Thin film deposition is a versatile and essential process used across various industries to enhance the properties of materials and enable advanced technological applications. It involves applying a thin layer of material, typically less than 1000 nanometers thick, onto a substrate to alter its surface properties. This process is fundamental in the fabrication of semiconductor devices, optical coatings, solar panels, LED displays, and nanotechnology-based systems. By controlling the thickness and composition of the deposited material, thin film deposition improves properties such as conductivity, insulation, corrosion resistance, and optical performance. Its applications span industries like electronics, energy, healthcare, and manufacturing, making it a cornerstone of modern technological advancements.
Key Points Explained:
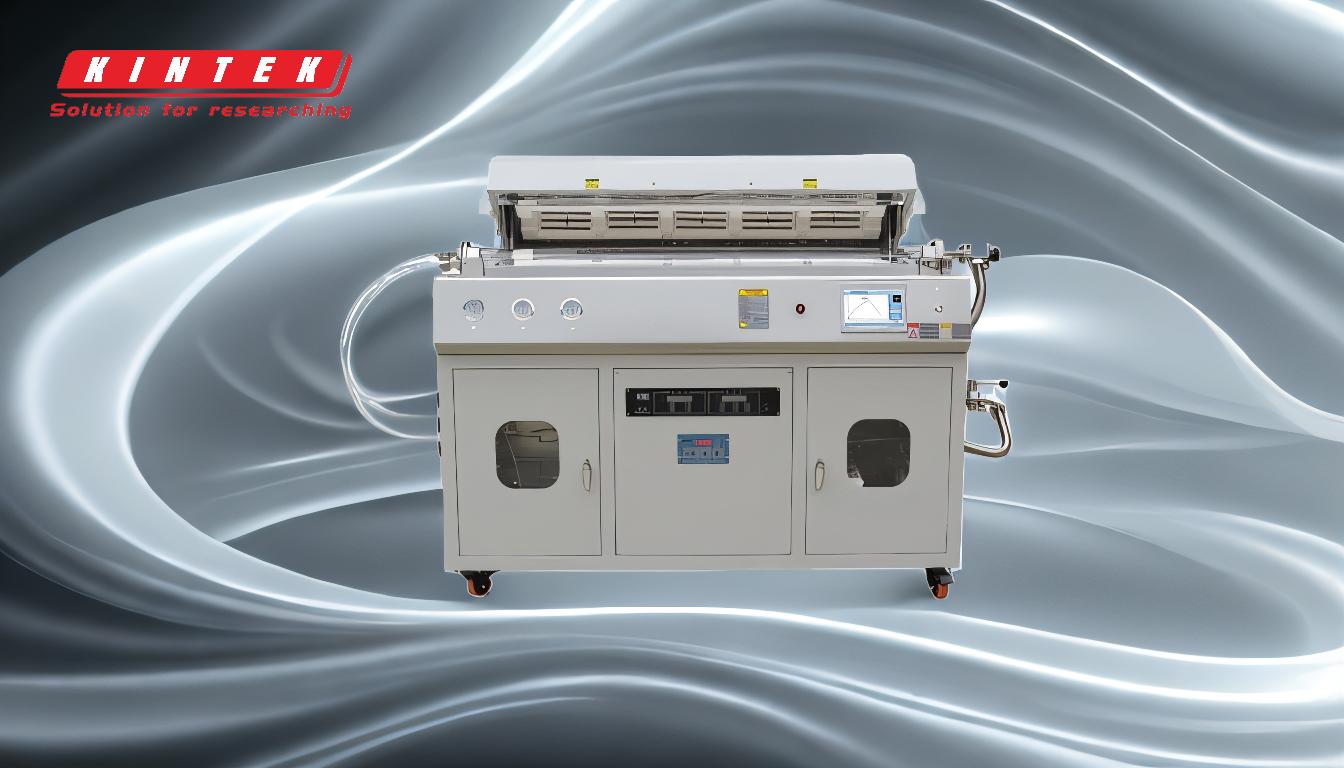
-
Definition and Process of Thin Film Deposition:
- Thin film deposition is the process of applying a thin layer of material (less than 1000 nanometers thick) onto a substrate.
- The process involves emitting particles from a source, transporting them to the substrate, and condensing them onto its surface.
- This technique is used to modify or enhance the substrate's properties, such as conductivity, insulation, or optical performance.
-
Applications in Semiconductor and Electronics Industry:
- Thin film deposition is critical for manufacturing semiconductor devices and integrated circuits.
- It enables the creation of ultra-small structures required for advanced micro/nano devices, including sensors, integrated circuitry, and quantum computers.
- The process is used to deposit materials that improve conductance, insulation, or other electrical properties, ensuring the functionality of modern electronics.
-
Optical Coatings and Devices:
- Thin film deposition is widely used to create optical coatings on lenses, plate glass, and other optical devices.
- These coatings improve properties like light transmission, refraction, and reflection, enhancing the performance of optical systems.
- Applications include anti-reflective coatings, mirrors, and filters used in cameras, telescopes, and other optical instruments.
-
Energy and Renewable Technologies:
- Thin film deposition plays a key role in the production of solar panels and energy-efficient devices.
- It is used to deposit light-absorbing or light-emitting materials, optimizing the efficiency of solar cells and LED displays.
- The process also contributes to the development of advanced batteries and energy storage systems.
-
Protective and Functional Coatings:
- Thin film deposition provides protective coatings that enhance durability and resistance to environmental factors.
- Examples include anti-corrosive ceramic thin films for sensors and industrial equipment, as well as coatings that protect against extreme temperatures, scratches, or infrared radiation.
- These coatings are essential for extending the lifespan and performance of materials in harsh environments.
-
Nanotechnology and Advanced Manufacturing:
- Thin film deposition is a foundational process in nanotechnology, enabling the creation of ultra-small structures and devices.
- It is used in the development of drug delivery systems, quantum computers, and other cutting-edge technologies.
- The ability to precisely control the thickness and composition of deposited materials makes it indispensable for advanced manufacturing.
-
Cross-Industry Relevance:
- Thin film deposition is not limited to a single industry; its applications span electronics, energy, healthcare, manufacturing, and more.
- Its versatility and ability to enhance material properties make it a critical process for modern technological advancements.
- The process is continuously evolving, paving the way for innovations in various fields.
By understanding the purpose and applications of thin film deposition, it becomes clear why this process is integral to the development of modern technology. Its ability to enhance material properties and enable the creation of advanced devices ensures its continued relevance across industries.
Summary Table:
Key Aspect | Details |
---|---|
Definition | Applying a thin layer (<1000 nm) onto a substrate to alter surface properties. |
Applications | Semiconductors, optical coatings, solar panels, LED displays, nanotechnology. |
Benefits | Improves conductivity, insulation, corrosion resistance, and optical performance. |
Industries | Electronics, energy, healthcare, manufacturing, and more. |
Future Potential | Enables innovations in quantum computing, advanced batteries, and drug delivery systems. |
Learn how thin film deposition can revolutionize your industry—contact us today for expert guidance!