The residence time of pyrolysis refers to the duration that the feedstock remains in the pyrolysis reactor, and it significantly influences the process outcomes, including the yield and quality of products such as bio-oil, char, and gases. Residence time varies depending on the type of pyrolysis: slow pyrolysis involves long residence times (minutes to days), favoring char and tar production, while fast and flash pyrolysis have very short residence times (0.5–10 seconds), optimizing bio-oil yields. The residence time of vapors is also critical, as longer durations can lead to secondary cracking, reducing bio-oil quality. Understanding these dynamics is essential for optimizing pyrolysis processes for specific product goals.
Key Points Explained:
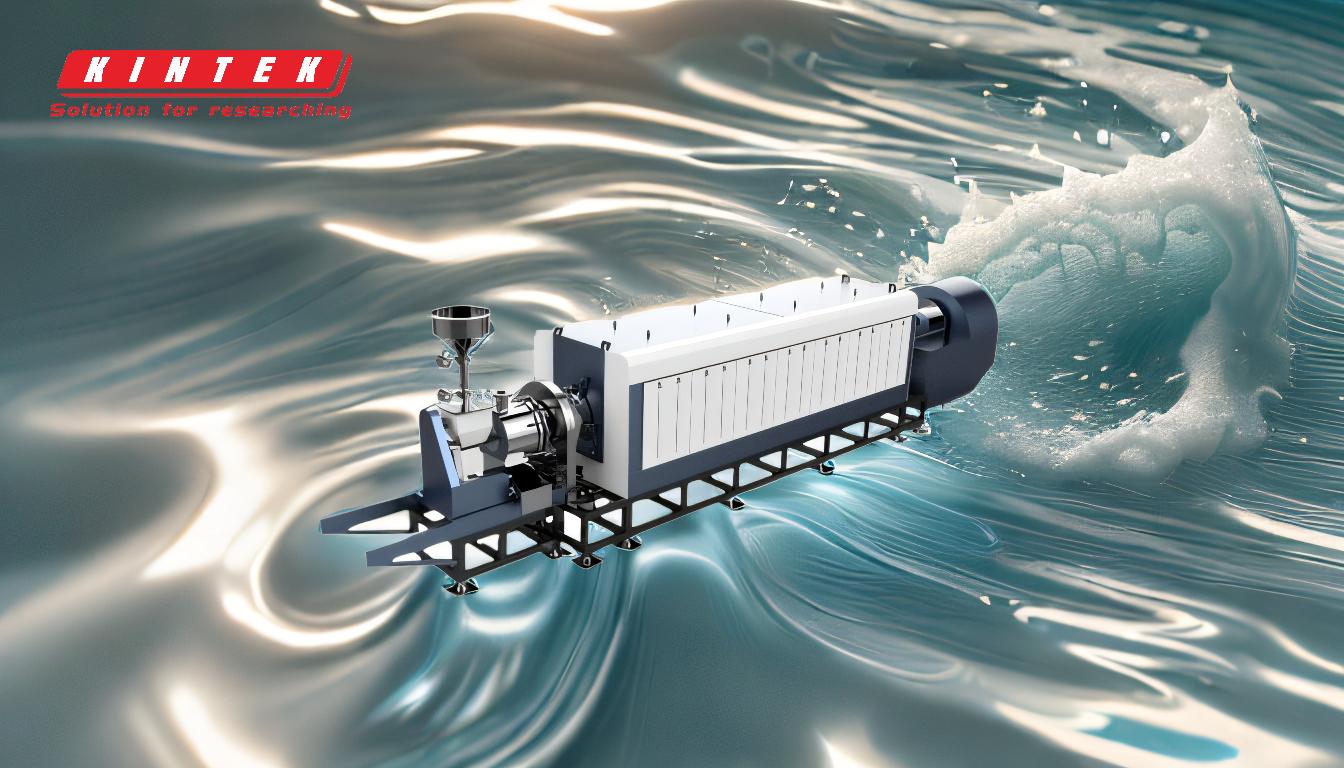
-
Definition of Residence Time
- Residence time in pyrolysis refers to the duration the feedstock or its vapors spend in the pyrolysis reactor.
- It is a critical parameter that influences the degree of thermal decomposition and the composition of the final products.
-
Residence Time in Slow Pyrolysis
- Slow pyrolysis involves long residence times, ranging from minutes to days.
- This extended duration allows for thorough thermal decomposition, favoring the production of solid char and tar.
- Gas residence times can exceed five seconds, contributing to secondary reactions that further modify product composition.
- Slow heating rates (0.1–2°C/s) and low temperatures (up to 500°C) are typical in this process.
-
Residence Time in Fast Pyrolysis
- Fast pyrolysis is characterized by very short residence times, typically between 0.5 and 10 seconds.
- High heating rates (10–200°C/s) and moderate temperatures (400–600°C) are used to maximize bio-oil yields (50–70 wt%).
- The short residence time minimizes secondary cracking of vapors, preserving the quality and yield of bio-oil.
-
Residence Time in Flash Pyrolysis
- Flash pyrolysis operates at even higher heating rates than fast pyrolysis, with residence times often less than 2 seconds.
- This ultra-short duration maximizes bio-oil yields, which can reach 75–80 wt%.
- The process is designed to rapidly decompose biomass and condense vapors before secondary reactions occur.
-
Impact of Vapor Residence Time
- Vapor residence time is a key factor in determining the quality of bio-oil.
- Longer vapor residence times (over 2 seconds) can lead to secondary cracking, where primary pyrolysis vapors break down further into smaller molecules, reducing bio-oil yield and quality.
- Optimal vapor residence times are critical for maintaining high bio-oil yields and minimizing unwanted by-products.
-
Factors Influencing Residence Time
- Temperature: Higher temperatures can reduce the required residence time by accelerating thermal decomposition.
- Heating Rate: Faster heating rates (as in fast and flash pyrolysis) allow for shorter residence times.
- Feedstock Properties: Smaller particle sizes and higher surface areas can reduce residence time by enabling quicker heat transfer and decomposition.
- Reactor Design: The type of reactor (e.g., fluidized bed, fixed bed) and its operating conditions can influence residence time.
-
Practical Implications for Equipment and Consumable Purchasers
- For Slow Pyrolysis: Equipment must accommodate long residence times, requiring robust reactors capable of sustained operation over extended periods.
- For Fast and Flash Pyrolysis: Reactors must be designed for rapid heating and cooling cycles, with precise control over residence times to optimize bio-oil production.
- Vapor Management: Systems for condensing and collecting vapors must be efficient to prevent secondary cracking and ensure high-quality bio-oil.
By understanding the role of residence time in pyrolysis, purchasers can select equipment and consumables that align with their desired product outcomes, whether focusing on char, bio-oil, or gas production.
Summary Table:
Pyrolysis Type | Residence Time | Key Features | Primary Products |
---|---|---|---|
Slow Pyrolysis | Minutes to days | Long residence time, slow heating rates (0.1–2°C/s), low temperatures (up to 500°C) | Char, tar |
Fast Pyrolysis | 0.5–10 seconds | Short residence time, high heating rates (10–200°C/s), moderate temperatures (400–600°C) | Bio-oil (50–70 wt%) |
Flash Pyrolysis | < 2 seconds | Ultra-short residence time, very high heating rates, rapid vapor condensation | Bio-oil (75–80 wt%) |
Ready to optimize your pyrolysis process? Contact our experts today for tailored solutions!