The relationship between sintering temperature and melting temperature is defined by the fact that sintering occurs at temperatures significantly below the melting point of the material, while melting requires reaching or exceeding the material's melting point. Sintering relies on a combination of heat and pressure to fuse particles together without liquefying the material, making it a more energy-efficient process suitable for materials with high melting points. In contrast, melting is solely dependent on temperature, requiring the material to transition from a solid to a liquid state. This distinction makes sintering particularly useful for creating solid structures from powdered materials without the need for complete liquefaction.
Key Points Explained:
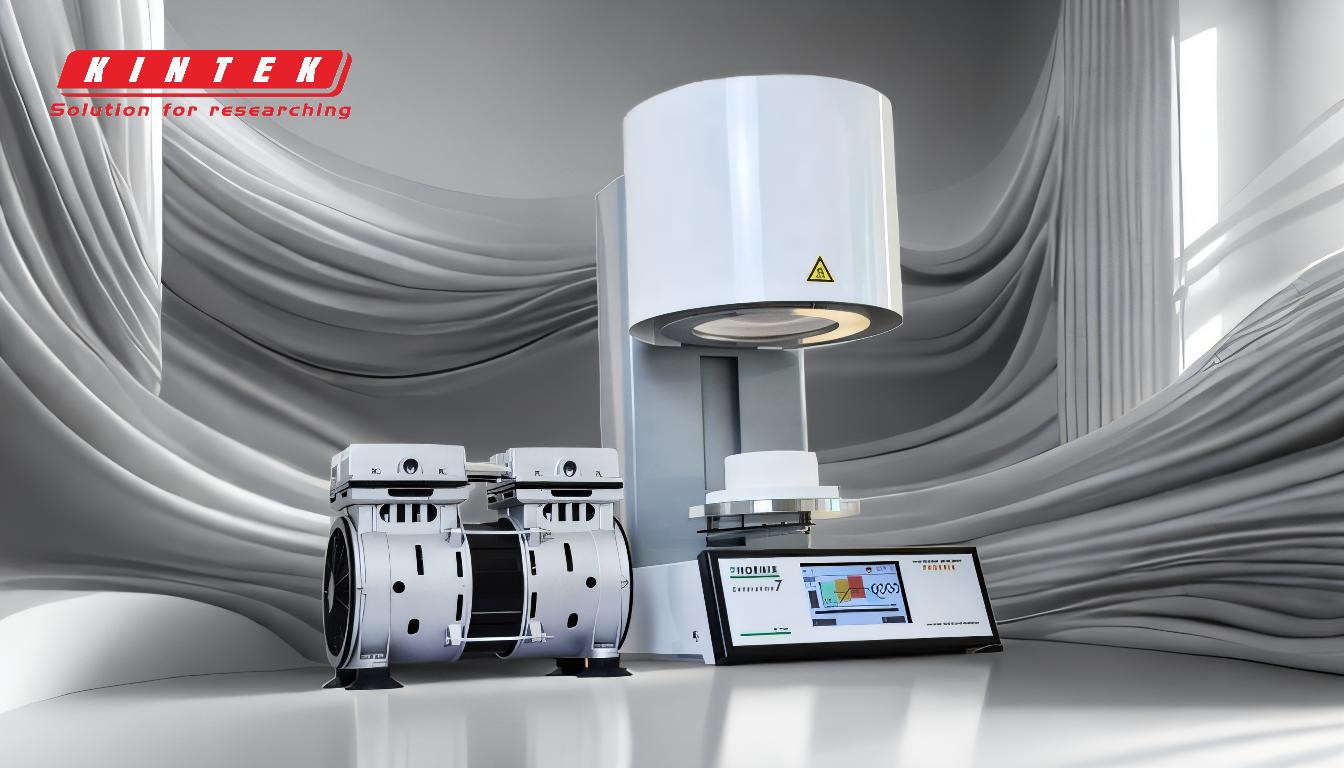
-
Definition of Sintering and Melting:
- Sintering: A process that uses heat and pressure to bond particles together without reaching the material's melting point. It is commonly used in powder metallurgy and ceramics to create solid structures.
- Melting: A process that involves heating a material to or above its melting point, causing it to transition from a solid to a liquid state.
-
Temperature Requirements:
- Sintering Temperature: Typically much lower than the melting point of the material. For example, if a metal has a melting point of 1500°C, sintering might occur at 1000°C or lower.
- Melting Temperature: Must reach or exceed the material's melting point. Using the same example, melting would require temperatures of 1500°C or higher.
-
Role of Pressure:
- Sintering: Pressure is a critical factor, as it helps bond particles together at lower temperatures. This makes sintering possible even for materials with high melting points.
- Melting: Pressure is not a factor in the melting process, as it relies solely on temperature to achieve the phase transition.
-
Energy Efficiency:
- Sintering: More energy-efficient because it operates at lower temperatures and avoids the energy-intensive process of liquefaction.
- Melting: Less energy-efficient due to the high temperatures required to achieve and maintain the liquid state.
-
Applications:
- Sintering: Ideal for creating complex shapes and structures from powdered materials, especially those with high melting points. Commonly used in manufacturing components like bearings, gears, and filters.
- Melting: Used in processes like casting, where the material must be in a liquid state to be poured into molds.
-
Material Suitability:
- Sintering: Suitable for materials that are difficult to melt or have high melting points, such as tungsten or ceramics.
- Melting: Suitable for materials that can be easily liquefied and cast, such as aluminum or copper.
-
Structural Integrity:
- Sintering: Produces porous structures with good mechanical properties, but may require additional steps like infiltration or hot isostatic pressing to achieve full density.
- Melting: Produces fully dense materials with uniform properties, but may introduce defects like shrinkage or porosity during solidification.
By understanding these key points, it becomes clear that sintering and melting are distinct processes with different temperature requirements and applications. Sintering is particularly advantageous for materials with high melting points and for creating complex, energy-efficient structures.
Summary Table:
Aspect | Sintering | Melting |
---|---|---|
Temperature | Occurs below the melting point (e.g., 1000°C for a 1500°C melting point metal) | Requires reaching or exceeding the melting point (e.g., 1500°C or higher) |
Pressure Role | Critical for bonding particles at lower temperatures | Not a factor; relies solely on temperature |
Energy Efficiency | More energy-efficient due to lower temperatures | Less energy-efficient due to high temperatures |
Applications | Ideal for creating complex shapes from powdered materials (e.g., bearings) | Used in processes like casting for liquid-state materials |
Material Suitability | Suitable for high-melting-point materials (e.g., tungsten, ceramics) | Suitable for easily liquefied materials (e.g., aluminum, copper) |
Structural Integrity | Produces porous structures; may require additional steps for full density | Produces fully dense materials but may have defects like shrinkage |
Discover how sintering can optimize your material processing—contact our experts today for tailored solutions!