Physical Vapor Deposition (PVD) is a versatile thin film deposition technique used to create highly durable and resistant coatings on various substrates. The primary purpose of PVD is to enhance the performance attributes of materials by improving their resistance to high temperatures, oxidation, friction, and wear. It is widely applied in industries such as aerospace, electronics, optics, and medical devices, where thin films are required for mechanical, optical, chemical, or electronic functions. PVD coatings are known for their durability, precision, and ability to reflect surfaces well without additional polishing.
Key Points Explained:
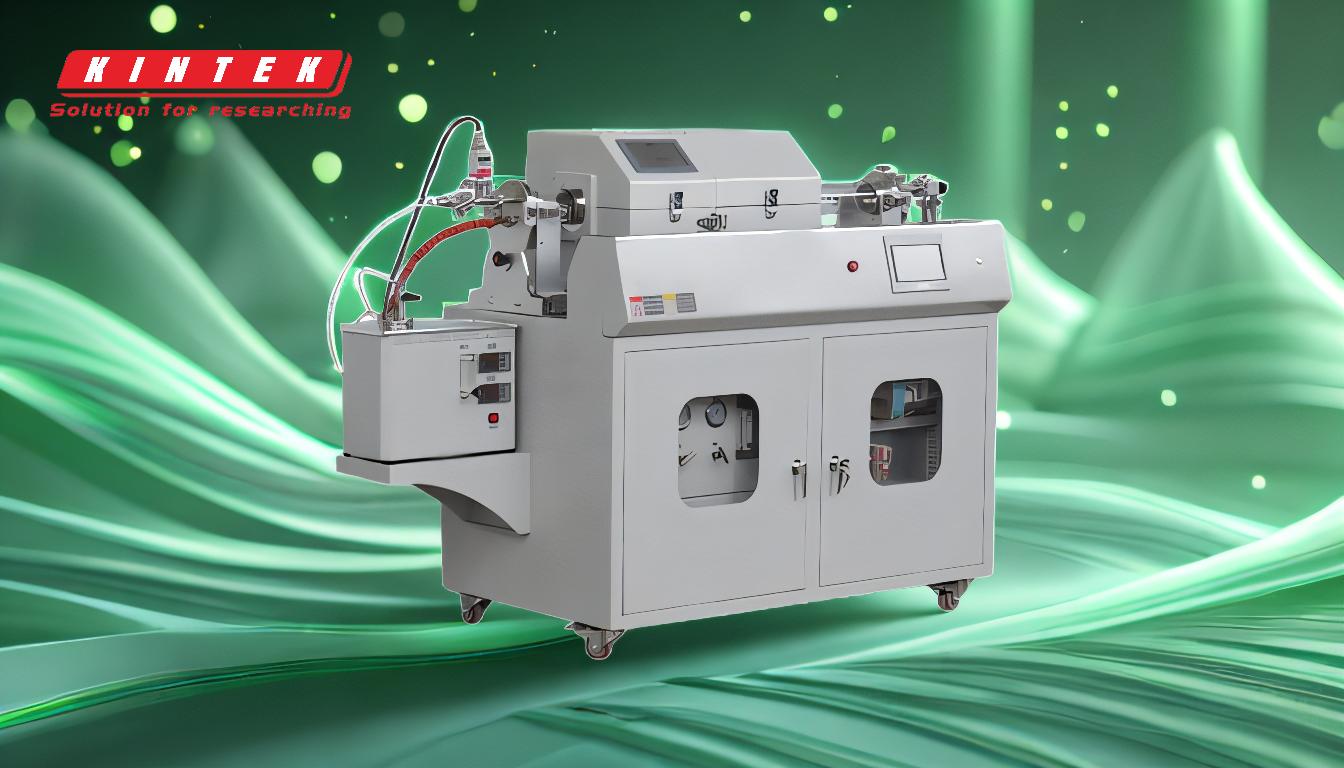
-
Enhancing Material Performance:
- PVD is used to improve the resistance of substrates to high temperatures, oxidation, and wear. This makes it ideal for applications in harsh environments, such as aerospace technology and high-temperature industrial processes.
- By depositing thin films, PVD enhances the hardness and durability of substrates, making them more resistant to mechanical stress and abrasion.
-
Reducing Friction and Improving Wear Resistance:
- PVD coatings are effective in reducing friction between moving parts, which is critical in machinery and automotive applications.
- The process improves wear resistance, extending the lifespan of tools and components exposed to constant mechanical stress.
-
Applications in Various Industries:
- Semiconductor and Electronics: PVD is used to create thin films for semiconductor devices, microchips, and solar panels, ensuring precise and durable coatings.
- Optics: It is employed in the production of optical lenses and decorative coatings, where high reflectivity and durability are essential.
- Medical Devices: PVD coatings are used to enhance the performance and biocompatibility of medical instruments and implants.
- Aerospace: The technique is applied to create diffusion barrier layers and coatings that withstand extreme conditions.
-
Process Characteristics:
- PVD involves vaporizing a solid material in a vacuum environment and depositing it onto a substrate. This process does not involve chemical reactions, ensuring the purity and integrity of the coating.
- Common methods of vaporization include evaporation, high-power electricity, and laser ablation, allowing for precise control over the deposition process.
-
Advantages of PVD Coatings:
- Durability: PVD coatings are highly resistant to wear, corrosion, and high temperatures.
- Precision: The process allows for the creation of thin, uniform films with controlled thickness and composition.
- Aesthetic Quality: PVD coatings reflect surfaces well and do not require additional polishing to achieve a metallic luster, making them ideal for decorative applications.
-
Environmental and Economic Benefits:
- PVD is a clean and environmentally friendly process, as it does not involve harmful chemicals or produce significant waste.
- The durability of PVD coatings reduces the need for frequent replacements, leading to cost savings over time.
In summary, PVD is a critical technology for enhancing the performance, durability, and functionality of materials across a wide range of industries. Its ability to create precise, durable, and high-quality coatings makes it indispensable for applications requiring advanced material properties.
Summary Table:
Key Aspect | Details |
---|---|
Purpose | Enhances resistance to high temperatures, oxidation, friction, and wear. |
Applications | Aerospace, electronics, optics, medical devices, and more. |
Process Characteristics | Vaporization in a vacuum, no chemical reactions, high precision. |
Advantages | Durable, precise, aesthetic, environmentally friendly, cost-effective. |
Learn how PVD can revolutionize your material performance—contact us today!