Sintering is a critical process in materials science and manufacturing, primarily used to join metal particles without requiring them to reach their melting points. This makes it particularly useful for metals with high melting points. Sintering is widely employed in powder metallurgy to create durable metal components like gears, bearings, and automotive parts. It is also integral to 3D printing, enabling the layer-by-layer formation of custom metal shapes with energy efficiency and precision. Additionally, sintering reduces surface porosity, enhancing material properties such as strength and durability. Beyond metals, sintering is used in ceramics and plastics, including the production of filters and other specialized components.
Key Points Explained:
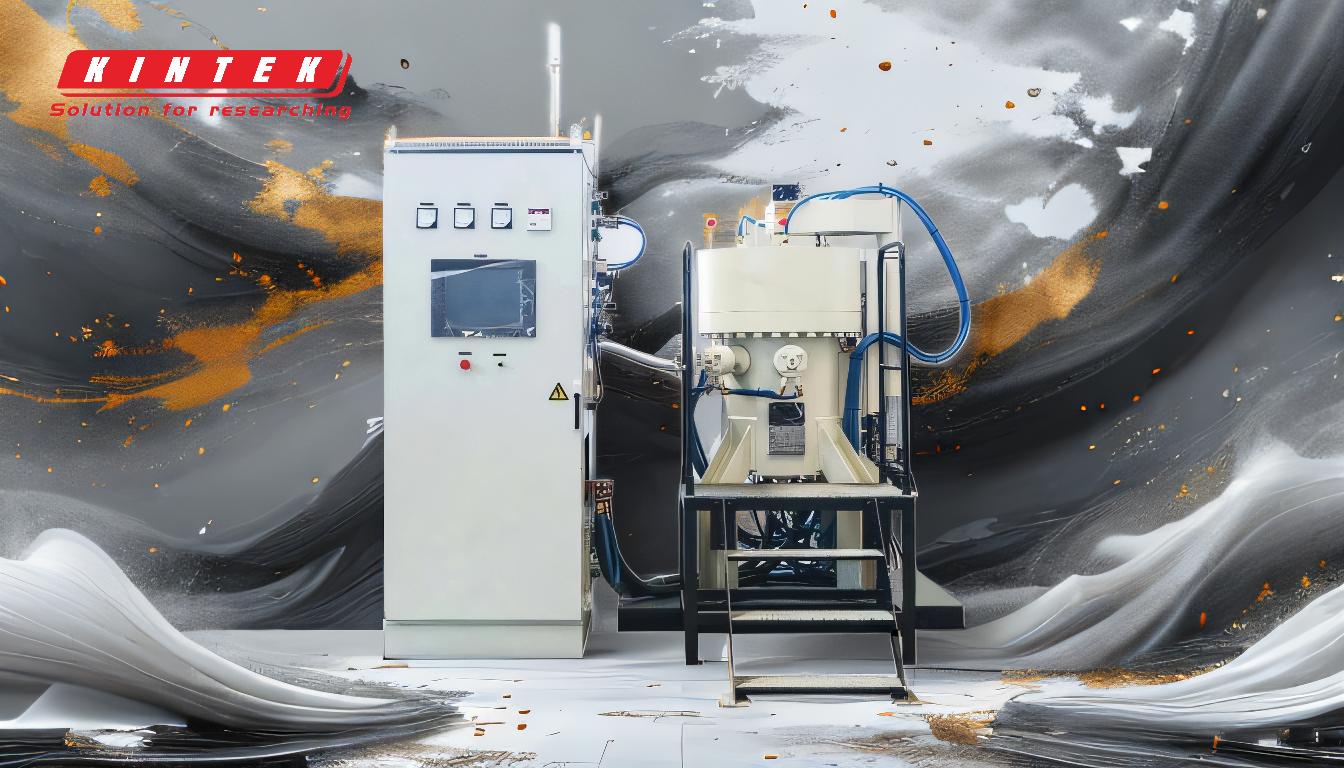
-
Joining Metal Particles Without Melting:
- Sintering binds metal particles together through heat and compaction without reaching the melting point of the material.
- This is especially beneficial for metals with high melting points, as it avoids the energy-intensive process of melting.
- Example: Iron, aluminum, and stainless steel powders are sintered to create solid, durable components like gears and bearings.
-
Applications in 3D Printing:
- Sintering is used in additive manufacturing (3D printing) to create custom metal shapes layer by layer.
- This method saves energy compared to traditional melting techniques and allows for greater control and consistency in the final product.
- Example: Sintering in 3D printing is used to produce complex geometries that are difficult to achieve with conventional methods.
-
Reduction of Surface Porosity:
- Sintering reduces the porosity of a material's surface, improving its mechanical properties such as strength, durability, and wear resistance.
- This is particularly important for components that require high performance under stress.
- Example: Sintered metal parts used in automotive applications benefit from reduced porosity, enhancing their longevity and reliability.
-
Flexibility in Manufacturing:
- Sintering is more flexible than traditional manufacturing techniques like casting, forging, and extrusion because it does not require solid-liquid phase changes.
- This flexibility allows for the creation of components that would otherwise decompose or lose integrity during melting.
- Example: Sintering enables the production of intricate parts with consistent material properties, which are challenging to achieve with other methods.
-
Applications Beyond Metals:
- Sintering is not limited to metals; it is also used in ceramics and plastics.
- In ceramics, sintering is traditionally used to create durable and heat-resistant objects.
- In plastics, sintering is employed to produce specialized components like sintered plastic filters.
- Example: Sintered PE (polyethylene) filters are widely used in filtration systems due to their high efficiency and durability.
-
Energy Efficiency and Precision:
- Sintering is an energy-efficient process compared to melting, as it operates at lower temperatures.
- The precision of sintering allows for the production of parts with consistent properties and complex geometries.
- Example: In powder metallurgy, sintering ensures that metal powders are uniformly compacted and bonded, resulting in parts with excellent mechanical properties.
-
Wide Range of Industrial Applications:
- Sintering is used in various industries, including automotive, aerospace, and structural engineering, to manufacture high-performance components.
- It is also applied in the production of filters, bearings, and other specialized parts.
- Example: Sintered metal components are integral to the automotive industry, where they are used in engines, transmissions, and other critical systems.
By understanding these key points, it becomes clear that sintering is a versatile and essential process in modern manufacturing, offering significant advantages in terms of energy efficiency, material properties, and design flexibility.
Summary Table:
Key Aspect | Description |
---|---|
Joining Without Melting | Binds metal particles through heat and compaction, avoiding high melting points. |
3D Printing Applications | Enables layer-by-layer creation of custom metal shapes with energy efficiency. |
Reduced Surface Porosity | Enhances strength, durability, and wear resistance of materials. |
Flexibility in Manufacturing | Allows production of intricate parts without solid-liquid phase changes. |
Applications Beyond Metals | Used in ceramics and plastics, e.g., sintered PE filters for filtration systems. |
Energy Efficiency | Operates at lower temperatures, saving energy compared to melting. |
Industrial Applications | Widely used in automotive, aerospace, and structural engineering industries. |
Learn how sintering can revolutionize your manufacturing process—contact our experts today!