Thin film formation is a sophisticated process involving the deposition of material layers onto a substrate, often at the atomic or molecular level. The process is critical in industries such as semiconductors, optics, and energy, where precise control over film thickness and properties is essential. The main methods of thin film deposition are categorized into chemical and physical techniques. Chemical methods include processes like chemical vapor deposition (CVD), plasma-enhanced CVD (PECVD), and atomic layer deposition (ALD). Physical methods, primarily physical vapor deposition (PVD), encompass techniques such as sputtering, thermal evaporation, and electron beam evaporation. The process typically involves selecting a pure material source, transporting it to a substrate, depositing it to form a thin film, and optionally annealing the film to enhance its properties. Each method offers unique advantages and is chosen based on the desired film characteristics and application requirements.
Key Points Explained:
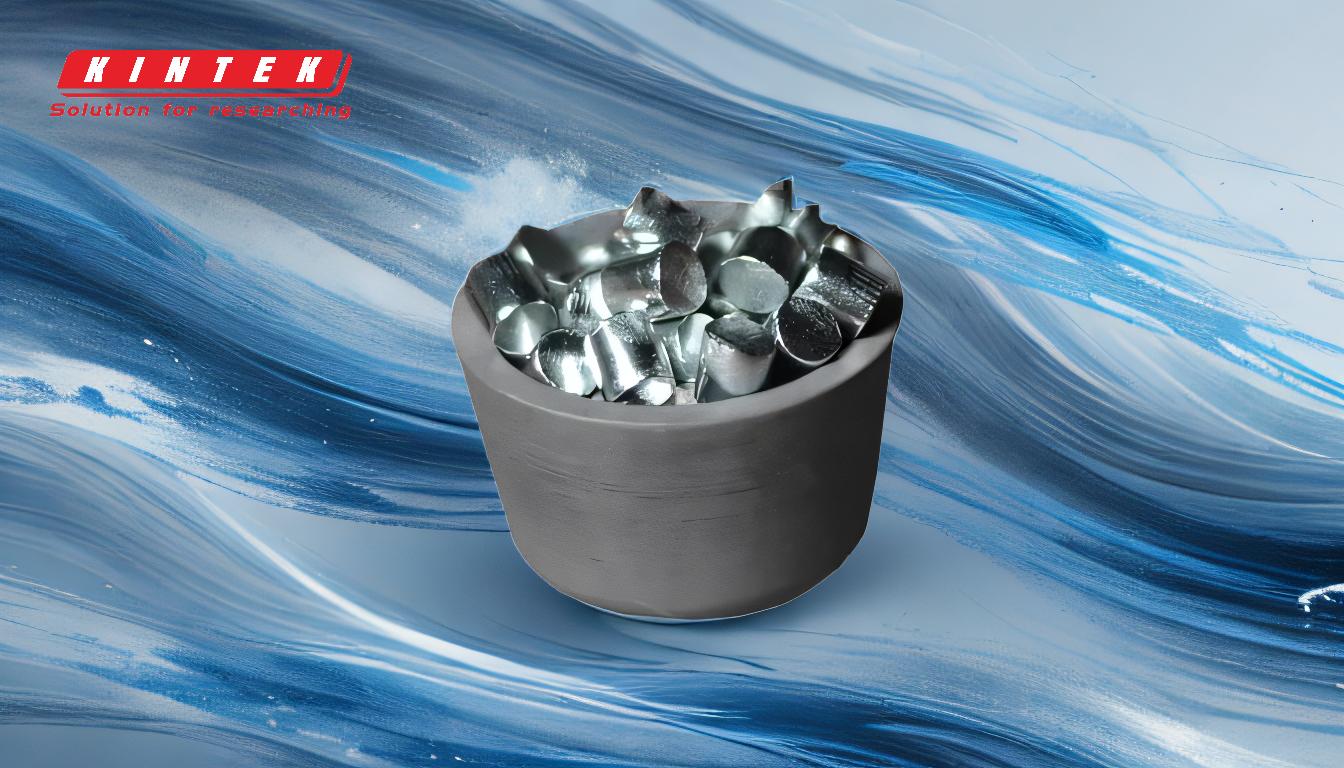
-
Categories of Thin Film Deposition Methods:
-
Chemical Methods:
- Chemical Vapor Deposition (CVD): Involves chemical reactions to produce high-purity thin films. Precursor gases react on the substrate surface to form the film.
