Sintering finishing is a critical process in materials science and manufacturing, where powdered materials are transformed into dense, solid bodies through the application of heat and pressure, without reaching the melting point of the material. This process is widely used in industries such as powder metallurgy, ceramics, and plastics to create strong, durable, and low-porosity components. The sintering process involves several stages, including powder preparation, compaction, heating, particle merging, and solidification. Each step is carefully controlled to ensure the final product meets the desired specifications for strength, density, and structural integrity.
Key Points Explained:
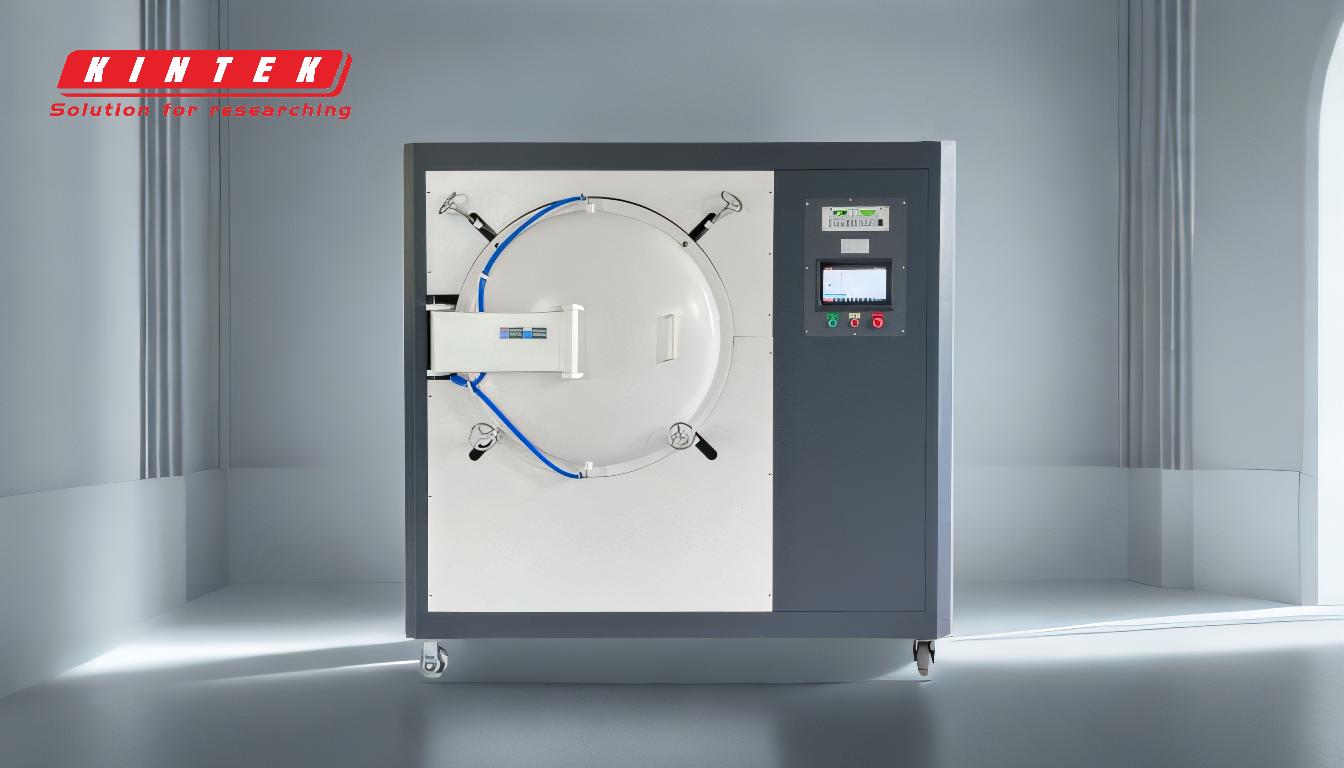
-
Definition and Purpose of Sintering:
- Sintering is a process that transforms powdered materials into dense, solid bodies by applying heat and pressure below the material's melting point.
- It is used to create strong, durable, and low-porosity components in industries like powder metallurgy, ceramics, and plastics.
-
Preparation of the Powder Compact:
- The first step involves preparing the powder compact, which can be done using methods such as cold welds, 3D-printed lasers, or pressing tools.
- This step is crucial for ensuring the powder is uniformly distributed and ready for the subsequent heating and consolidation stages.
-
Heating and Consolidation:
- The powder compact is heated to a temperature just below the material's melting point.
- This heating activates martensitic crystalline microstructures, which are essential for the material's strength and durability.
- The controlled atmosphere during heating prevents oxidation and other undesirable reactions.
-
Particle Merging and Densification:
- As the material is heated, the particles begin to merge and densify.
- This process can be accelerated using techniques like liquid phase sintering (LPS), where a liquid phase forms between particles, facilitating faster densification.
- The goal is to reduce porosity and create a solid, unified mass.
-
Solidification:
- After the particles have merged and densified, the material is allowed to cool and solidify.
- This final stage ensures the material retains its shape and structural integrity, resulting in a strong, durable product.
-
Composition and Compression:
- The sintering process often begins with the composition stage, where primary materials and coupling agents are mixed.
- The powder is then compressed into the required shape using pressing tools.
- This step ensures the material is uniformly distributed and ready for the heating process.
-
Applications of Sintering:
- Sintering is used in a variety of applications, including the production of metal components, ceramics, and plastics.
- It is particularly useful for materials with high melting points, such as tungsten and molybdenum, where traditional melting and casting methods are impractical.
-
Advantages of Sintering:
- Sintering allows for the creation of complex shapes and structures that would be difficult or impossible to achieve with other manufacturing methods.
- The process results in materials with high strength, durability, and low porosity, making them ideal for demanding applications.
By following these steps, the sintering process transforms powdered materials into high-quality, durable components that meet the rigorous demands of various industries. Each stage of the process is carefully controlled to ensure the final product meets the desired specifications for strength, density, and structural integrity.
Summary Table:
Stage | Description |
---|---|
Powder Preparation | Powder is uniformly distributed and compacted using methods like cold welds or pressing tools. |
Heating & Consolidation | Compact is heated below melting point, activating microstructures for strength. |
Particle Merging | Particles merge and densify, reducing porosity and forming a solid mass. |
Solidification | Material cools and solidifies, retaining shape and structural integrity. |
Applications | Used in metal components, ceramics, and plastics, especially for high-melting-point materials. |
Advantages | Creates complex shapes, high strength, durability, and low porosity. |
Discover how sintering can enhance your manufacturing process—contact our experts today for tailored solutions!