Thin film deposition is a critical process in materials science and engineering, used to create thin layers of material on a substrate. The process can be broadly categorized into two main methods: Physical Vapor Deposition (PVD) and Chemical Vapor Deposition (CVD). PVD involves the physical vaporization of a solid material in a vacuum, which then condenses onto a substrate to form a thin film. CVD, on the other hand, relies on chemical reactions between gaseous precursors to deposit a solid film on the substrate. Both methods have various sub-techniques, each suited for specific applications and materials. The process typically involves several key steps, including material selection, transport, deposition, and post-treatment, to ensure the desired film properties are achieved.
Key Points Explained:
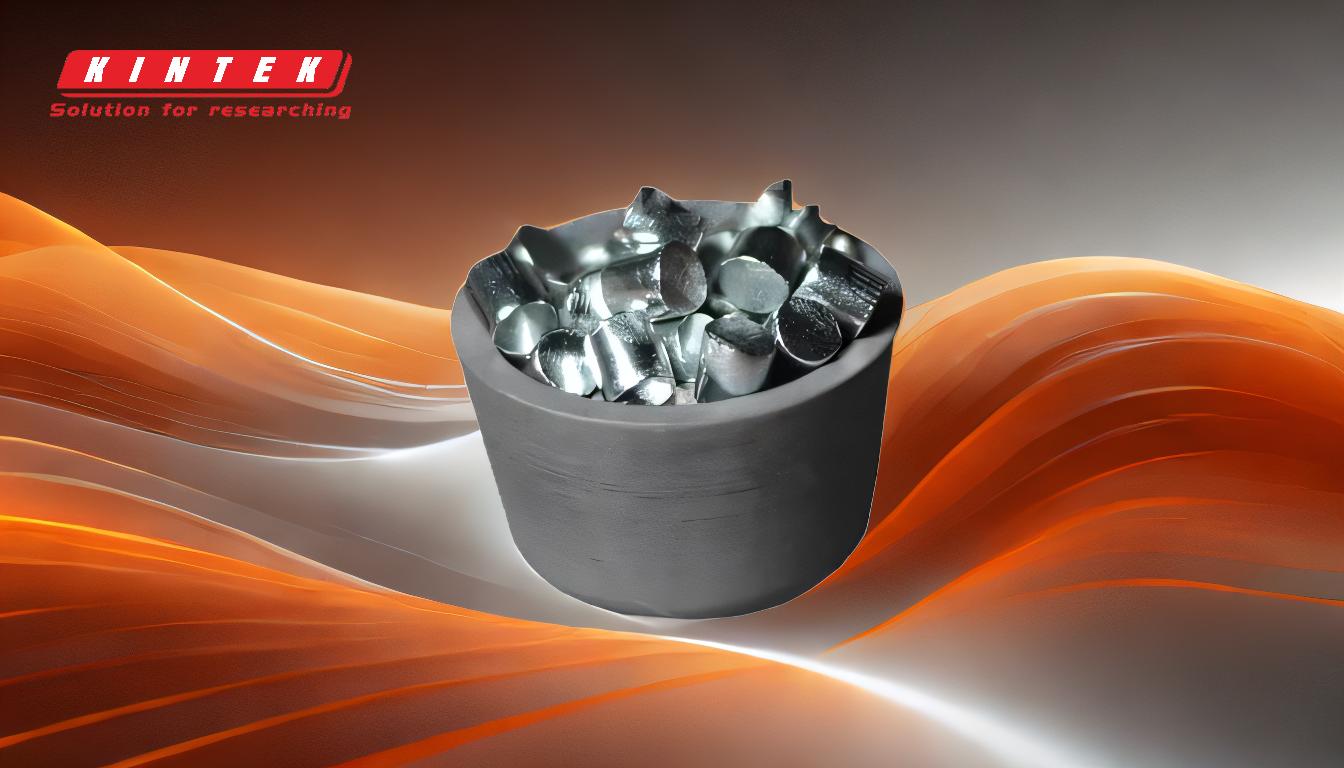
-
Categories of Thin Film Deposition Methods:
-
Physical Vapor Deposition (PVD):
- Definition: PVD involves the physical vaporization of a solid material in a vacuum, which then condenses onto a substrate to form a thin film.
