Laser sintering, also known as selective laser sintering (SLS), is an advanced additive manufacturing process that uses a high-powered laser to fuse powdered material into a solid three-dimensional structure. This process is guided by a computer-aided design (CAD) file, which directs the laser to selectively bind material at specific points, layer by layer, to create the final part. Unlike traditional sintering methods, laser sintering does not require molds or dies and is capable of producing highly complex geometries with minimal material waste. The process involves preparing the powder, selectively fusing it with a laser, and post-processing the final part to achieve the desired properties.
Key Points Explained:
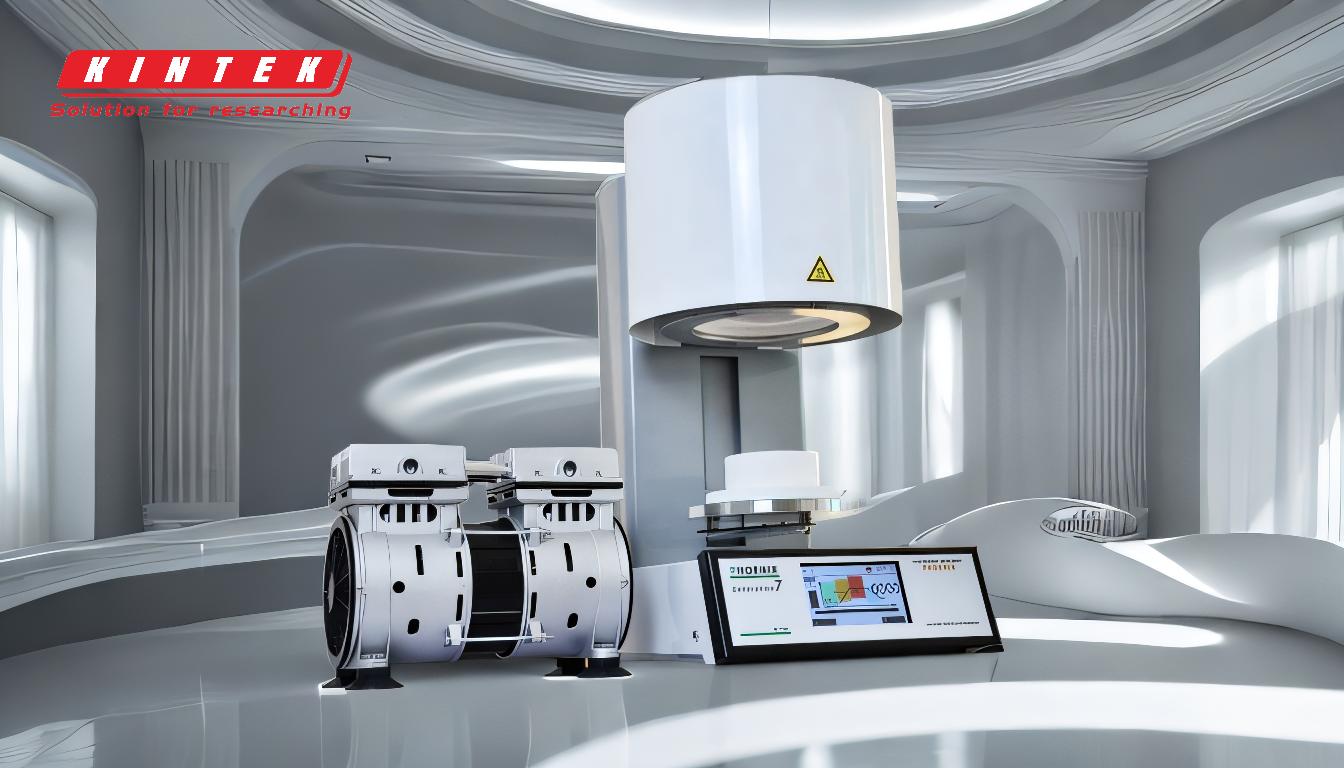
-
Preparation of the Powder Material:
- The process begins with the preparation of the powdered material, which can be metal, polymer, ceramic, or composite. The powder must have specific properties, such as particle size and flowability, to ensure uniform spreading and effective sintering.
- The powder is spread in a thin layer over a build platform inside the sintering machine. A recoater blade or roller ensures an even distribution of the powder.
-
Laser Sintering Process:
- A high-powered laser, typically a CO2 or fiber laser, is used to selectively fuse the powder particles. The laser is guided by a CAD file, which specifies the exact points where the material should be bonded.
- The laser heats the powder to just below its melting point, causing the particles to coalesce and form a solid layer. The process is repeated layer by layer until the entire part is built.
-
Layer-by-Layer Building:
- After each layer is sintered, the build platform is lowered by a small increment, and a new layer of powder is spread over the previous one. The laser then sinters the new layer, bonding it to the layer below.
- This iterative process continues until the entire part is complete. The unsintered powder acts as a support structure during the build, eliminating the need for additional support materials.
-
Cooling and Solidification:
- Once the part is fully built, it is allowed to cool within the build chamber. Cooling is a critical step as it ensures the part solidifies uniformly and minimizes residual stresses.
- The cooling rate can affect the microstructure and mechanical properties of the final part, so it is carefully controlled.
-
Post-Processing:
- After cooling, the part is removed from the build chamber, and excess powder is brushed or blown away. Depending on the material and application, additional post-processing steps may be required, such as heat treatment, surface finishing, or machining.
- Post-processing enhances the part's mechanical properties, dimensional accuracy, and surface quality.
-
Advantages of Laser Sintering:
- Design Freedom: Laser sintering enables the production of complex geometries that are difficult or impossible to achieve with traditional manufacturing methods.
- Material Efficiency: Since the process is additive, it generates minimal waste compared to subtractive methods like machining.
- Rapid Prototyping: Laser sintering is widely used for rapid prototyping due to its ability to quickly produce functional parts directly from CAD files.
- Customization: The process is ideal for producing customized or low-volume parts without the need for expensive tooling.
-
Applications of Laser Sintering:
- Aerospace: Used to produce lightweight, high-strength components with complex geometries.
- Medical: Ideal for creating custom implants, prosthetics, and surgical tools.
- Automotive: Used for prototyping and producing functional parts with reduced weight and improved performance.
- Consumer Goods: Enables the production of customized products and intricate designs.
In summary, laser sintering is a versatile and efficient additive manufacturing process that offers significant advantages in terms of design flexibility, material efficiency, and rapid production. By understanding the key steps and considerations involved, manufacturers can leverage this technology to produce high-quality, complex parts for a wide range of applications.
Summary Table:
Key Steps | Details |
---|---|
Powder Preparation | Powder materials (metal, polymer, ceramic) are prepared for uniform spreading. |
Laser Sintering | A high-powered laser fuses powder particles layer by layer using CAD guidance. |
Layer-by-Layer Building | Each layer is sintered and bonded to the previous one, building the 3D part. |
Cooling & Solidification | The part cools uniformly to minimize stresses and ensure proper solidification. |
Post-Processing | Excess powder is removed, and parts undergo heat treatment or surface finishing. |
Advantages | Design freedom, material efficiency, rapid prototyping, and customization. |
Applications | Aerospace, medical, automotive, and consumer goods industries. |
Ready to explore laser sintering for your manufacturing needs? Contact our experts today!