Sintering in injection molding, particularly in Metal Injection Molding (MIM), is a critical thermal process that transforms powdered materials into dense, solid components. It involves heating the molded part below its melting point in a controlled environment, allowing the particles to bond through atomic diffusion. This process enhances the material's mechanical properties, such as hardness, toughness, and precision, while maintaining intricate shapes and geometries. Sintering is essential for achieving the desired density, reducing impurities, and ensuring the final part meets stringent performance requirements. It is a cost-effective method for producing complex parts with high repeatability and precision.
Key Points Explained:
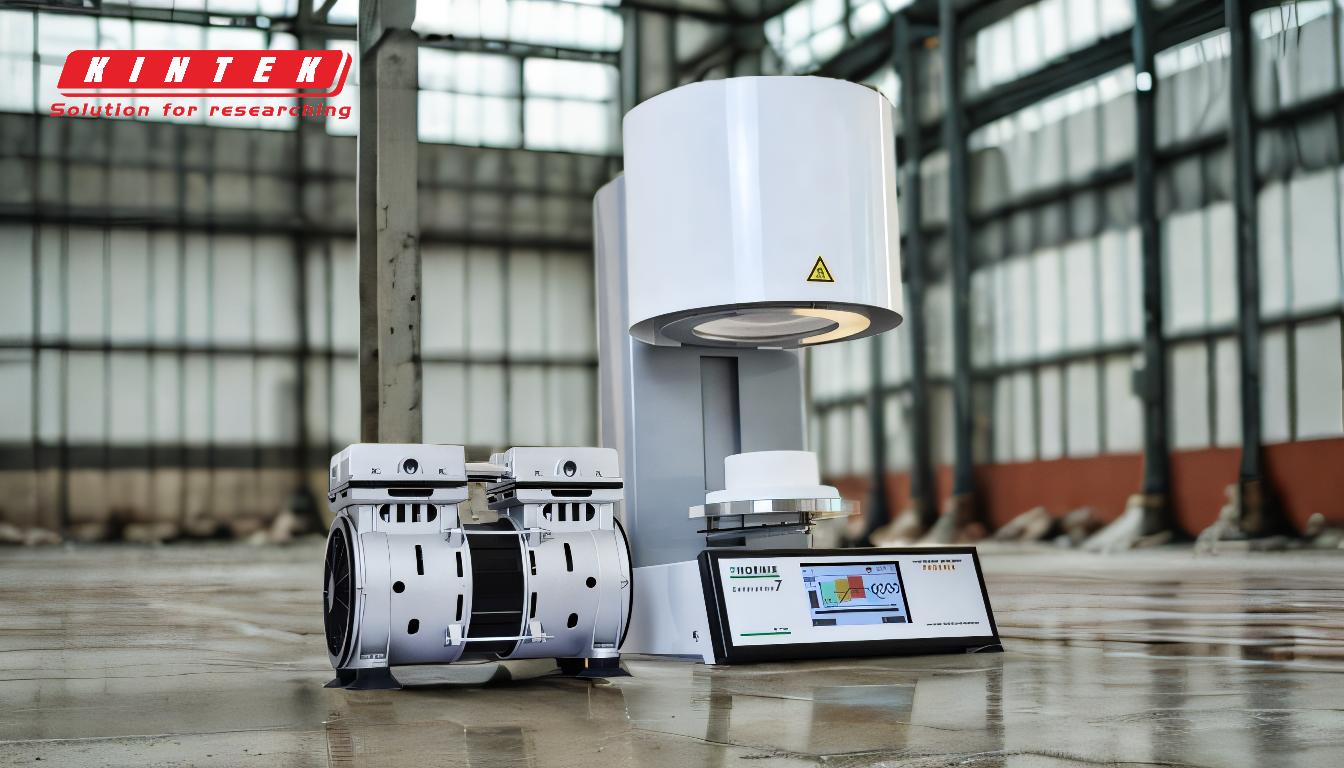
-
Definition and Purpose of Sintering:
- Sintering is a thermal process used in Metal Injection Molding (MIM) to compact and strengthen powdered materials by heating them below their melting point.
- The primary goal is to bond particles through atomic diffusion, resulting in a dense, solid component with improved mechanical properties.
-
Process Steps:
- Heating: The molded part is heated in a furnace at temperatures below the material's melting point.
- Bonding: Heat causes atomic diffusion, allowing particles to adhere and form a dense compact.
- Controlled Environment: Sintering often occurs in a high-purity hydrogen atmosphere to reduce surface oxides and impurities.
-
Key Benefits:
- Enhanced Mechanical Properties: Sintering improves hardness, toughness, and precision of the final part.
- Complex Geometries: It allows the creation of intricate shapes that are difficult to achieve with traditional manufacturing methods.
- Cost-Effectiveness: Lower tooling costs and rapid mass production are possible while maintaining precision and repeatability.
-
Applications:
- Metal Injection Molding (MIM): Sintering is crucial for producing high-performance metal parts with complex geometries.
- Ceramics and Glass: The process is also used in the manufacture of ceramics and glass, where bonding particles at high temperatures is essential.
-
Comparison with Other Manufacturing Techniques:
- Flexibility: Sintering is more flexible than casting, forging, and extrusion, as it does not require solid-liquid phase changes.
- Material Versatility: It can be used with a wide range of materials, including metals, ceramics, and composites.
-
Importance in MIM:
- Density and Mechanical Properties: Sintering is vital for achieving the desired density and mechanical properties of MIM parts.
- Impurity Reduction: The process helps reduce surface oxides and impurities, ensuring high-quality final products.
-
Challenges and Considerations:
- Temperature Control: Precise temperature control is necessary to avoid melting while ensuring proper bonding.
- Atmosphere Management: The sintering environment must be carefully controlled to prevent contamination and ensure consistent results.
By understanding these key points, an equipment or consumable purchaser can better appreciate the importance of sintering in the injection molding process and make informed decisions about materials and equipment.
Summary Table:
Aspect | Details |
---|---|
Definition | Thermal process to bond powdered materials below melting point, enhancing mechanical properties. |
Key Benefits | - Improved hardness, toughness, and precision. |
- Enables complex geometries.
- Cost-effective mass production. | | Applications | - Metal Injection Molding (MIM).
- Ceramics and glass manufacturing. | | Challenges | - Precise temperature control.
- Controlled atmosphere to prevent contamination. |
Discover how sintering can optimize your MIM process—contact us today for expert guidance!