Sintering ceramics is a multi-step process that transforms powdered ceramic materials into dense, solid structures through heat and pressure without melting the material. The process involves preparing a ceramic powder mixture, forming it into a desired shape (green body), and then heating it to high temperatures to fuse the particles together. This results in a dense, low-porosity ceramic product with enhanced mechanical strength and durability. The process is critical for creating high-performance ceramics used in various industries, including electronics, aerospace, and medical applications.
Key Points Explained:
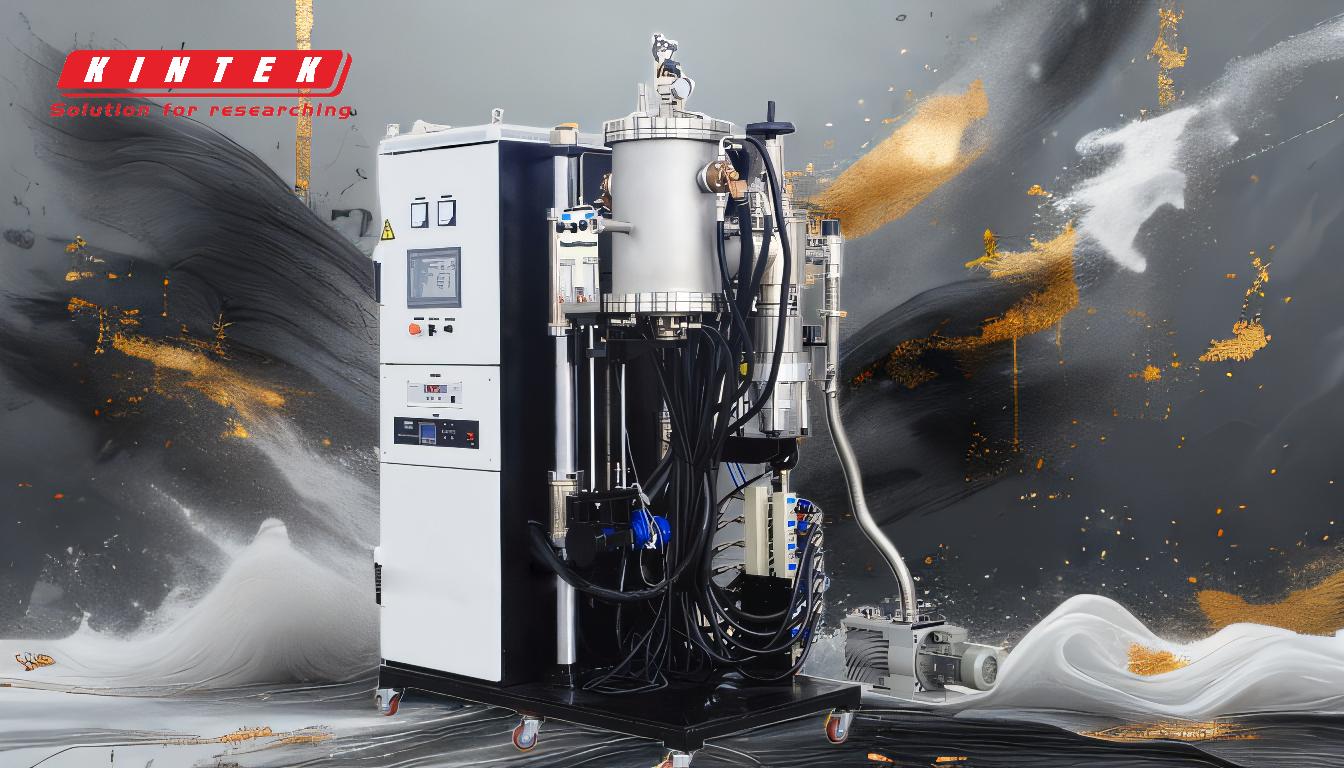
-
Powder Composition and Preparation:
- The process begins with the preparation of a ceramic powder mixture. This involves mixing raw ceramic powders with additives such as binders, deflocculants, and water to form a slurry. The binders help hold the particles together, while deflocculants prevent the particles from clumping.
- The slurry is then spray-dried to create a free-flowing powder that is easier to handle and press into molds.
-
Forming the Green Body:
- The spray-dried powder is pressed into a mold using mechanical methods such as cold or hot pressing. This step shapes the powder into a "green body," which is a fragile, unfired ceramic structure.
- The green body retains the desired shape but lacks the strength and density of the final product. It is crucial to handle the green body carefully to avoid cracks or deformations.
-
Binder Burn-Off (Debinding):
- Before sintering, the green body is heated to a low temperature to remove the organic binders used during the forming process. This step, known as debinding, is essential to prevent defects in the final product.
- The temperature is carefully controlled to ensure complete removal of the binder without damaging the green body.
-
Sintering (Firing):
- The green body is then heated to a high temperature, typically just below the melting point of the ceramic material, in a controlled atmosphere (e.g., in a tunnel kiln or periodic kiln).
- During sintering, the ceramic particles undergo diffusion and grain boundary movement, leading to particle densification and fusion. This results in a dense, low-porosity ceramic product with improved mechanical properties.
- The sintering process can be enhanced using techniques like liquid phase sintering (LPS), where a small amount of liquid phase accelerates particle merging.
-
Cooling and Solidification:
- After sintering, the ceramic product is gradually cooled to room temperature. This step is critical to prevent thermal stress and cracking.
- The cooling rate is controlled to ensure the material solidifies into a unified, dense mass with the desired microstructure and properties.
-
Factors Influencing Sintering:
- Temperature and Time: The sintering temperature and duration must be carefully controlled to achieve optimal densification without over-sintering, which can lead to grain growth and reduced strength.
- Atmosphere: The sintering atmosphere (e.g., air, vacuum, or inert gas) affects the final properties of the ceramic. For example, sintering in a reducing atmosphere can prevent oxidation of certain materials.
- Powder Characteristics: The size, shape, and distribution of the ceramic particles influence the sintering behavior. Finer particles generally sinter more easily due to their higher surface energy.
-
Applications of Sintered Ceramics:
- Sintered ceramics are used in a wide range of applications, including:
- Electronics: For substrates, insulators, and capacitors.
- Aerospace: For heat shields and engine components.
- Medical: For implants and dental prosthetics.
- Industrial: For cutting tools, wear-resistant parts, and filters.
- Sintered ceramics are used in a wide range of applications, including:
By understanding and optimizing each step of the sintering process, manufacturers can produce high-quality ceramic materials tailored to specific applications. The process requires precise control of parameters such as temperature, pressure, and atmosphere to achieve the desired material properties.
Summary Table:
Step | Description |
---|---|
Powder Preparation | Mix ceramic powders with binders, deflocculants, and water to form a slurry. |
Forming Green Body | Press the powder into a mold to create a fragile, unfired ceramic structure. |
Debinding | Heat to remove binders, ensuring no defects in the final product. |
Sintering | Heat to high temperatures to fuse particles, creating a dense ceramic product. |
Cooling | Gradually cool to solidify the material and prevent thermal stress. |
Applications | Used in electronics, aerospace, medical, and industrial sectors. |
Optimize your ceramic sintering process—contact our experts today for tailored solutions!