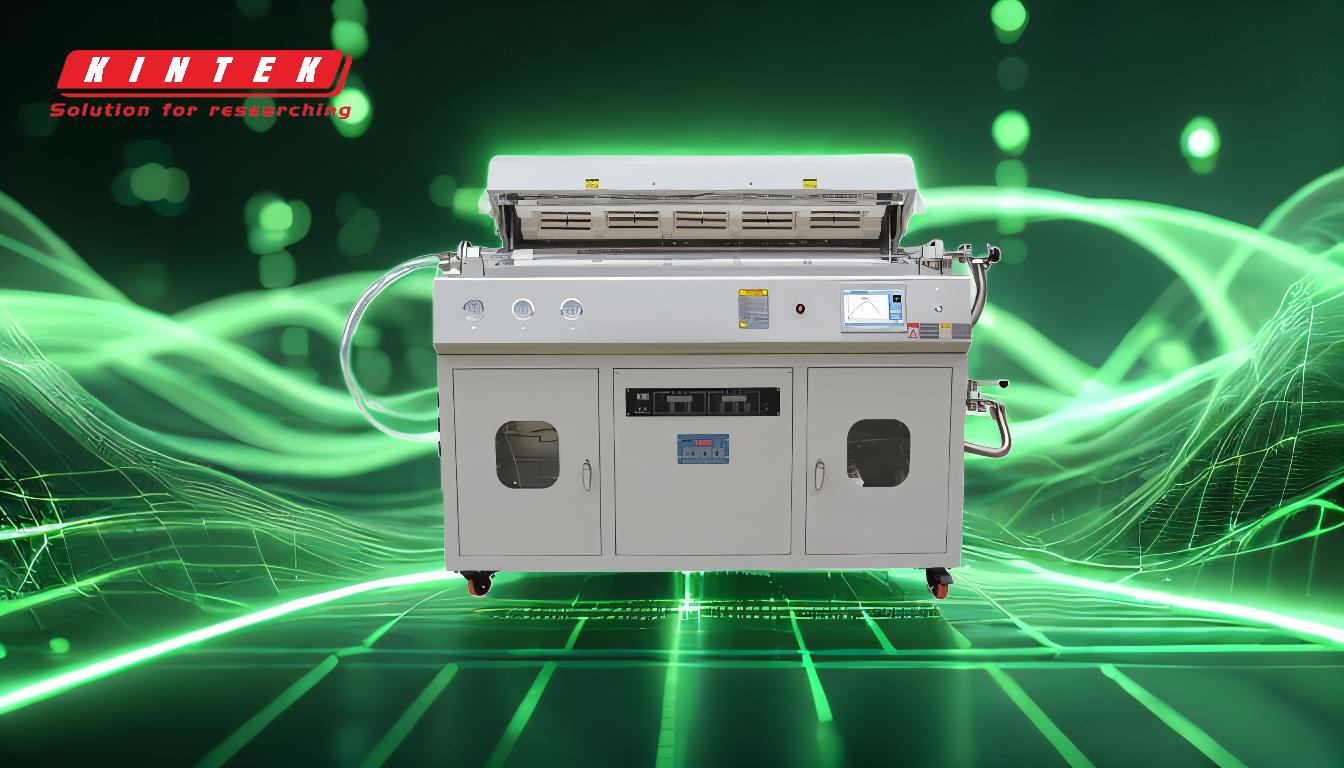
-
Evaporation Process:
- The material to be deposited is heated until it reaches its vaporization point. This can be done using thermal energy from a tungsten heating element or an electron beam. The atoms or molecules gain enough energy to overcome the binding forces in the solid or liquid phase and transition into the gas phase.
- The vaporized material is then transported through a vacuum environment to the substrate.
-
Transportation:
- The vaporized atoms or molecules travel through a high-pressure vacuum to the substrate. This vacuum environment is crucial as it prevents contamination and ensures that the vaporized material reaches the substrate without reacting with other gases.
-
Deposition:
- Upon reaching the substrate, the vaporized material condenses and forms a thin, uniform film. The quality of the film depends on factors such as the substrate temperature, the rate of deposition, and the vacuum conditions.
-
Methods of Evaporation Deposition:
- Thermal Evaporation: Uses a tungsten heating element to vaporize the target material. This method is suitable for depositing pure metals, non-metals, oxides, and nitrides.
- Electron-Beam (E-beam) Evaporation: Employs a high-energy electron beam to evaporate the material. This method is particularly useful for materials with high melting points and is commonly used in the production of solar panels and glass.
- Sputtering Deposition: Involves bombarding the target material with high-energy ions of argon gas to dislodge atoms, which then deposit on the substrate. This method is effective for creating high-quality, uniform films.
-
Applications:
- Solar Panels: Used to deposit conductive metallic layers that enhance the efficiency of solar cells.
- OLED Displays: Essential for creating the thin, conductive layers required for OLED technology.
- Thin-Film Transistors: Utilized in the fabrication of transistors used in electronic devices.
-
Advantages:
- High Purity: The vacuum environment ensures that the deposited film is free from contaminants.
- Uniformity: The process allows for the deposition of very thin, uniform layers, which is critical for many applications.
- Versatility: Can be used with a wide range of materials, including metals, oxides, and nitrides.
-
Challenges:
- High Vacuum Requirements: Maintaining a high vacuum can be technically challenging and costly.
- Material Limitations: Some materials may not be suitable for evaporation deposition due to their high melting points or other properties.
- Complexity: The process requires precise control of parameters such as temperature, pressure, and deposition rate.
In summary, evaporation deposition is a versatile and widely used technique for creating thin films in various industrial applications. By understanding the key steps and methods involved, one can appreciate the complexity and precision required to achieve high-quality results.
Summary Table:
Aspect | Details |
---|---|
Process | Material is vaporized and deposited onto a substrate to form a thin film. |
Key Steps | 1. Evaporation 2. Transportation 3. Deposition |
Methods | Thermal Evaporation, Electron-Beam Evaporation, Sputtering |
Applications | Solar Panels, OLED Displays, Thin-Film Transistors |
Advantages | High Purity, Uniformity, Versatility |
Challenges | High Vacuum Requirements, Material Limitations, Process Complexity |
Discover how evaporation deposition can enhance your manufacturing process—contact our experts today!