- Techniques: Common PVD techniques include sputtering, thermal evaporation, electron beam evaporation, molecular beam epitaxy (MBE), and pulsed laser deposition (PLD).
- Applications: PVD is widely used in the semiconductor industry, for coatings on tools, and in the production of optical and electronic devices.
-
Chemical Vapor Deposition (CVD):
- Definition: CVD involves the use of chemical reactions between gaseous precursors to deposit a solid film on a substrate.
- Techniques: Techniques include standard CVD, plasma-enhanced CVD (PECVD), and atomic layer deposition (ALD).
- Applications: CVD is used for creating high-purity, high-performance thin films in applications such as semiconductor manufacturing, solar cells, and protective coatings.
-
Physical Vapor Deposition (PVD):
-
Steps in the Thin Film Deposition Process:
-
Material Selection:
- The process begins with selecting a pure material source (target) that will be deposited as a thin film.
-
Transport:
- The target material is transported to the substrate through a medium, which could be a fluid or a vacuum, depending on the deposition method.
-
Deposition:
- The material is deposited onto the substrate to form a thin film. This step varies significantly between PVD and CVD methods.
-
Post-Treatment:
- After deposition, the film may undergo annealing or heat treatment to improve its properties, such as adhesion, density, and crystallinity.
-
Analysis and Modification:
- The properties of the deposited film are analyzed, and the deposition process may be modified to achieve the desired characteristics.
-
Material Selection:
-
Detailed Explanation of PVD and CVD Techniques:
-
PVD Techniques:
- Sputtering: A high-energy plasma is used to eject atoms from a target material, which then deposit onto the substrate.
- Thermal Evaporation: The target material is heated until it vaporizes, and the vapor condenses onto the substrate.
- Electron Beam Evaporation: An electron beam is used to heat the target material, causing it to evaporate and deposit onto the substrate.
- Molecular Beam Epitaxy (MBE): A highly controlled process where beams of atoms or molecules are directed at the substrate to grow epitaxial layers.
- Pulsed Laser Deposition (PLD): A high-power laser pulse is used to ablate material from a target, which then deposits onto the substrate.
-
CVD Techniques:
- Standard CVD: Reactant gases are introduced into a chamber, where they react on the substrate surface to form a solid film.
- Plasma-Enhanced CVD (PECVD): A plasma is used to enhance the chemical reactions, allowing deposition at lower temperatures.
- Atomic Layer Deposition (ALD): A sequential, self-limiting process where alternating pulses of precursor gases are used to deposit one atomic layer at a time.
-
PVD Techniques:
-
Applications and Importance of Thin Film Deposition:
- Semiconductor Industry: Thin films are essential for the fabrication of integrated circuits, transistors, and other electronic components.
- Optical Coatings: Thin films are used to create anti-reflective coatings, mirrors, and filters for optical devices.
- Solar Cells: Thin film deposition is used to create layers in photovoltaic cells, improving their efficiency and flexibility.
- Protective Coatings: Thin films provide wear resistance, corrosion protection, and thermal insulation in various industrial applications.
- Flexible Electronics: Techniques like ALD are used to deposit thin films on flexible substrates, enabling the development of flexible solar cells and OLEDs.
In conclusion, thin film deposition is a versatile and essential process in modern technology, with a wide range of methods and applications. Understanding the differences between PVD and CVD, as well as the specific techniques within each category, is crucial for selecting the appropriate method for a given application. The process involves several key steps, from material selection to post-treatment, each of which must be carefully controlled to achieve the desired film properties.
Summary Table:
Aspect | Details |
---|---|
Categories | Physical Vapor Deposition (PVD), Chemical Vapor Deposition (CVD) |
PVD Techniques | Sputtering, Thermal Evaporation, Electron Beam Evaporation, MBE, PLD |
CVD Techniques | Standard CVD, Plasma-Enhanced CVD (PECVD), Atomic Layer Deposition (ALD) |
Key Steps | Material Selection, Transport, Deposition, Post-Treatment, Analysis & Modification |
Applications | Semiconductors, Optical Coatings, Solar Cells, Protective Coatings, Flexible Electronics |
Need help choosing the right thin film deposition method for your project? Contact our experts today!