The speed of a kiln for cement production typically ranges from 0.5 to 2 revolutions per minute (rpm) for traditional rotary kilns, while modern cement plant kilns operate at higher speeds of 4 to 5 rpm. The rotation speed directly influences the material flow rate through the kiln, which is critical for maintaining operational efficiency. Factors such as the kiln's inclination angle, temperature, and retention time of solid particles also play a significant role in determining the kiln's performance. These parameters are carefully controlled to ensure optimal processing of cement materials, ensuring consistent quality and energy efficiency.
Key Points Explained:
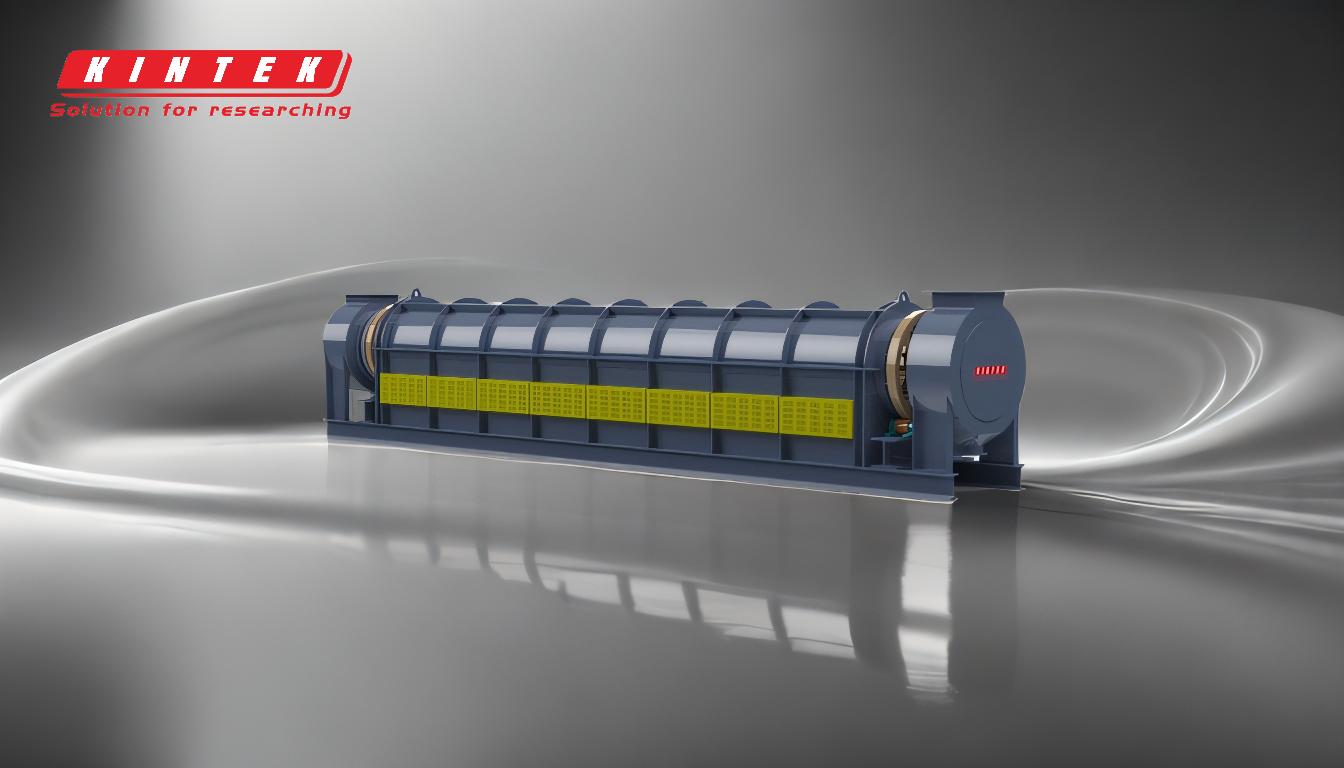
-
Typical Rotation Speed of Cement Kilns:
- Traditional rotary kilns operate at speeds between 0.5 to 2 rpm.
- Modern cement plant kilns are designed to run faster, typically at 4 to 5 rpm.
- The rotation speed is a critical factor in determining the material flow rate through the kiln.
-
Impact of Rotation Speed on Material Flow:
- The speed of material flow through the kiln is proportional to the rotation speed.
- Faster rotation speeds result in shorter retention times for materials, which can improve throughput but must be balanced with the need for sufficient processing time.
-
Operational Parameters Influencing Kiln Efficiency:
- Inclination Angle: The tilt of the kiln affects the gravitational force acting on the material, influencing its movement through the kiln.
- Temperature: High temperatures are maintained in different zones (drying, heating, reaction, and soaking) to ensure proper chemical reactions and material transformation.
- Retention Time: The time materials spend in the kiln is crucial for achieving the desired chemical and physical changes.
- Bed Depth: Controlled using a ring dam, bed depth ensures uniform heat transfer and processing of materials.
-
Modern vs. Traditional Kiln Speeds:
- Modern kilns operate at higher speeds (4 to 5 rpm) compared to traditional kilns (0.5 to 2 rpm).
- Higher speeds in modern kilns are enabled by advancements in kiln design, materials, and control systems, allowing for better energy efficiency and throughput.
-
Importance of Balancing Speed and Processing Time:
- While higher rotation speeds increase throughput, they must be carefully managed to ensure materials have sufficient time to undergo necessary chemical reactions.
- Insufficient retention time can lead to incomplete processing, affecting the quality of the final cement product.
-
Control Systems in Modern Kilns:
- Modern kilns are equipped with advanced control systems that monitor and adjust parameters such as rotation speed, temperature, and material flow in real-time.
- These systems optimize kiln performance, ensuring consistent product quality and energy efficiency.
-
Energy Efficiency Considerations:
- Higher rotation speeds can reduce energy consumption per unit of material processed, but this must be balanced with the energy required to maintain high temperatures and ensure proper material processing.
- Modern kilns are designed to minimize heat loss and maximize energy efficiency, contributing to lower operational costs.
-
Practical Implications for Cement Production:
- The choice of kiln speed depends on the specific requirements of the cement production process, including the type of raw materials used and the desired output quality.
- Operators must carefully calibrate the kiln to achieve the optimal balance between speed, retention time, and energy efficiency.
By understanding these key points, equipment and consumable purchasers can make informed decisions about the selection and operation of rotary kilns for cement production, ensuring optimal performance and cost-effectiveness.
Summary Table:
Parameter | Traditional Kilns | Modern Kilns |
---|---|---|
Rotation Speed (rpm) | 0.5 to 2 | 4 to 5 |
Material Flow Rate | Slower | Faster |
Retention Time | Longer | Shorter |
Energy Efficiency | Moderate | High |
Control Systems | Basic | Advanced |
Want to optimize your cement production process? Contact our experts today for tailored solutions!