Sieve analysis is a widely used method to determine the particle size distribution of granular materials. The process involves separating a sample into different size fractions using a stack of sieves with progressively smaller mesh sizes. The material retained on each sieve is weighed, and the percentage of the total sample in each size fraction is calculated. This method provides a quick and reliable analysis of particle size distribution, which is crucial for quality control and material characterization in various industries. The process includes steps such as sampling, sample preparation, sieving, weighing, and data evaluation, all of which must be performed with precision to ensure accurate results.
Key Points Explained:
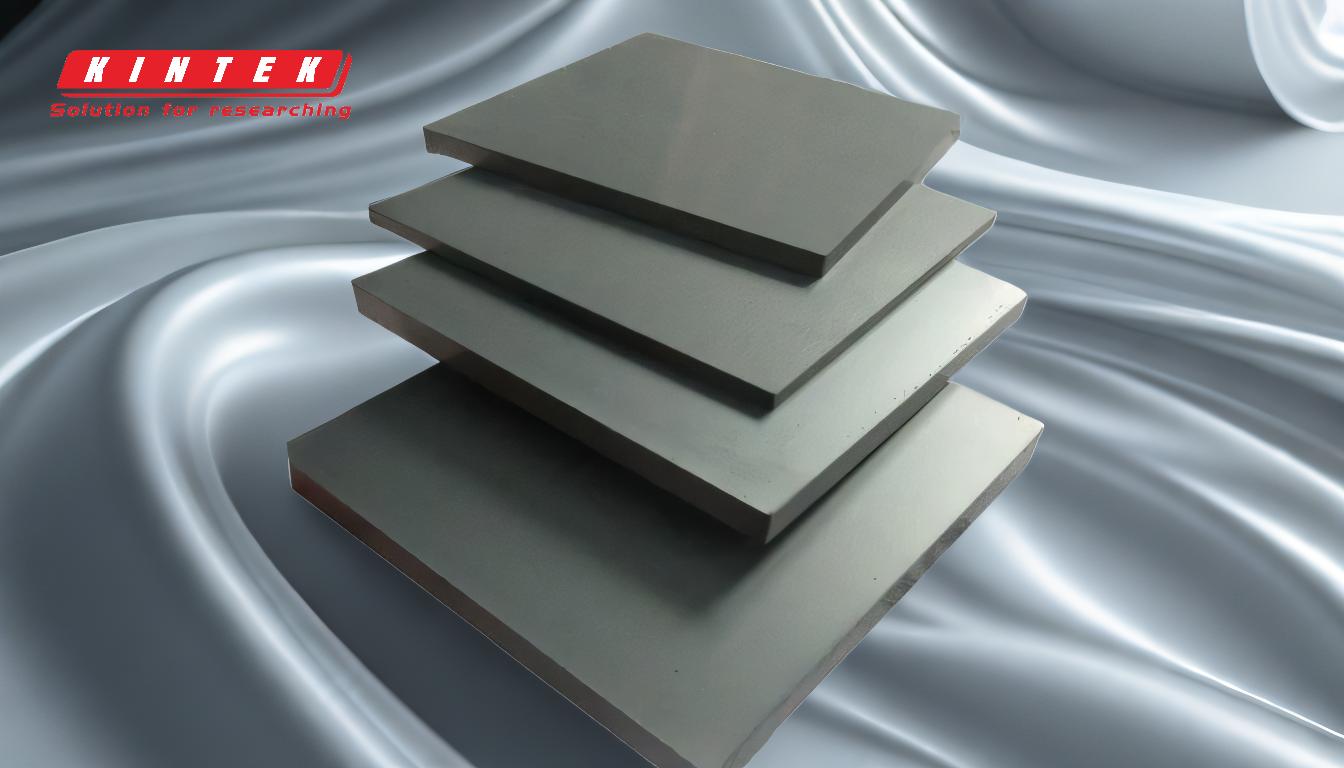
-
Method Development:
- Selection of Standard Method: The first step in sieve analysis is to choose a suitable standard method based on the material being tested and the desired accuracy. Different industries may have specific standards (e.g., ASTM, ISO) that dictate the procedure.
