Particle sintering is a critical manufacturing process used to transform powdered materials into dense, solid bodies by applying heat and pressure without reaching the material's melting point. This process involves several key steps: composition, compression, heating, and solidification. During sintering, particles are fused through diffusion, reducing porosity and creating a strong, durable material. It is widely used in industries such as powder metallurgy and ceramics to produce components with high strength and precision. The process can be enhanced through techniques like liquid phase sintering (LPS) or controlled atmospheres, depending on the material and desired properties.
Key Points Explained:
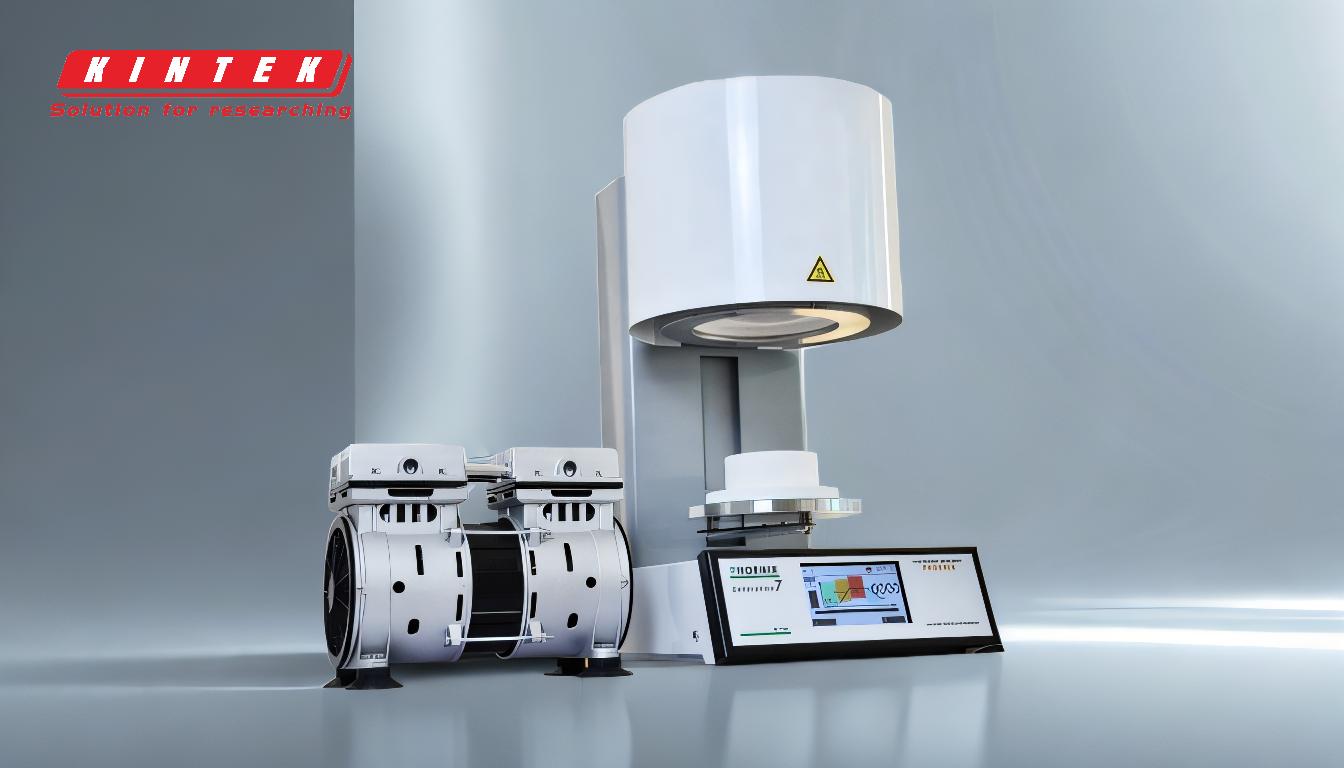
-
Composition and Mixing:
- The sintering process begins with the preparation of raw materials, which involves mixing primary powders with coupling agents or binders. These additives help in binding the particles together during the initial stages.
- The mixture is carefully formulated to achieve the desired properties in the final product, such as strength, density, or thermal conductivity.
-
Compression and Shaping:
- The mixed powder is then compressed into a specific shape using methods like cold pressing, 3D printing, or pressing tools. This step forms a "green compact," which is a loosely bonded structure.
- The compression process ensures that the particles are in close contact, which is essential for effective sintering.
-
Heating and Consolidation:
- The green compact is heated to a temperature just below the material's melting point. This step is crucial as it removes binders or coupling agents and initiates particle diffusion.
- During heating, atoms diffuse across particle boundaries, reducing surface area and local curvature. This diffusion leads to densification and the formation of a low-porosity structure.
- Techniques like liquid phase sintering (LPS) can be used to accelerate the process by introducing a liquid phase that enhances particle merging.
-
Particle Merging and Densification:
- As the temperature increases, particles begin to merge, and the material densifies. This stage is critical for achieving the desired mechanical properties, such as hardness and strength.
- The process may involve the activation of specific crystalline microstructures, such as martensitic structures in metals, which contribute to the material's final properties.
-
Cooling and Solidification:
- After the heating phase, the material is allowed to cool and solidify into a unified mass. This step ensures that the material retains its shape and achieves the desired structural integrity.
- Controlled cooling rates may be employed to optimize the material's microstructure and properties.
-
Applications and Benefits:
- Sintering is widely used in industries such as powder metallurgy, ceramics, and advanced manufacturing. It is particularly useful for materials with high melting points, such as tungsten and molybdenum.
- The process produces components with high precision, strength, and durability, making it ideal for applications in aerospace, automotive, and electronics.
-
Variations and Enhancements:
- Advanced sintering techniques, such as spark plasma sintering (SPS) or microwave sintering, can further enhance the process by reducing processing times or improving material properties.
- Controlled atmospheres (e.g., vacuum or inert gas) are often used to prevent oxidation or contamination during sintering.
By understanding these key steps and their underlying principles, manufacturers can optimize the sintering process to produce high-quality materials tailored to specific applications.
Summary Table:
Key Steps | Description |
---|---|
Composition and Mixing | Mix primary powders with binders to achieve desired properties like strength. |
Compression and Shaping | Compress powder into a shape (e.g., cold pressing) to form a green compact. |
Heating and Consolidation | Heat below melting point to remove binders and initiate particle diffusion. |
Particle Merging | Particles merge, reducing porosity and enhancing material strength. |
Cooling and Solidification | Cool to solidify into a unified mass with optimal microstructure. |
Applications | Used in powder metallurgy, ceramics, aerospace, and electronics for precision. |
Enhancements | Techniques like LPS, SPS, or controlled atmospheres improve sintering efficiency. |
Optimize your sintering process with expert guidance—contact us today!