Deposition in semiconductor manufacturing is a critical process that involves the application of thin layers of materials onto a substrate, which is essential for creating the intricate structures and components of semiconductor devices. The purpose of deposition is multifaceted, aiming to enhance the electrical, thermal, and mechanical properties of the semiconductor, as well as to protect and insulate different layers within the device. The aerosol deposition method, in particular, stands out for its ability to deposit materials at low or room temperatures, making it suitable for substrates that are sensitive to high temperatures, such as those with low melting points or polymers. This method opens up new possibilities for semiconductor applications by allowing for the use of a wider range of materials and substrates, thereby expanding the potential for innovation in high-technology semiconductor devices.
Key Points Explained:
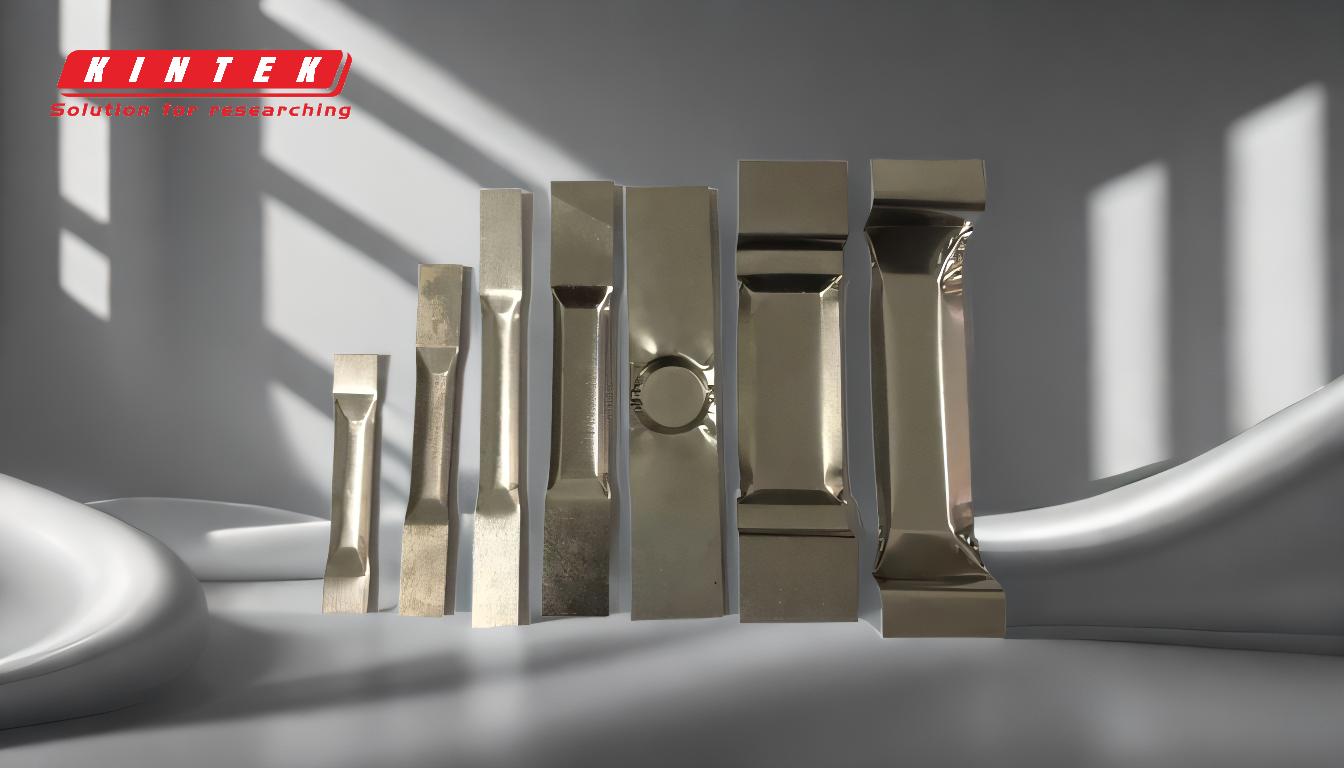
-
Enhancing Semiconductor Properties:
- Deposition is used to improve the electrical, thermal, and mechanical properties of semiconductors. By adding thin layers of specific materials, the performance of semiconductor devices can be significantly enhanced. For example, deposition can be used to create conductive pathways, insulating layers, or protective coatings that prevent damage from environmental factors.
-
Low-Temperature Deposition:
- Traditional deposition methods often require high temperatures, which can be detrimental to certain substrates. The aerosol deposition method, however, allows for deposition at low or room temperatures. This is particularly beneficial for substrates that are sensitive to heat, such as polymers or materials with low melting points, enabling the use of a broader range of materials in semiconductor fabrication.
-
Versatility in Material Application:
- The ability to deposit materials at lower temperatures opens up new possibilities for the types of materials that can be used in semiconductor devices. This versatility is crucial for the development of advanced semiconductor applications, as it allows for the integration of materials that were previously unsuitable due to their sensitivity to high temperatures.
-
Innovation in High-Technology Applications:
- The aerosol deposition method provides a new perspective for high-technology semiconductor applications. By enabling the use of a wider variety of materials and substrates, this method facilitates the creation of more complex and innovative semiconductor devices. This is particularly important in fields such as microelectronics, where the demand for smaller, more efficient, and more powerful devices is constantly growing.
-
Protection and Insulation:
- Deposition is also used to create protective and insulating layers within semiconductor devices. These layers are essential for preventing electrical shorts, protecting the device from environmental damage, and ensuring the long-term reliability of the semiconductor. The ability to deposit these layers at low temperatures ensures that the integrity of the substrate is maintained, even when using heat-sensitive materials.
In summary, deposition in semiconductor manufacturing serves a crucial role in enhancing the properties of semiconductor devices, enabling the use of a wider range of materials, and facilitating innovation in high-technology applications. The aerosol deposition method, with its low-temperature capabilities, is particularly valuable for expanding the possibilities in semiconductor fabrication, making it a key technique in the development of advanced semiconductor technologies.
Summary Table:
Purpose of Deposition | Key Benefits |
---|---|
Enhancing Properties | Improves electrical, thermal, and mechanical performance of semiconductors. |
Low-Temperature Deposition | Enables use of heat-sensitive materials like polymers and low-melting substrates. |
Versatility in Materials | Expands material options for advanced semiconductor applications. |
High-Tech Innovation | Facilitates creation of complex, efficient, and powerful semiconductor devices. |
Protection and Insulation | Prevents electrical shorts and environmental damage, ensuring device reliability. |
Learn how deposition can revolutionize your semiconductor processes—contact our experts today!