The Physical Vapor Deposition (PVD) process is a vacuum-based thin-film coating technology widely used in semiconductor manufacturing. It involves the vaporization of a solid material, transportation of the vaporized particles to a substrate, and their subsequent condensation to form a thin, uniform layer. The process is performed under high-vacuum conditions and often at relatively low temperatures, making it suitable for delicate semiconductor substrates. PVD is essential for creating precise, high-quality coatings with excellent adhesion and uniformity, which are critical for semiconductor device performance. The process typically includes steps such as vapor generation, transportation, reaction (if applicable), and deposition onto the substrate.
Key Points Explained:
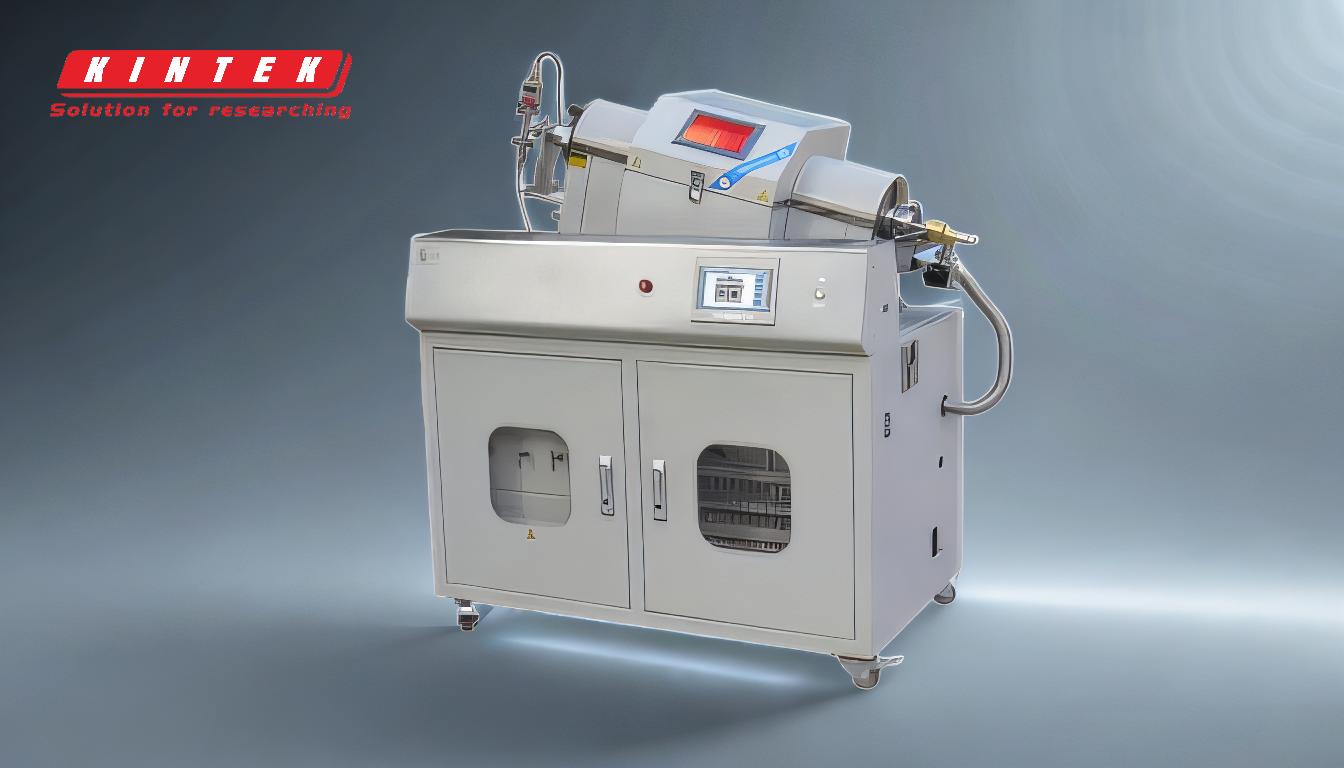
-
Vaporization of the Source Material:
- The first step in the PVD process involves converting a solid precursor material into a vapor. This is achieved through methods such as:
- Evaporation: Heating the source material until it vaporizes.
