Extrusion blow molding is a widely used manufacturing process for creating hollow plastic products, such as bottles, containers, and tanks. The process begins with the extrusion of a heated plastic tube, known as a parison, which is then captured by a press mold. Once the mold closes, air is injected into the parison, inflating it to conform to the shape of the mold. The process is efficient, cost-effective, and suitable for producing large quantities of plastic products with consistent quality. Below, we break down the key steps and considerations involved in extrusion blow molding.
Key Points Explained:
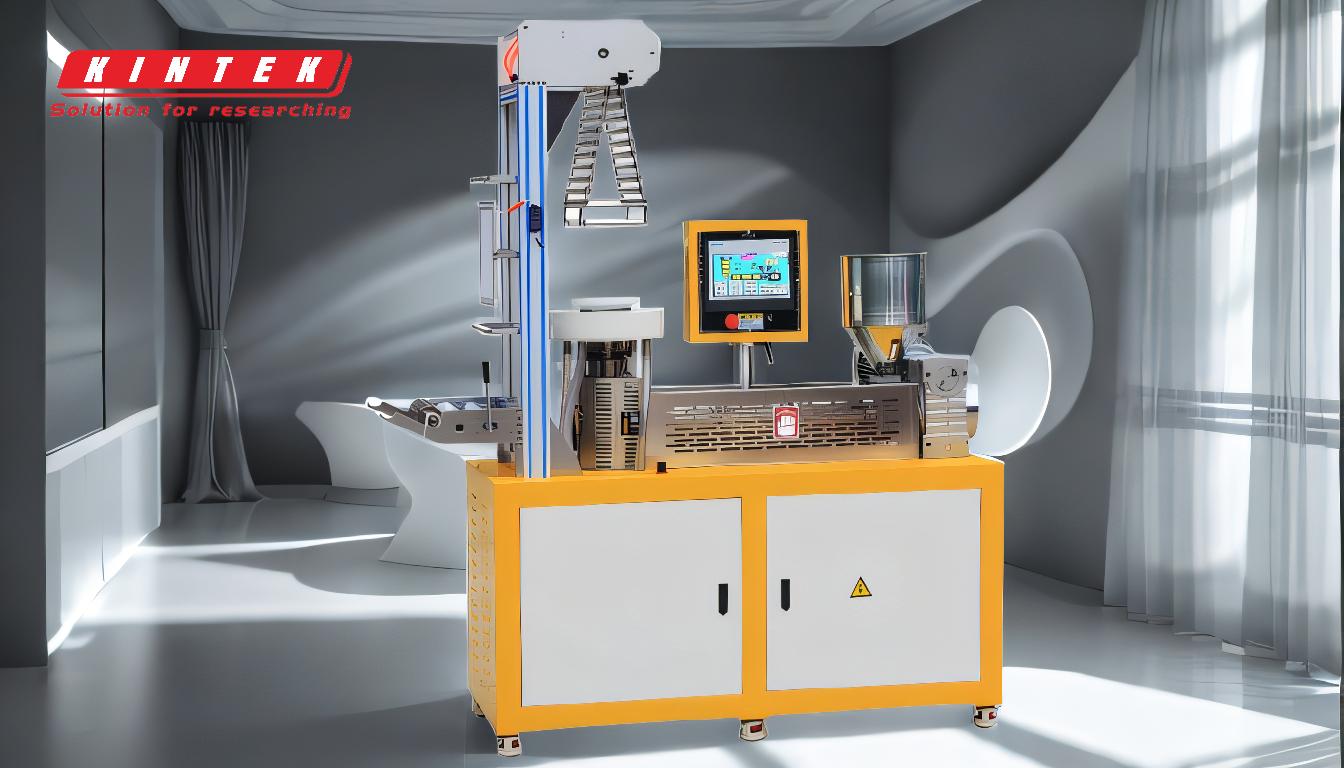
-
Extrusion of the Parison:
- The process starts with the extrusion of a molten plastic tube, called a parison. This is achieved by feeding plastic resin into an extruder, where it is heated and melted.
