Melting alloys involves heating a mixture of metals or a metal with other elements to a temperature above their melting points to form a homogeneous liquid. This process is crucial in manufacturing, as it allows for the creation of materials with specific properties tailored to various applications. The process typically involves selecting the right materials, preparing them, heating them in a controlled environment, and then cooling them to form the desired alloy. Each step requires careful control of temperature, composition, and cooling rates to ensure the final product meets the required specifications.
Key Points Explained:
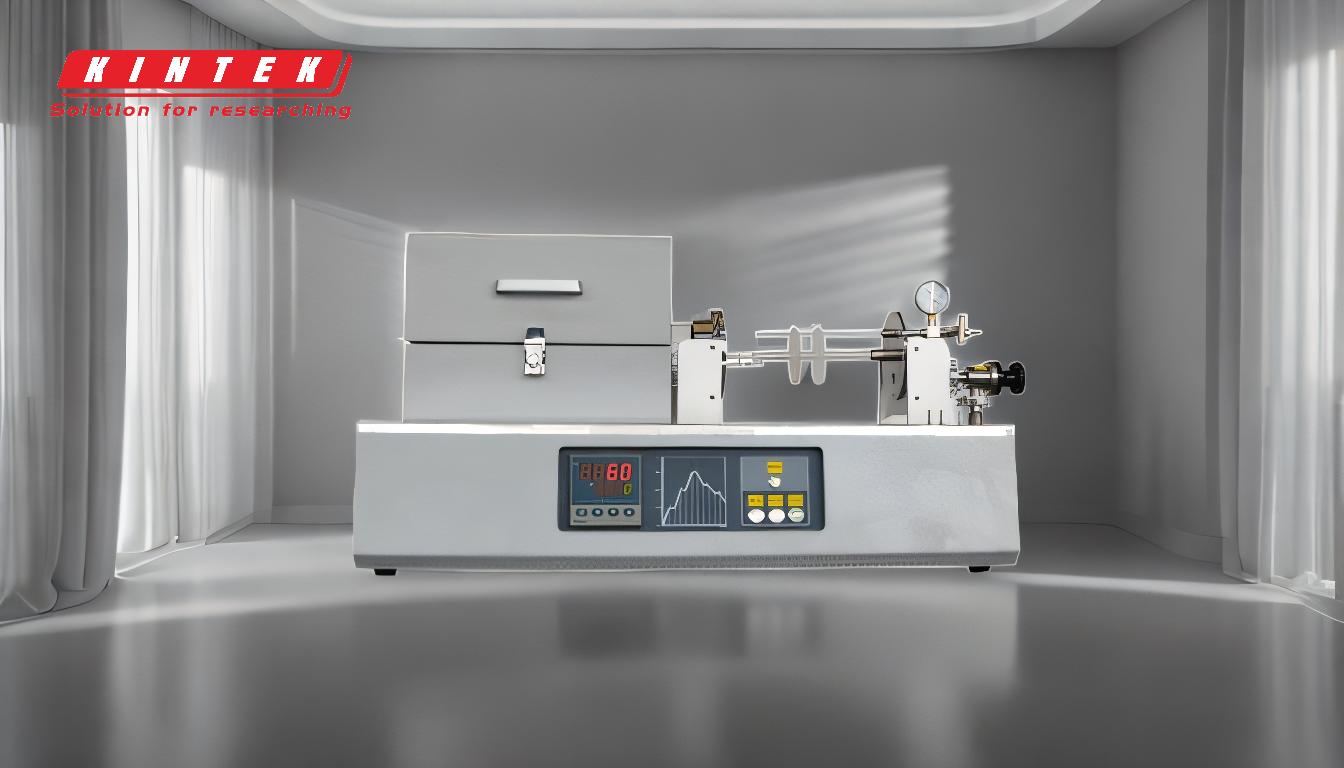
-
Selection of Materials:
- Base Metals: The primary metals that form the majority of the alloy.
- Alloying Elements: Additional elements added to modify properties like strength, corrosion resistance, or electrical conductivity.
- Purity and Quality: Ensuring materials are free from impurities that could affect the alloy's properties.
-
Preparation of Materials:
- Weighing and Measuring: Accurately measuring the proportions of each component to achieve the desired alloy composition.
- Cleaning: Removing any oxides, dirt, or contaminants from the metal surfaces to prevent defects in the final product.
-
Melting Process:
- Furnace Selection: Choosing the appropriate type of furnace (e.g., induction, arc, or crucible) based on the materials and desired outcome.
- Temperature Control: Precisely controlling the temperature to ensure all components melt uniformly without overheating or underheating.
- Atmosphere Control: Using inert gases or vacuum environments to prevent oxidation or contamination during melting.
-
Mixing and Homogenization:
- Stirring or Agitation: Ensuring the molten alloy is well-mixed to achieve a uniform composition.
- Degassing: Removing any dissolved gases that could cause porosity or weaken the alloy.
-
Pouring and Casting:
- Mold Preparation: Preparing molds that will shape the molten alloy into the desired form.
- Pouring Technique: Carefully pouring the molten alloy to avoid introducing air bubbles or other defects.
- Cooling Rate: Controlling the cooling rate to influence the microstructure and properties of the alloy.
-
Post-Processing:
- Heat Treatment: Applying additional heating and cooling cycles to enhance specific properties like hardness or toughness.
- Surface Finishing: Machining, polishing, or coating the alloy to achieve the final desired surface quality and dimensions.
-
Quality Control:
- Testing and Inspection: Conducting various tests (e.g., tensile strength, hardness, chemical composition) to ensure the alloy meets the required specifications.
- Documentation: Keeping detailed records of the process parameters and test results for traceability and quality assurance.
By following these steps meticulously, manufacturers can produce high-quality alloys with precise properties tailored to specific applications, ensuring reliability and performance in their end-use environments.
Summary Table:
Step | Key Actions |
---|---|
1. Material Selection | Choose base metals, alloying elements, and ensure purity and quality. |
2. Preparation | Accurately weigh, measure, and clean materials to prevent defects. |
3. Melting | Select the right furnace, control temperature, and use inert atmospheres. |
4. Mixing | Stir or agitate molten alloy for uniformity and degas to remove impurities. |
5. Casting | Prepare molds, pour carefully, and control cooling rates for desired properties. |
6. Post-Processing | Apply heat treatment and surface finishing for enhanced performance. |
7. Quality Control | Test, inspect, and document to ensure alloy meets specifications. |
Ready to create high-performance alloys? Contact our experts today for tailored solutions!