Spark sintering, also known as spark plasma sintering (SPS), is a modern powder metallurgy technique that combines electrical and mechanical energy to rapidly form dense, high-quality parts. Unlike traditional sintering methods that rely on external heat sources, spark sintering uses a high-power electric current that passes through the compacted powder while simultaneously applying mechanical pressure. This process heats the material internally, removes surface impurities, and achieves sintering in seconds, making it highly efficient for producing complex shapes and advanced materials.
Key Points Explained:
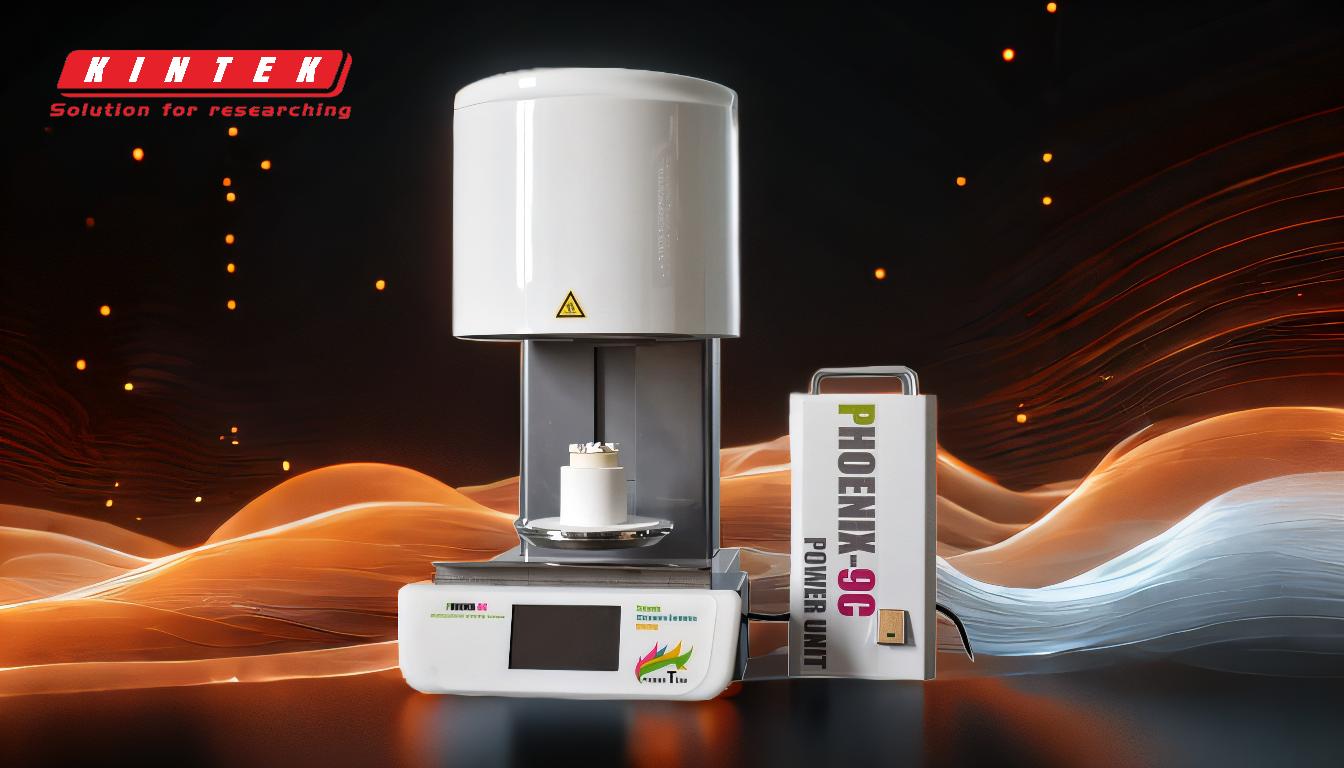
-
Definition and Mechanism of Spark Sintering:
- Spark sintering is a powder processing method that integrates electrical and mechanical energy to form parts.
- A high-power electric current is passed through the compacted powder, while mechanical pressure is applied simultaneously.
- The punches used for compression also act as electrodes, enabling the electric current to flow through the material.
- This process heats the material internally, unlike traditional methods like hot pressing, where heat is applied externally.
-
Advantages of Spark Sintering:
- Rapid Processing: The entire part is pressed and sintered in seconds, significantly reducing production time.
- Internal Heating: The electric current heats the material from within, ensuring uniform temperature distribution and minimizing thermal gradients.
- Surface Film Removal: The current burns away surface films and oxides from powder particles, enhancing particle bonding and material purity.
- High Density and Quality: The combination of electrical and mechanical energy results in dense, high-quality parts with improved mechanical properties.
-
Comparison with Other Sintering Methods:
- Hot Pressing: In hot pressing, heat is applied externally, which can lead to uneven heating and longer processing times compared to spark sintering.
- Conventional Sintering: This method involves heating the powder compact without external pressure, resulting in lower density and longer sintering times.
- Liquid Phase Sintering (LPS): LPS uses a liquid phase to accelerate densification, but it may not achieve the same level of purity and density as spark sintering.
- Microwave Sintering: While microwave sintering is faster than conventional methods, it is typically limited to specific materials like ceramics and does not offer the same level of control as spark sintering.
-
Applications of Spark Sintering:
- Advanced Materials: Spark sintering is ideal for producing advanced materials such as ceramics, composites, and nanostructured materials.
- Complex Shapes: The rapid and uniform heating allows for the production of complex shapes with high precision.
- High-Performance Components: It is widely used in industries requiring high-performance components, such as aerospace, automotive, and electronics.
-
Process Parameters and Control:
- Electric Current: The intensity and duration of the electric current are critical for achieving optimal sintering results.
- Mechanical Pressure: The applied pressure must be carefully controlled to ensure uniform densification without causing defects.
- Temperature Control: Precise temperature control is essential to prevent overheating or incomplete sintering.
-
Challenges and Limitations:
- Equipment Cost: The specialized equipment required for spark sintering can be expensive, making it less accessible for small-scale operations.
- Material Limitations: While spark sintering is versatile, it may not be suitable for all materials, particularly those with low electrical conductivity.
- Process Complexity: The need for precise control of electrical and mechanical parameters adds complexity to the process, requiring skilled operators.
-
Future Prospects:
- Material Innovation: Spark sintering is expected to play a key role in the development of new materials with enhanced properties, such as higher strength and thermal stability.
- Process Optimization: Ongoing research aims to optimize the process parameters to further reduce costs and improve efficiency.
- Industrial Adoption: As the technology matures, it is likely to see broader adoption across various industries, particularly in high-tech manufacturing.
In summary, spark sintering is a cutting-edge powder metallurgy technique that offers significant advantages in terms of speed, quality, and versatility. Its ability to combine electrical and mechanical energy for rapid, internal heating makes it a powerful tool for producing advanced materials and complex components. While there are challenges related to cost and process complexity, ongoing advancements are expected to drive its adoption and expand its applications in the future.
Summary Table:
Aspect | Details |
---|---|
Definition | Combines electrical and mechanical energy for rapid sintering. |
Key Advantages | Rapid processing, internal heating, surface film removal, high density. |
Comparison | Faster and more precise than hot pressing, conventional, and LPS methods. |
Applications | Advanced materials, complex shapes, high-performance components. |
Challenges | High equipment cost, material limitations, process complexity. |
Future Prospects | Material innovation, process optimization, broader industrial adoption. |
Unlock the potential of spark sintering for your projects—contact our experts today!