- Selection of Sieves: The appropriate sieves are selected based on the expected particle size distribution. Sieves are typically arranged in a stack with the largest mesh size at the top and the smallest at the bottom.
-
Preparation of Sieves:
- Pre-recording Identification and Tare Weight: Before starting the analysis, each sieve must be identified, and its tare weight (empty weight) recorded. This ensures that any material retained on the sieve can be accurately weighed later.
- Cleaning and Drying: Sieves should be cleaned and dried to remove any residual material from previous tests, ensuring that the results are not contaminated.
-
Sampling:
- Representative Sample: A representative sample of the material is taken to ensure that the results reflect the overall particle size distribution of the entire batch. The sample size should be appropriate for the sieve stack being used.
-
Sample Preparation:
- Pre-drying and Conditioning: Depending on the material, the sample may need to be dried or conditioned to remove moisture, which can affect the sieving process.
- Sample Division: If the sample is too large, it may be divided into smaller, more manageable portions using a sample splitter or other dividing techniques.
-
Weighing Sieves Empty:
- Tare Weighing: Each sieve is weighed empty to determine its tare weight. This step is crucial for calculating the weight of the material retained on each sieve after sieving.
-
Adding the Sample:
- Loading the Sieve Stack: The prepared sample is placed on the top sieve of the stack. The stack is then assembled, ensuring that the sieves are securely fastened to prevent material loss during shaking.
-
Sieving:
- Manual or Mechanical Shaking: The sieve stack is shaken either manually or using a mechanical sieve shaker. The shaking action allows particles smaller than the mesh size to pass through to the next sieve.
- Duration of Shaking: The sieving process continues for a predetermined amount of time or until no further material passes through the sieves. This ensures that the particles are adequately separated by size.
-
Back Weighing Fractions:
- Weighing Retained Material: After sieving, the material retained on each sieve is carefully collected and weighed. The weight of the material on each sieve is recorded, and the tare weight is subtracted to determine the net weight of the retained material.
- Calculating Percentages: The mass of the material retained on each sieve is divided by the total mass of the sample to calculate the percentage of the sample in each size fraction.
-
Result Analysis, Evaluation, and Interpretation:
- Data Evaluation: The results are evaluated to determine the particle size distribution. This may involve plotting a particle size distribution curve or calculating statistical parameters such as the mean particle size or the uniformity coefficient.
- Interpretation: The results are interpreted in the context of the material's intended use. For example, in construction, the particle size distribution of aggregates can affect the strength and workability of concrete.
-
Cleaning and Drying the Test Sieves:
- Post-analysis Cleaning: After the analysis, the sieves are cleaned to remove any residual material. This is important to prevent cross-contamination between different samples.
- Drying: The sieves are dried to ensure they are ready for the next use. Proper maintenance of sieves is essential for consistent and accurate results over time.
By following these steps meticulously, sieve analysis provides a reliable method for determining the particle size distribution of granular materials, which is essential for quality control and material characterization in various industries.
Summary Table:
Step | Key Action |
---|---|
Method Development | Choose standard method (e.g., ASTM, ISO) and select appropriate sieves. |
Preparation of Sieves | Record tare weight, clean, and dry sieves to avoid contamination. |
Sampling | Take a representative sample to reflect overall particle distribution. |
Sample Preparation | Dry and condition the sample, then divide if necessary. |
Weighing Sieves Empty | Weigh each sieve empty to determine tare weight. |
Adding the Sample | Load the sample onto the top sieve and secure the stack. |
Sieving | Shake manually or mechanically to separate particles by size. |
Back Weighing Fractions | Weigh retained material and calculate percentages for each size fraction. |
Result Analysis | Evaluate data and interpret results for material characterization. |
Cleaning and Drying | Clean and dry sieves post-analysis to maintain accuracy. |
Need accurate sieve analysis for your materials? Contact our experts today for reliable results!