The metal sintering process is a method used to create solid metal components from powdered metal. It involves several stages, including powder preparation, compaction, and heating in a controlled environment to bond the particles together. The process begins with blending powdered metals with additives, followed by compacting the powder into a desired shape. The compacted part is then heated in a sintering furnace to a temperature just below the metal's melting point, allowing the particles to bond and form a solid structure. The final product is a dense, low-porosity metal component with structural integrity.
Key Points Explained:
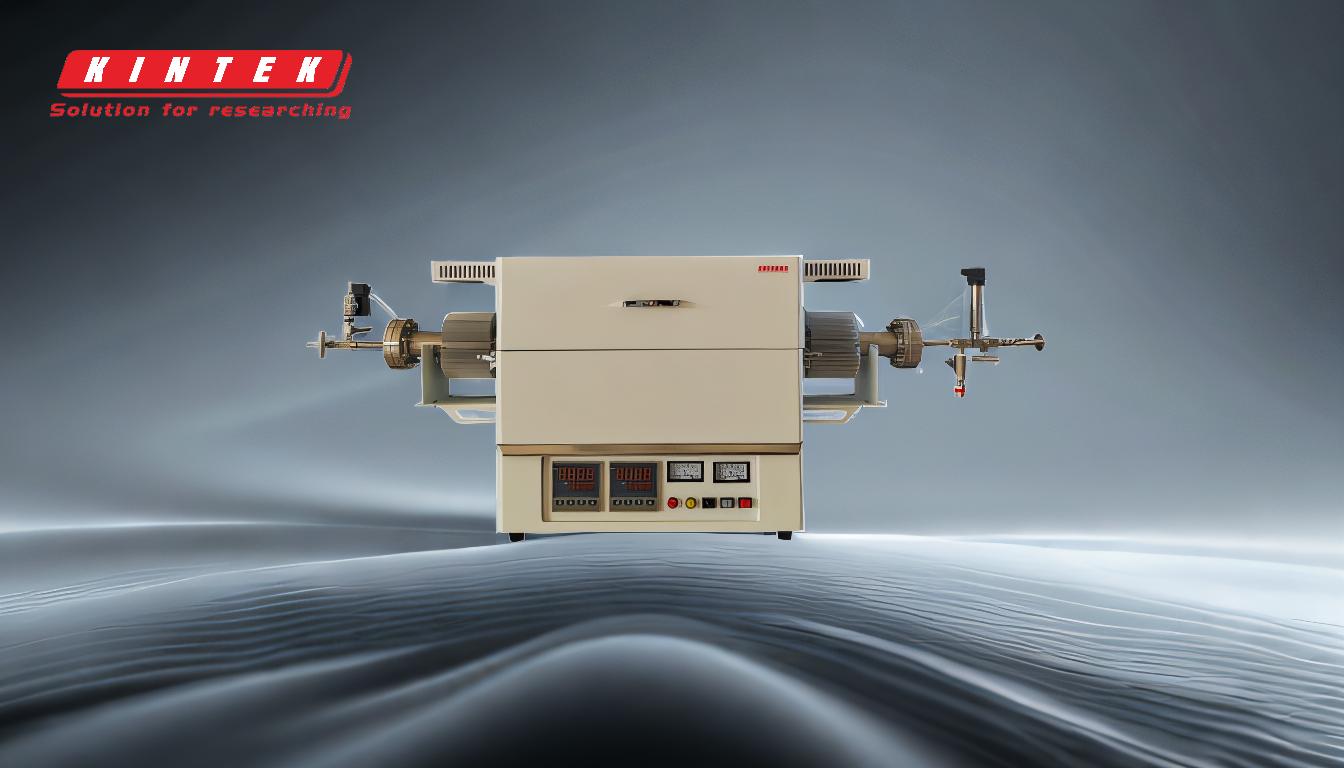
-
Powder Preparation and Blending:
- Powder Composition: The process begins with the preparation of metal powders, which may include primary metals, alloying elements, and additives. These powders are often mixed with water, deflocculants, and binders to create a uniform slurry.
- Blending: The powdered metals are blended with alloying elements and additives to ensure a homogeneous mixture. This step is crucial for achieving the desired material properties in the final product.
-
Compaction:
- Cold or Hot Pressing: The blended powder is then compacted into a desired shape using high-pressure tools. This can be done either at room temperature (cold pressing) or at elevated temperatures (hot pressing). The compaction process forms a "green part," which is a loosely bonded structure that holds its shape but lacks strength.
- Mechanical Densification: During compaction, the powder particles are pressed together, reducing the porosity and increasing the density of the green part. This step is essential for creating a uniform and dense structure before sintering.
-
Sintering:
- Heating and Bonding: The green part is placed in a sintering furnace, where it is heated to a temperature just below the melting point of the metal. This heating process causes the particles to bond together through diffusion, forming a solid structure.
-
Stages of Sintering:
- Initial Stage: The material is heated to create martensitic, crystalline structures without complete compaction. This stage involves the removal of lubricants and the reduction of oxides.
- Intermediate Stage: The particle density increases, and the particles begin to merge. This can be accelerated using methods like transient liquid phase sintering (TLPS) or permanent liquid phase sintering (LPS).
- Final Stage: The material becomes mostly solid, with any remaining pores being filled by liquid and binder additives. This stage ensures the final product has low porosity and high structural integrity.
-
Cooling and Solidification:
- Cooling: After sintering, the material is cooled in a controlled manner to solidify the structure. This step is crucial for achieving the desired mechanical properties and dimensional stability.
- Solidification: The cooling process allows the material to solidify into a unified mass, resulting in a dense, low-porosity metal component with the desired shape and properties.
-
Additional Considerations:
- Liquid Phase Sintering (LPS): In some cases, a liquid phase is introduced during sintering to enhance particle bonding and densification. This is particularly useful for materials that are difficult to sinter using solid-state methods.
- Binder Additives: Binders are often added to the powder mixture to improve the green part's strength and handling properties. These binders are typically removed during the sintering process through thermal decomposition.
- Controlled Atmosphere: Sintering is often performed in a controlled atmosphere (e.g., vacuum or inert gas) to prevent oxidation and ensure the quality of the final product.
By following these steps, the metal sintering process transforms powdered metals into solid, high-strength components suitable for various industrial applications. The process is highly customizable, allowing for the production of complex shapes and tailored material properties.
Summary Table:
Stage | Key Details |
---|---|
Powder Preparation | Blending metal powders with additives for a homogeneous mixture. |
Compaction | Cold or hot pressing to form a 'green part' with reduced porosity. |
Sintering | Heating below melting point to bond particles and form a solid structure. |
Cooling & Solidification | Controlled cooling to achieve desired mechanical properties and stability. |
Additional Considerations | Use of liquid phase sintering, binders, and controlled atmospheres for quality. |
Interested in optimizing your metal sintering process? Contact us today for expert guidance!