- Sputtering: Bombarding the target material with high-energy ions to dislodge atoms, creating a vapor.
- Laser ablation: Using a high-power laser to vaporize the material.
- The vaporization process occurs in a high-vacuum environment to minimize contamination and ensure the purity of the deposited layer.
- The first step in the PVD process involves converting a solid precursor material into a vapor. This is achieved through methods such as:
-
Transportation of Vaporized Particles:
- Once the source material is vaporized, the atoms, molecules, or ions are transported through the vacuum chamber to the substrate. This step involves:
- Ensuring a controlled environment to prevent unwanted reactions or contamination.
- Using plasma or reactive gases (if needed) to modify the properties of the vaporized particles.
- The transportation phase is critical for maintaining the integrity and uniformity of the vapor before deposition.
- Once the source material is vaporized, the atoms, molecules, or ions are transported through the vacuum chamber to the substrate. This step involves:
-
Reaction with Reactive Gases (Optional):
- In some PVD processes, a reactive gas is introduced to the vaporized particles to form a compound. This step is common in reactive PVD, where the goal is to deposit a compound material (e.g., nitrides or oxides) rather than a pure metal.
- The reactive gas chemically interacts with the vaporized particles, forming a compound that is then deposited onto the substrate.
-
Deposition onto the Substrate:
- The final step involves the condensation of the vaporized particles onto the substrate to form a thin, uniform layer. Key aspects of this step include:
- Adhesion: Ensuring strong bonding between the deposited layer and the substrate.
- Uniformity: Achieving a consistent thickness across the substrate.
- Crystallinity: Controlling the microstructure of the deposited layer to meet specific semiconductor performance requirements.
- The substrate is typically maintained at a lower temperature than the vaporized material to facilitate condensation.
- The final step involves the condensation of the vaporized particles onto the substrate to form a thin, uniform layer. Key aspects of this step include:
-
High-Vacuum Environment:
- The entire PVD process is conducted under high-vacuum conditions to:
- Minimize contamination from atmospheric gases.
- Enhance the control over the deposition process.
- Improve the quality and performance of the deposited thin film.
- The entire PVD process is conducted under high-vacuum conditions to:
-
Applications in Semiconductor Manufacturing:
- PVD is widely used in the semiconductor industry for:
- Depositing conductive layers (e.g., aluminum, copper) for interconnects.
- Creating barrier layers (e.g., titanium nitride) to prevent diffusion.
- Forming thin films for advanced semiconductor devices, such as transistors and memory cells.
- PVD is widely used in the semiconductor industry for:
-
Advantages of PVD:
- Precision: Enables the deposition of extremely thin and uniform layers.
- Material Versatility: Suitable for a wide range of materials, including metals, alloys, and compounds.
- Low Temperature: Reduces the risk of damaging temperature-sensitive substrates.
- High Purity: Minimizes contamination, ensuring high-quality coatings.
By understanding these key steps and considerations, semiconductor manufacturers can leverage PVD technology to produce high-performance devices with precise and reliable thin-film coatings.
Summary Table:
Key Steps in PVD Process | Details |
---|---|
Vaporization | Converts solid material into vapor via evaporation, sputtering, or ablation. |
Transportation | Vaporized particles move through a high-vacuum chamber to the substrate. |
Reaction (Optional) | Reactive gases may be used to form compound materials. |
Deposition | Vapor condenses onto the substrate, forming a thin, uniform layer. |
High-Vacuum Environment | Ensures minimal contamination and precise control over the process. |
Applications | Used for conductive layers, barrier layers, and advanced semiconductor devices. |
Advantages | Precision, material versatility, low temperature, and high purity. |
Discover how PVD can enhance your semiconductor manufacturing—contact us today for expert guidance!