- Plasma-Enhanced CVD (PECVD): Uses plasma to enhance chemical reactions, allowing deposition at lower temperatures.
- Atomic Layer Deposition (ALD): A sequential process where atomic layers are deposited one at a time, offering precise thickness control.
- Electroplating, Sol-Gel, Dip Coating, Spin Coating: These methods involve chemical solutions or gels to form thin films through various application techniques.
-
Physical Methods:
- Physical Vapor Deposition (PVD): Involves vaporizing a solid material in a vacuum and depositing it onto a substrate.
- Sputtering: A PVD technique where high-energy particles bombard a target material, causing atoms to be ejected and deposited onto the substrate.
- Thermal Evaporation: Material is heated to its evaporation point in a vacuum, and the vapor condenses on the substrate.
- Electron Beam Evaporation: Uses an electron beam to heat and evaporate the material, providing high deposition rates and purity.
- Molecular Beam Epitaxy (MBE): A highly controlled process where beams of atoms or molecules are directed onto the substrate to grow epitaxial films.
- Pulsed Laser Deposition (PLD): A laser pulse vaporizes the target material, which then deposits onto the substrate.
-
Chemical Methods:
-
Steps in the Thin Film Deposition Process:
- Selection of Material Source (Target): Choosing a pure material that will form the thin film.
- Transportation to Substrate: Moving the material to the substrate through a medium, often a vacuum or fluid.
- Deposition onto Substrate: The material is deposited onto the substrate to form a thin film. This can involve various techniques depending on the chosen method.
- Optional Annealing or Heat Treatment: The film may be subjected to heat treatment to improve its properties, such as crystallinity or adhesion.
- Analysis and Modification: The film's properties are analyzed, and the deposition process may be modified to achieve the desired characteristics.
-
Applications and Importance:
- Semiconductors: Thin films are crucial in the fabrication of semiconductor devices, where precise control over film thickness and composition is essential.
- Optics: Used in anti-reflective coatings, mirrors, and filters, where optical properties must be finely tuned.
- Energy: Applications include flexible solar cells and OLEDs, where thin films enable lightweight, flexible, and efficient energy devices.
- Protective Coatings: Thin films provide protective layers against corrosion, wear, and environmental damage.
-
Advantages of Different Deposition Methods:
- CVD and PECVD: Offer high purity and conformal coatings, suitable for complex geometries.
- ALD: Provides atomic-level control, ideal for ultra-thin films and complex structures.
- PVD (Sputtering, Evaporation): Offers high deposition rates and good adhesion, suitable for a wide range of materials.
- Spin Coating and Dip Coating: Simple and cost-effective for large-area coatings, though less precise in thickness control.
-
Considerations for Equipment and Consumable Purchasers:
- Material Compatibility: Ensure the chosen method is compatible with the materials to be deposited.
- Film Quality and Uniformity: Consider the required film properties, such as thickness, purity, and uniformity.
- Process Scalability: Evaluate the scalability of the deposition method for production volumes.
- Cost and Efficiency: Balance the cost of equipment and consumables with the efficiency and quality of the deposition process.
- Environmental and Safety Factors: Consider the environmental impact and safety requirements of the deposition method, especially for chemical processes.
In summary, the process of thin film formation involves a variety of chemical and physical deposition methods, each with its own set of advantages and applications. The choice of method depends on the desired film properties, material compatibility, and specific application requirements. Understanding these processes is crucial for equipment and consumable purchasers to make informed decisions that align with their production goals and quality standards.
Summary Table:
Category | Methods | Key Advantages |
---|---|---|
Chemical Methods | CVD, PECVD, ALD, Electroplating, Sol-Gel, Dip Coating, Spin Coating | High purity, conformal coatings, atomic-level control, cost-effective for large areas |
Physical Methods | PVD (Sputtering, Thermal Evaporation, Electron Beam Evaporation), MBE, PLD | High deposition rates, good adhesion, precise control, suitable for wide materials |
Ready to optimize your thin film deposition process? Contact our experts today for tailored solutions!