Plasma-Assisted Chemical Vapor Deposition (PACVD) is a specialized form of Chemical Vapor Deposition (CVD) that utilizes plasma to enhance the chemical reactions necessary for thin film deposition. This process is particularly useful for depositing high-quality films at lower temperatures compared to traditional CVD. PACVD combines the principles of CVD with plasma technology, enabling the deposition of a wide range of materials, including metals, semiconductors, and insulators, with precise control over film properties.
Key Points Explained:
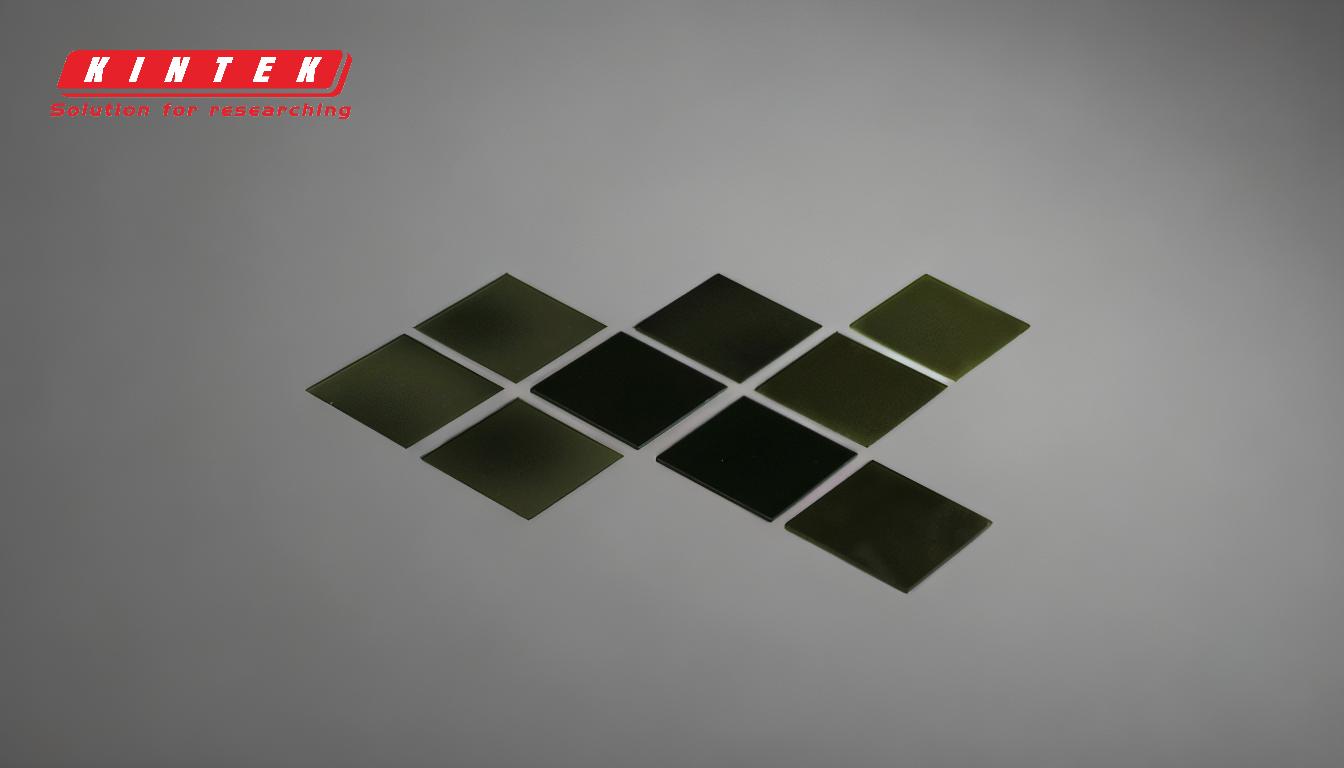
-
Introduction to PACVD:
- PACVD is a variant of CVD that uses plasma to activate the gas phase precursors, facilitating the deposition of thin films on substrates.
- The plasma provides the energy needed to break down the precursor molecules into reactive species, which then deposit onto the substrate.
-
Process Overview:
- Precursor Introduction: The process begins with the introduction of precursor gases into a reaction chamber. These gases are typically organic or inorganic compounds that contain the elements needed for the desired film.
- Plasma Generation: A plasma is generated within the chamber using an external energy source, such as radio frequency (RF) or microwave power. This plasma ionizes the precursor gases, creating highly reactive species.
- Film Deposition: The reactive species generated by the plasma interact with the substrate surface, leading to the formation of a thin film. The properties of the film can be controlled by adjusting parameters such as plasma power, gas flow rates, and substrate temperature.
-
Advantages of PACVD:
- Lower Deposition Temperatures: PACVD allows for the deposition of films at lower temperatures compared to traditional CVD, making it suitable for temperature-sensitive substrates.
- Enhanced Film Quality: The use of plasma can improve the quality of the deposited films, including better adhesion, higher density, and improved uniformity.
- Versatility: PACVD can be used to deposit a wide range of materials, including metals, semiconductors, and insulators, with precise control over film properties.
-
Applications of PACVD:
- Semiconductor Manufacturing: PACVD is widely used in the semiconductor industry for depositing thin films of materials such as silicon dioxide, silicon nitride, and various metals.
- Optical Coatings: The process is also used to deposit optical coatings, such as anti-reflective and protective coatings, on lenses and other optical components.
- Biomedical Applications: PACVD is employed in the biomedical field for coating medical devices with biocompatible materials, such as diamond-like carbon (DLC) coatings.
-
Challenges and Limitations:
- Complexity: The use of plasma adds complexity to the deposition process, requiring careful control of plasma parameters to achieve the desired film properties.
- Cost: The equipment required for PACVD is generally more expensive than that for traditional CVD, which can be a barrier to its adoption in some applications.
- Scalability: While PACVD is highly effective for small-scale applications, scaling up the process for large-scale production can be challenging.
In summary, PACVD is a powerful and versatile deposition technique that leverages plasma technology to enhance the CVD process. It offers several advantages, including lower deposition temperatures, improved film quality, and the ability to deposit a wide range of materials. However, it also presents challenges related to process complexity, cost, and scalability.
Summary Table:
Aspect | Details |
---|---|
Process Overview | Combines CVD with plasma technology for enhanced thin film deposition. |
Key Steps | 1. Precursor introduction 2. Plasma generation 3. Film deposition |
Advantages | Lower temperatures, improved film quality, versatile material deposition. |
Applications | Semiconductor manufacturing, optical coatings, biomedical devices. |
Challenges | Complexity, higher costs, scalability issues. |
Interested in PACVD for your applications? Contact us today to learn more!