Sintering is a manufacturing process that involves compacting and heating powdered materials to form a solid, low-porosity structure without melting the material entirely. This method is widely used in the production of ceramics, metals, and glass. The process typically includes steps such as powder preparation, compaction, heating to bond particles, and cooling to solidify the material. Sintering is valued for its ability to produce complex shapes with high strength and durability, making it essential in industries like automotive, aerospace, and electronics.
Key Points Explained:
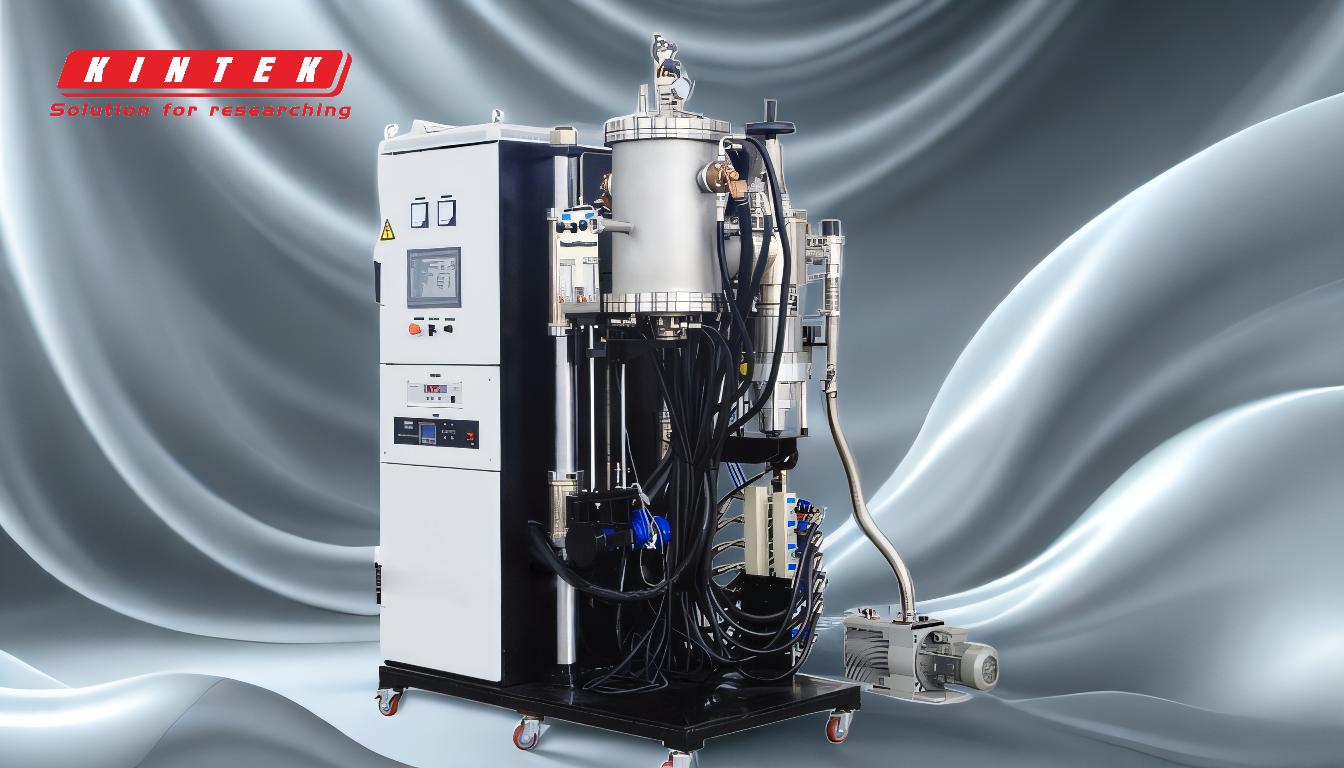
-
Powder Preparation:
- The process begins with the preparation of raw materials in powdered form. These powders can be metals, ceramics, or a mixture of both, often combined with additives like coupling agents or binders to improve bonding.
- Example: In metal sintering, powdered iron from iron ore is mixed with coke, while in ceramics, specific powders like alumina or zirconia are used.
-
Compaction:
- The powdered material is compacted into a desired shape using high pressure. This step ensures the particles are densely packed, forming a "green body" that holds its shape.
- Tools like molds, dies, or pressing equipment are used to achieve the required form. For example, in ceramic manufacturing, a calibrated powder is pressed to form a coherent shape.
-
Heating (Sintering):
- The compacted material is heated in a controlled environment, typically in a sintering furnace, to a temperature just below its melting point. This step removes volatile components, such as binders or lubricants, and allows the particles to bond through diffusion.
- During heating, the material undergoes physical and chemical changes, such as the formation of martensitic or crystalline structures in metals, or the reduction of oxides in ceramics.
- Example: In metal sintering, the furnace heats the material to activate particle bonding, while in ceramics, high temperatures remove volatile components and fuse the primary material.
-
Cooling and Solidification:
- After sintering, the material is cooled gradually to solidify into a unified, dense structure. This step ensures the final product has the desired mechanical properties, such as strength and durability.
- Cooling rates can be controlled to achieve specific microstructures, which influence the material's performance.
-
Post-Processing:
- Depending on the application, sintered parts may undergo additional steps like machining, assembly, or surface treatment.
- Example: In ceramic manufacturing, sintered parts are often machined with diamond tools or ultrasound to achieve precise dimensions, and then metallized and brazed for assembly.
-
Applications and Advantages:
- Sintering is used to produce a wide range of products, including automotive components, cutting tools, bearings, and electronic substrates.
- The process offers advantages such as the ability to create complex shapes, high material utilization, and cost-effectiveness for mass production.
-
Variations of Sintering:
- Liquid Phase Sintering (LPS): A small amount of liquid phase is introduced to accelerate particle bonding and densification.
- Solid-State Sintering: Particles bond without melting, relying on diffusion and grain growth.
- Example: In metal sintering, LPS can be used to bond cemented carbides, while solid-state sintering is common for ceramics.
By following these steps, sintering transforms powdered materials into strong, durable components with minimal waste, making it a cornerstone of modern manufacturing.
Summary Table:
Step | Description | Example |
---|---|---|
Powder Preparation | Raw materials are prepared in powdered form, often with additives. | Metal sintering: iron powder mixed with coke; ceramics: alumina or zirconia. |
Compaction | Powder is compacted into a shape using high pressure, forming a 'green body.' | Ceramic manufacturing: calibrated powder pressed into shape. |
Heating (Sintering) | Material is heated below melting point to bond particles through diffusion. | Metal sintering: furnace activates bonding; ceramics: removes volatiles. |
Cooling | Gradual cooling solidifies the material into a dense, unified structure. | Controlled cooling rates achieve specific microstructures. |
Post-Processing | Additional steps like machining or surface treatment for final product. | Ceramics: machined with diamond tools, metallized, and brazed. |
Applications | Used in automotive, aerospace, electronics, and more. | Cutting tools, bearings, electronic substrates. |
Variations | Liquid Phase Sintering (LPS) and Solid-State Sintering. | LPS for cemented carbides; solid-state for ceramics. |
Discover how sintering can revolutionize your manufacturing process—contact our experts today!