A rotary kiln is a versatile, high-temperature processing device used across various industries to facilitate chemical reactions, physical transformations, and thermal processing of materials. Its primary purpose is to heat materials to extremely high temperatures in a controlled environment, enabling processes such as calcination, sintering, drying, incineration, and thermal desorption. Rotary kilns are essential in industries like cement production, where they calcinate limestone to create raw concrete, as well as in metallurgy, waste management, and chemical manufacturing. They operate as continuous or batch processes, functioning as heat exchangers, reactors, and dryers to achieve desired material transformations.
Key Points Explained:
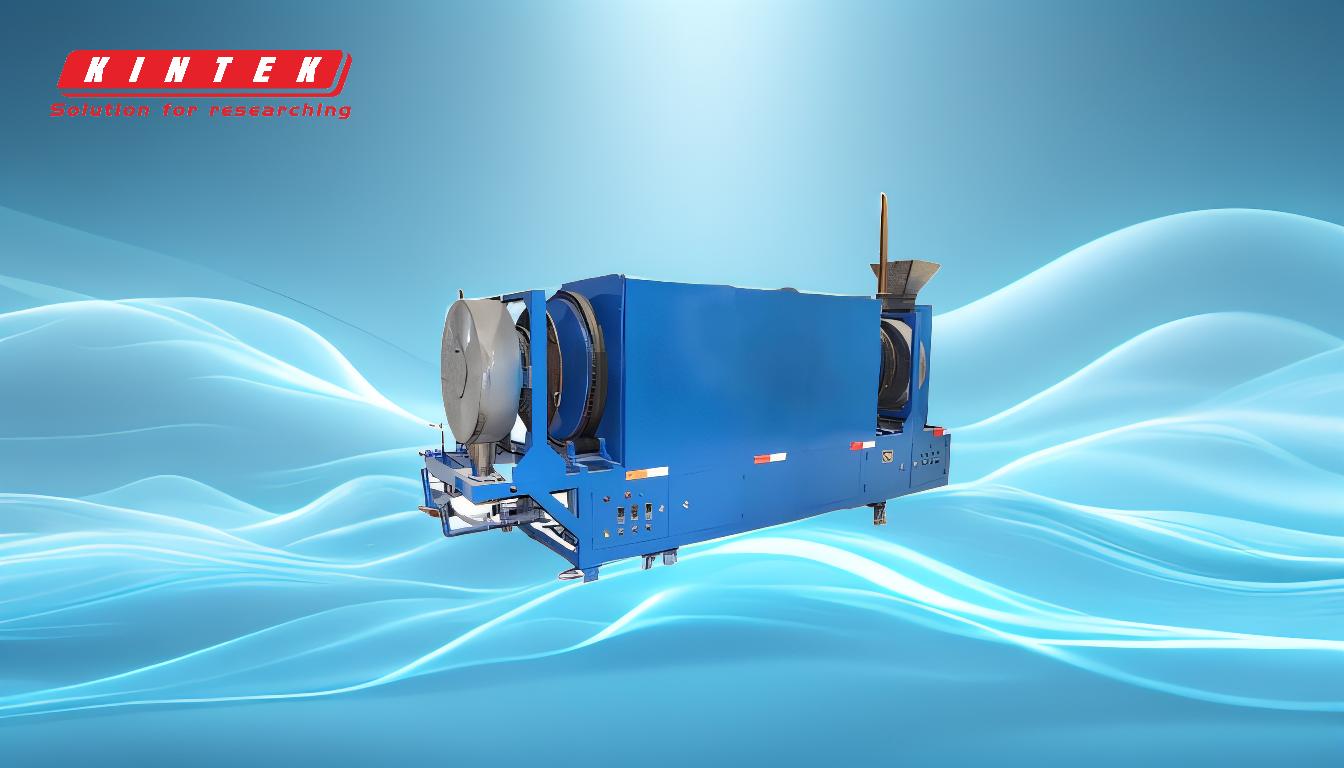
-
High-Temperature Processing:
- Rotary kilns are designed to provide ultra-high temperatures, making them ideal for thermal processing functions such as calcination, sintering, and incineration.
- They enable chemical and physical transformations of materials by exposing them to controlled heat over a specific duration.
-
Calcination:
- One of the most common applications of rotary kilns is calcination, a process where materials like limestone are heated to high temperatures to drive off carbon dioxide and produce lime.
- This is crucial in industries like cement production, where calcination is a key step in creating raw concrete.
-
Sintering and Induration:
- Rotary kilns are used to sinter or indurate materials, which involves heating them to just below their melting point to form a solid mass.
- This process is vital in metallurgy and ceramics for creating durable, high-strength materials.
-
Drying and Thermal Desorption:
- Rotary kilns effectively dry materials by removing moisture through high-temperature exposure.
- They are also used for thermal desorption, a process that removes volatile contaminants from solid materials like soil or sludge.
-
Incineration and Organic Combustion:
- Rotary kilns are employed in waste management to incinerate organic and hazardous waste, reducing it to ash and non-toxic byproducts.
- This process ensures safe disposal and minimizes environmental impact.
-
Reduction Roasting:
- In metallurgical applications, rotary kilns facilitate reduction roasting, where metal ores are heated in the presence of a reducing agent to extract metals.
- This is essential in the production of metals like iron, zinc, and lead.
-
Heat Exchange and Continuous Processing:
- Rotary kilns function as heat exchangers, transferring energy from a hot gas phase to the material being processed.
- Their inclined, rotating design allows for continuous processing, ensuring consistent material transformation and efficient heat utilization.
-
Versatility Across Industries:
- Rotary kilns are used in a wide range of industries, including cement, metallurgy, chemicals, and waste management.
- Their ability to handle diverse materials and processes makes them indispensable in industrial applications.
-
Chemical Reactions and Phase Changes:
- Rotary kilns serve as reactors to induce chemical reactions or phase changes in materials.
- This includes processes like oxidation, reduction, and decomposition, which are critical in manufacturing and material processing.
-
Design and Operation:
- The design of a rotary kiln includes a rotating cylindrical reactor, often inclined to facilitate material movement.
- This design ensures uniform heating and efficient processing of materials, making it a reliable and effective thermal processing solution.
In summary, rotary kilns are essential equipment for high-temperature industrial processes, enabling a wide range of thermal and chemical transformations. Their versatility, efficiency, and ability to handle continuous processing make them invaluable in industries requiring precise and controlled thermal treatment of materials.
Summary Table:
Key Application | Description |
---|---|
Calcination | Heats materials like limestone to produce lime, crucial for cement production. |
Sintering/Induration | Forms durable, high-strength materials by heating below melting point. |
Drying | Removes moisture from materials using high-temperature exposure. |
Thermal Desorption | Eliminates volatile contaminants from solid materials like soil or sludge. |
Incineration | Safely disposes of organic and hazardous waste, reducing it to non-toxic ash. |
Reduction Roasting | Extracts metals from ores by heating with a reducing agent. |
Heat Exchange | Transfers energy from hot gas to materials for efficient thermal processing. |
Learn how a rotary kiln can optimize your industrial processes—contact our experts today!