The process of molding a mold, particularly in the context of blow molding, involves transforming plastic into a desired shape using a mold. This process typically includes melting plastic into a preform, clamping it into a mold, inflating it with air to conform to the mold's shape, cooling the material, and finally ejecting the finished product. The three common methods of blow molding are extrusion, injection, and stretch blow molding, each with its own specific steps and applications.
Key Points Explained:
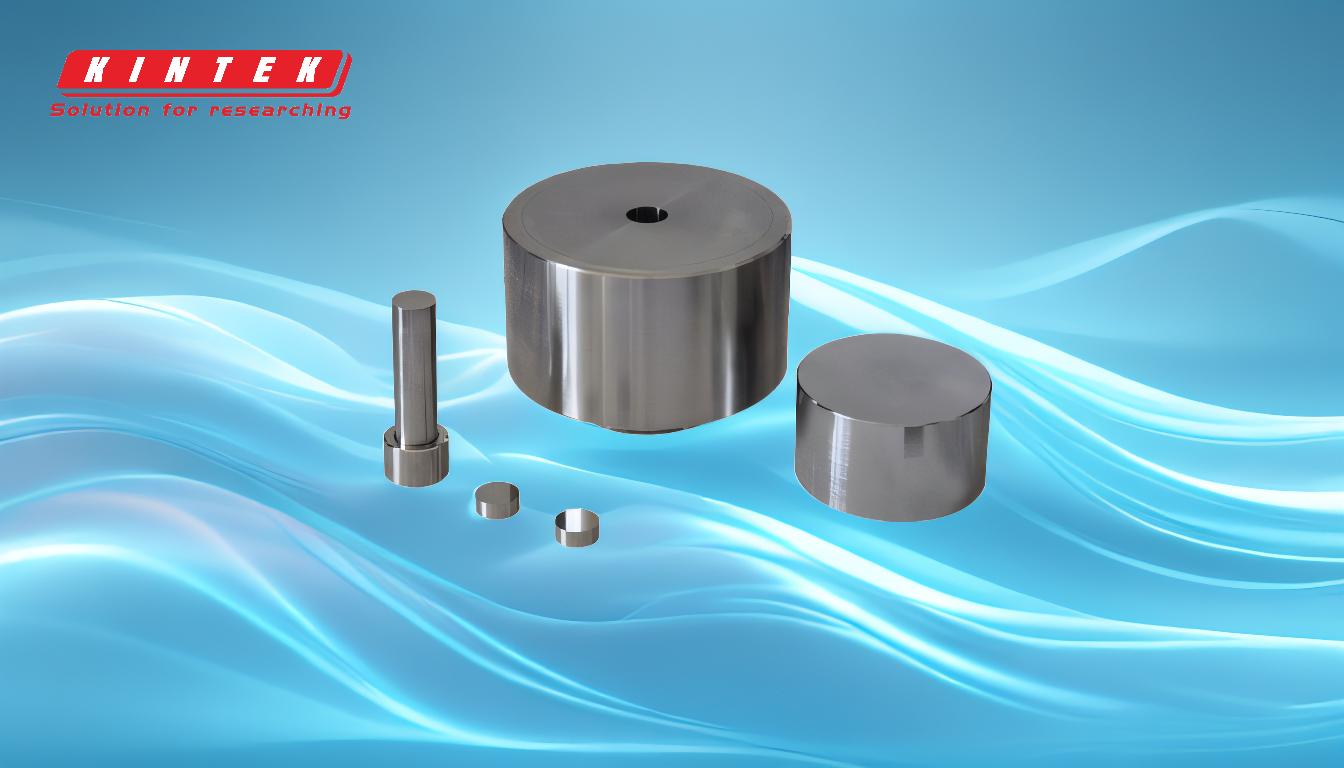
-
Melting Plastic into a Preform:
- The process starts with melting plastic pellets or resin to form a tube-shaped preform. This preform is the initial shape that will be further molded.
- The type of plastic used can vary depending on the desired properties of the final product, such as flexibility, strength, or transparency.
-
Clamping the Preform into a Mold:
- The preform is then clamped into a mold, which is designed to the exact specifications of the final product.
- The mold is typically made of metal and can be customized to produce a wide range of shapes and sizes.
-
Inflating the Preform with Air:
- Once the preform is securely clamped, air is pumped into it to push the plastic against the walls of the mold.
- This step ensures that the plastic takes on the exact shape of the mold, including any intricate details or textures.
-
Cooling the Molded Part:
- After the plastic has been shaped, it is allowed to cool within the mold. Cooling is crucial as it solidifies the plastic, ensuring that it retains its new shape.
- The cooling time can vary depending on the thickness of the plastic and the type of plastic used.
-
Ejecting the Finished Product:
- Once the plastic has cooled and solidified, the mold is opened, and the finished product is ejected.
- The product is then inspected for quality and any necessary finishing touches, such as trimming excess material or adding additional components.
-
Common Blow Molding Methods:
- Extrusion Blow Molding: This method involves extruding a tube of molten plastic (parison) into a mold and then inflating it. It is commonly used for producing hollow objects like bottles and containers.
- Injection Blow Molding: This process starts with injecting molten plastic into a preform mold. The preform is then transferred to a blow mold where it is inflated. This method is often used for small, precise items like medical bottles.
- Stretch Blow Molding: This technique involves stretching the preform both longitudinally and radially before blowing it into the mold. It is typically used for producing high-strength, lightweight containers, such as PET bottles.
By following these steps, manufacturers can produce a wide variety of plastic products with consistent quality and precision. Each method of blow molding has its own advantages and is chosen based on the specific requirements of the product being manufactured.
Summary Table:
Step | Description |
---|---|
Melting Plastic into a Preform | Plastic pellets are melted to form a tube-shaped preform, tailored to final product properties. |
Clamping into a Mold | The preform is clamped into a custom metal mold designed for the final shape. |
Inflating with Air | Air is pumped into the preform to push it against the mold walls for precise shaping. |
Cooling the Molded Part | The plastic cools within the mold to solidify and retain its shape. |
Ejecting the Finished Product | The cooled product is ejected, inspected, and finished as needed. |
Common Methods | Extrusion, Injection, and Stretch Blow Molding, each suited for specific product needs. |
Ready to optimize your plastic molding process? Contact our experts today for tailored solutions!