An electric arc furnace (EAF) is a specialized melting furnace primarily used in the steel industry to melt scrap metal and produce steel. It operates by generating an electric arc between electrodes and the metal charge, reaching extremely high temperatures (up to 3275°F or 1800°C) to melt the material efficiently. EAFs are widely used in mini-mills for steel production, offering advantages such as reduced transportation costs and energy efficiency. They are also employed in laboratory settings for research on refractory metals and metal carbides. The primary purpose of an arc furnace is to melt and refine metals, particularly steel, using electrical energy, making it a critical tool in modern metallurgy and manufacturing.
Key Points Explained:
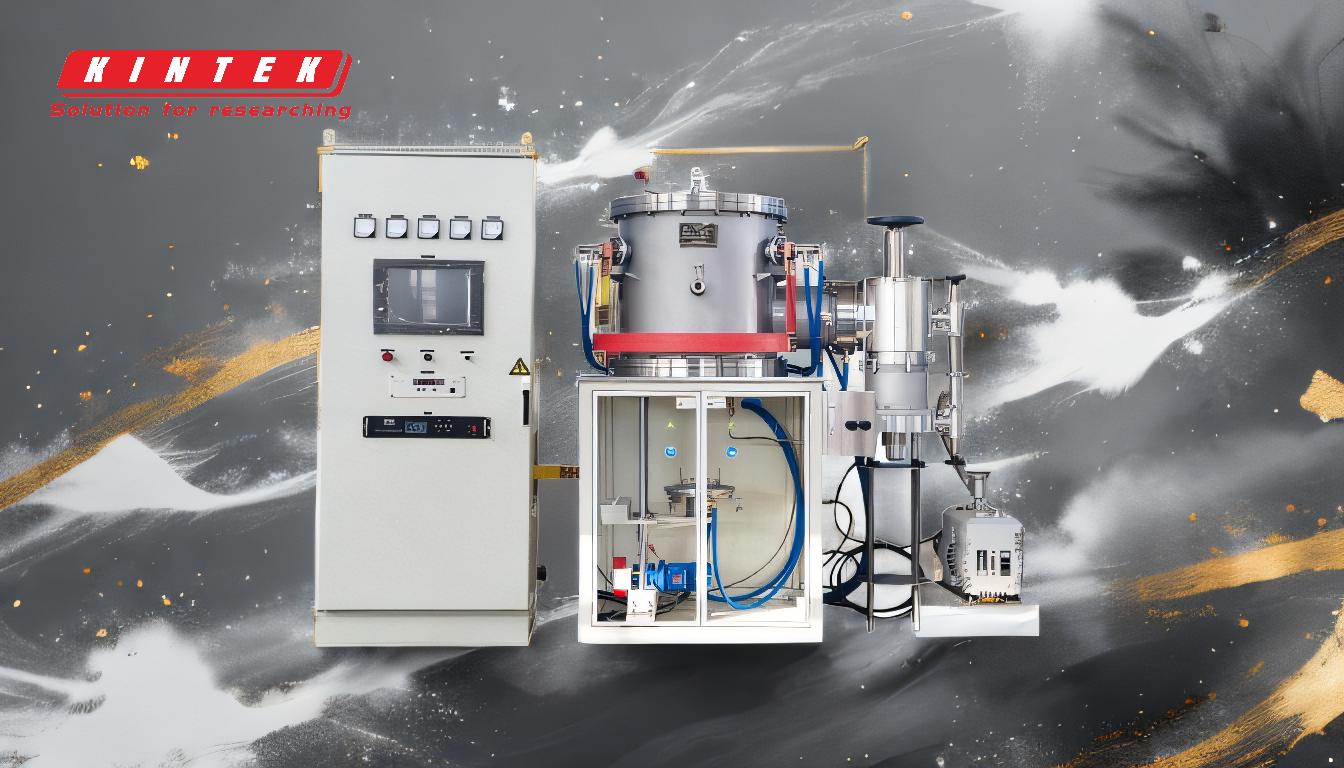
-
Primary Purpose: Melting and Refining Metals
- The core function of an electric arc furnace is to melt metals, particularly steel scrap, using electrical energy. The high-temperature arc (up to 3275°F or 1800°C) generated between the electrodes and the metal charge ensures rapid and efficient melting.
- This process is essential for recycling scrap metal into new steel products, making EAFs a key component of sustainable steel production.
-
Use in Steel Production
- EAFs are a primary source of steel in mini-mills, which produce steel products like bars and strips. These mills are often located near markets, reducing transportation costs and improving efficiency.
- The ability to use scrap metal as the main raw material makes EAFs environmentally friendly and cost-effective compared to traditional blast furnaces.
-
Energy Efficiency and Environmental Benefits
- EAFs rely on electrical energy, which can be sourced from renewable energy, reducing the carbon footprint of steel production.
- The process minimizes waste by recycling scrap metal, contributing to a circular economy in the steel industry.
-
High-Temperature Capabilities
- The electric arc generates extremely high temperatures, enabling the melting of even the most refractory metals. This makes EAFs suitable for producing high-quality steel and other alloys.
- The precise temperature control in EAFs ensures consistent product quality and reduces energy waste.
-
Applications Beyond Steelmaking
- In addition to steel production, EAFs are used in laboratory research for studying refractory metals and metal carbides. The vacuum non-self-consuming arc furnace, for example, is a specialized type used in advanced material research.
- The versatility of EAFs makes them valuable in both industrial and scientific contexts.
-
Operational Mechanism
- EAFs operate on three-phase electric current, with an arc formed between graphitized electrodes and the metal charge. The arc's heat melts the metal, and oxygen may be added to refine the molten material.
- The arc is a self-sustaining discharge phenomenon, ensuring stable and continuous operation.
-
Advantages Over Traditional Methods
- Compared to integrated mills, mini-mills using EAFs are more flexible and cost-effective, as they can be located closer to raw material sources and markets.
- The ability to use scrap metal reduces reliance on virgin materials, lowering production costs and environmental impact.
By understanding these key points, equipment and consumable purchasers can appreciate the critical role of electric arc furnaces in modern metallurgy and make informed decisions about their use in various applications.
Summary Table:
Key Aspect | Details |
---|---|
Primary Purpose | Melting and refining metals, especially steel scrap, using electrical energy. |
Temperature Range | Up to 3275°F (1800°C), enabling efficient melting of refractory metals. |
Applications | Steel production in mini-mills, laboratory research on refractory materials. |
Energy Efficiency | Uses electrical energy, often sourced from renewables, reducing carbon footprint. |
Environmental Benefits | Recycles scrap metal, minimizing waste and supporting a circular economy. |
Advantages | Cost-effective, flexible, and reduces reliance on virgin materials. |
Ready to enhance your steel production or research capabilities? Contact us today to learn more about electric arc furnaces!