The frequency of an induction furnace plays a critical role in determining its performance, efficiency, and suitability for specific applications. It influences the power delivery, heat generation depth (skin depth), and the level of turbulence in the molten metal. Higher frequencies allow for greater power application in smaller furnaces and result in shallower heat penetration, making them ideal for smaller volumes or specific materials. Lower frequencies, on the other hand, provide deeper penetration and can induce stirring or turbulence, which is beneficial for larger volumes or certain melting processes. The choice of frequency is tailored to the material being melted, the furnace's capacity, and the desired melting speed.
Key Points Explained:
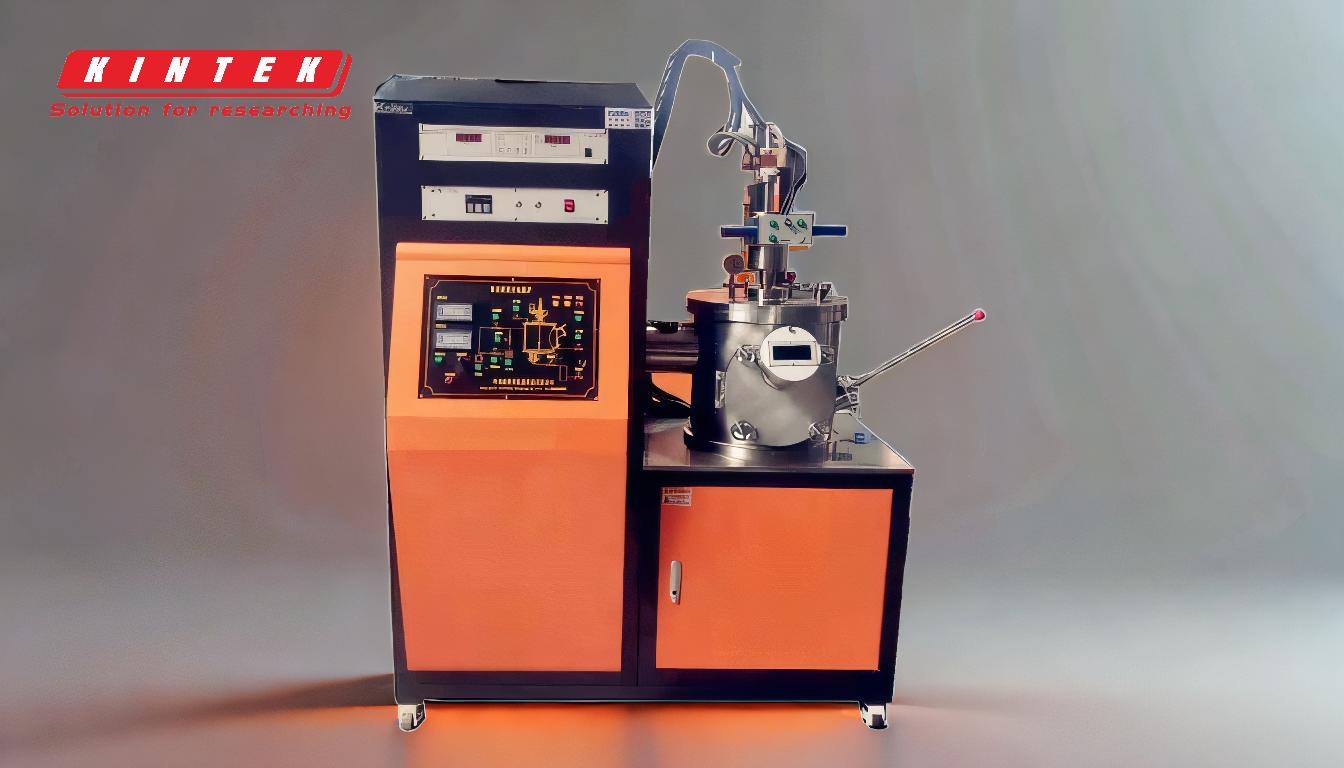
-
Power Delivery and Capacity:
- Higher operating frequencies enable greater power application to a furnace of a given capacity. This is particularly useful for smaller furnaces or when high melting speeds are required.
- Lower frequencies are more suitable for larger furnaces, as they distribute power more evenly and can handle larger volumes of material.
-
Skin Depth and Heat Generation:
- Frequency directly affects the skin depth, which is the depth to which the alternating current (AC) penetrates the material being heated.
- Higher frequencies result in shallower penetration, concentrating heat near the surface. This is ideal for smaller volumes or materials requiring precise surface heating.
- Lower frequencies provide deeper penetration, making them suitable for larger volumes or materials that require uniform heating throughout.
-
Turbulence and Stirring:
- Lower frequencies can induce turbulence or stirring in the molten metal, which is beneficial for homogenizing the melt and ensuring uniform temperature distribution.
- Higher frequencies reduce turbulence, which can be advantageous when minimal agitation is desired, such as in processes requiring precise control over the melt.
-
Material and Application Considerations:
- The choice of frequency depends on the material being melted. For example, materials with high electrical conductivity may require higher frequencies for efficient heating.
- The furnace's capacity and the required melting speed also influence frequency selection. Smaller furnaces typically operate at higher frequencies, while larger furnaces use lower frequencies.
-
Frequency Range:
- Induction furnaces operate across a wide frequency range, from utility frequencies (50 or 60 Hz) to high frequencies (400 kHz or higher).
- The specific frequency is selected based on the interplay of factors such as material properties, furnace size, and desired melting characteristics.
-
Magnetic Field Dynamics:
- The frequency of the AC current determines how quickly the magnetic field changes direction. Higher frequencies result in faster changes, which can enhance heating efficiency in certain applications.
- The induced current in the workpiece matches the frequency of the coil's current, directly influencing the heat generation pattern.
In summary, the frequency of an induction furnace is a critical parameter that affects its performance, efficiency, and suitability for specific applications. By carefully selecting the appropriate frequency, operators can optimize power delivery, heat generation, and melt characteristics to meet their specific requirements.
Summary Table:
Aspect | High Frequency | Low Frequency |
---|---|---|
Power Delivery | Greater power in smaller furnaces | Even power distribution in larger furnaces |
Skin Depth | Shallow heat penetration | Deep heat penetration |
Turbulence | Minimal agitation | Induces stirring and turbulence |
Best For | Small volumes, precise surface heating | Large volumes, uniform heating |
Frequency Range | 400 kHz or higher | 50-60 Hz |
Need help selecting the right induction furnace frequency? Contact our experts today to optimize your melting process!