Silicon deposition is a critical process in thin-film technology, primarily used to create thin layers of silicon on substrates for applications in electronics, photovoltaics, and other high-tech industries. The process involves depositing silicon atoms onto a substrate using methods such as chemical vapor deposition (CVD) and physical vapor deposition (PVD). These methods are chosen based on the desired film properties, such as thickness, purity, and electrical conductivity. CVD relies on chemical reactions to deposit silicon, while PVD uses physical processes like vaporization and condensation. Both methods have their advantages and are selected based on specific application requirements.
Key Points Explained:
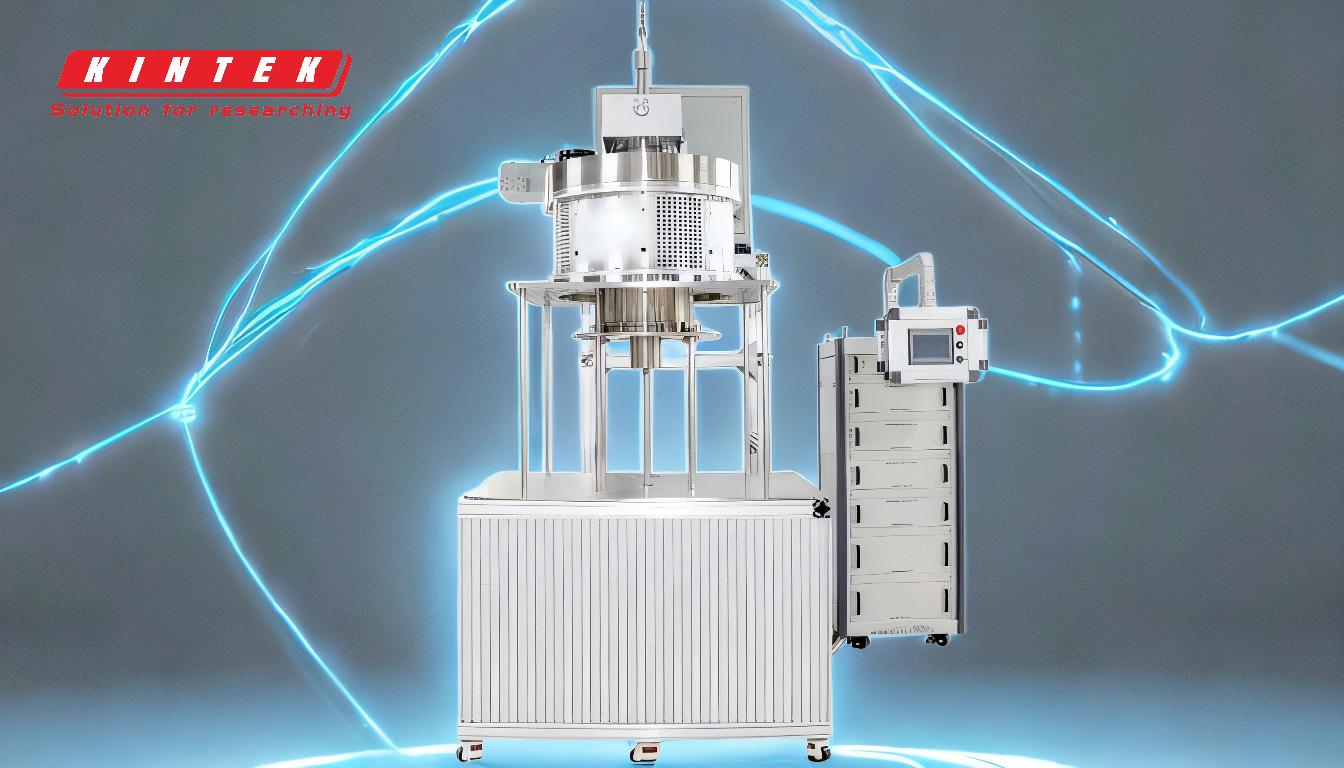
-
Overview of Silicon Deposition:
- Silicon deposition is a process used to create thin silicon films on substrates, which are essential in manufacturing semiconductors, solar cells, and other electronic devices.
- The process involves depositing silicon atoms onto a surface, either through chemical reactions or physical processes, to form a uniform and high-quality film.
-
Chemical Vapor Deposition (CVD):
- CVD is a widely used method for silicon deposition, where reactant gases are introduced into a chamber containing the substrate.
- Chemical reactions occur on the substrate surface, leading to the formation of a solid silicon film.
- This method is favored for its ability to produce high-purity and uniform films, which are crucial for applications requiring precise electrical properties.
-
Physical Vapor Deposition (PVD):
- PVD involves the physical vaporization of a silicon source material in a vacuum, which then condenses onto the substrate to form a thin film.
- Unlike CVD, PVD does not involve chemical reactions, making it suitable for applications where chemical contamination must be minimized.
- PVD is often used for depositing thin films with specific structural and mechanical properties.
-
Comparison of CVD and PVD:
- CVD Advantages: Produces high-purity films, excellent uniformity, and can deposit complex structures. It is ideal for applications requiring high electrical conductivity and precise control over film properties.
- PVD Advantages: Does not involve chemical reactions, reducing the risk of contamination. It is suitable for depositing thin films with specific mechanical properties and is often used in applications where thermal and chemical stability are critical.
-
Applications of Silicon Deposition:
- Silicon deposition is essential in the production of semiconductors, where thin silicon films are used to create transistors and other electronic components.
- In photovoltaics, silicon deposition is used to manufacture solar cells, where the thin films enhance light absorption and electrical conductivity.
- Other applications include optical coatings, sensors, and MEMS (Micro-Electro-Mechanical Systems).
-
Future Trends in Silicon Deposition:
- Advances in deposition techniques are focusing on improving film quality, reducing production costs, and enabling the deposition of thinner and more complex structures.
- Emerging technologies, such as atomic layer deposition (ALD), are being explored for their potential to achieve even greater precision and control in silicon deposition processes.
In summary, silicon deposition is a versatile and essential process in modern technology, with CVD and PVD being the primary methods used. Each method has its unique advantages and is chosen based on the specific requirements of the application. As technology advances, new deposition techniques are being developed to further enhance the performance and efficiency of silicon-based devices.
Summary Table:
Aspect | CVD | PVD |
---|---|---|
Process Type | Chemical reactions on substrate surface | Physical vaporization and condensation |
Key Advantages | High-purity films, excellent uniformity, complex structures | No chemical reactions, minimal contamination, specific mechanical properties |
Applications | Semiconductors, solar cells, high electrical conductivity | Optical coatings, sensors, MEMS, thermal and chemical stability |
Discover how silicon deposition can enhance your high-tech applications—contact our experts today!