- The extruder forces the molten plastic through a die, shaping it into a hollow tube. The parison is then dropped vertically into the open mold.
- Key considerations: The thickness and uniformity of the parison are critical, as they directly affect the final product's strength and consistency.
-
Mold Capture and Closing:
- Once the parison is extruded to the desired length, it is captured by the two halves of a water-cooled mold. The mold is designed to match the shape of the final product.
- The mold closes around the parison, pinching it at the top and bottom to seal the ends. This step ensures that the parison is securely held in place for the next stage.
- Key considerations: Mold design and cooling efficiency are crucial for maintaining product quality and reducing cycle times.
-
Air Injection and Inflation:
- After the mold is closed, compressed air is injected into the parison through a blow pin or needle, typically inserted at the top or neck of the container.
- The air pressure inflates the parison, forcing it to expand and conform to the interior shape of the mold. This step is akin to blowing up a balloon.
- Key considerations: The air pressure and timing must be carefully controlled to ensure even distribution of material and avoid defects like thin spots or weak seams.
-
Cooling and Solidification:
- Once the parison has fully expanded, the plastic begins to cool and solidify within the mold. The water-cooled mold accelerates this process, ensuring the product retains its shape.
- Cooling time is a critical factor in the overall cycle time of the process. Efficient cooling reduces production time and improves throughput.
- Key considerations: Proper cooling prevents warping or deformation of the final product.
-
Mold Opening and Part Ejection:
- After the plastic has sufficiently cooled and solidified, the mold opens, and the finished product is ejected.
- Excess plastic, known as flash, is trimmed from the part, typically at the top and bottom where the mold pinched the parison.
- Key considerations: Ejection mechanisms must be designed to avoid damaging the product, and flash removal should be precise to ensure a clean finish.
-
Recycling and Waste Management:
- Excess material, such as flash and trimmings, can often be recycled back into the extrusion process. This reduces waste and lowers material costs.
- Recycling systems must be integrated into the production line to ensure efficient material reuse.
- Key considerations: Proper material handling and recycling practices are essential for maintaining product quality and sustainability.
-
Advantages of Extrusion Blow Molding:
- Cost-effective for high-volume production.
- Suitable for creating complex shapes and large containers.
- Allows for the use of a wide range of thermoplastic materials, such as HDPE, LDPE, and PET.
- Produces seamless and durable products with consistent wall thickness.
-
Limitations and Challenges:
- Limited control over wall thickness in certain areas of the product.
- Not ideal for producing small or intricate parts.
- Requires careful design and maintenance of molds and equipment to avoid defects.
In summary, extrusion blow molding is a versatile and efficient process for manufacturing hollow plastic products. By understanding the key steps and considerations, manufacturers can optimize the process to produce high-quality, cost-effective products tailored to specific applications.
Summary Table:
Step | Key Details | Considerations |
---|---|---|
Extrusion of the Parison | Molten plastic tube (parison) is extruded and dropped into the mold. | Thickness and uniformity of the parison are critical for product strength. |
Mold Capture and Closing | Parison is captured by a water-cooled mold, which closes to seal the ends. | Mold design and cooling efficiency are crucial for quality and cycle time. |
Air Injection and Inflation | Compressed air inflates the parison to conform to the mold shape. | Air pressure and timing must be controlled to avoid defects. |
Cooling and Solidification | Plastic cools and solidifies within the mold. | Proper cooling prevents warping or deformation. |
Mold Opening and Part Ejection | Mold opens, and the finished product is ejected; excess flash is trimmed. | Ejection mechanisms must avoid damage, and flash removal should be precise. |
Recycling and Waste Management | Excess material is recycled back into the process. | Proper material handling ensures sustainability and cost efficiency. |
Advantages | Cost-effective, suitable for complex shapes, wide material range, durable. | |
Limitations | Limited wall thickness control, not ideal for small parts, requires maintenance. |
Ready to optimize your plastic manufacturing process? Contact us today for expert guidance on extrusion blow molding!