Sputter coating in scanning electron microscopy (SEM) is a critical sample preparation technique used to deposit a thin, conductive layer of material onto non-conductive or poorly conductive specimens. This process enhances the quality of SEM imaging by improving conductivity, reducing charging effects, and increasing the signal-to-noise ratio. Typically, metals like gold, platinum, or gold/palladium are sputtered onto the sample surface in layers ranging from 2 to 20 nanometers thick. The sputtering process involves bombarding a target material with energetic ions, usually argon ions, which eject atoms from the target. These atoms then deposit onto the specimen, forming a uniform conductive coating. This technique is particularly useful for beam-sensitive or non-conductive materials, ensuring clearer and more accurate SEM images.
Key Points Explained:
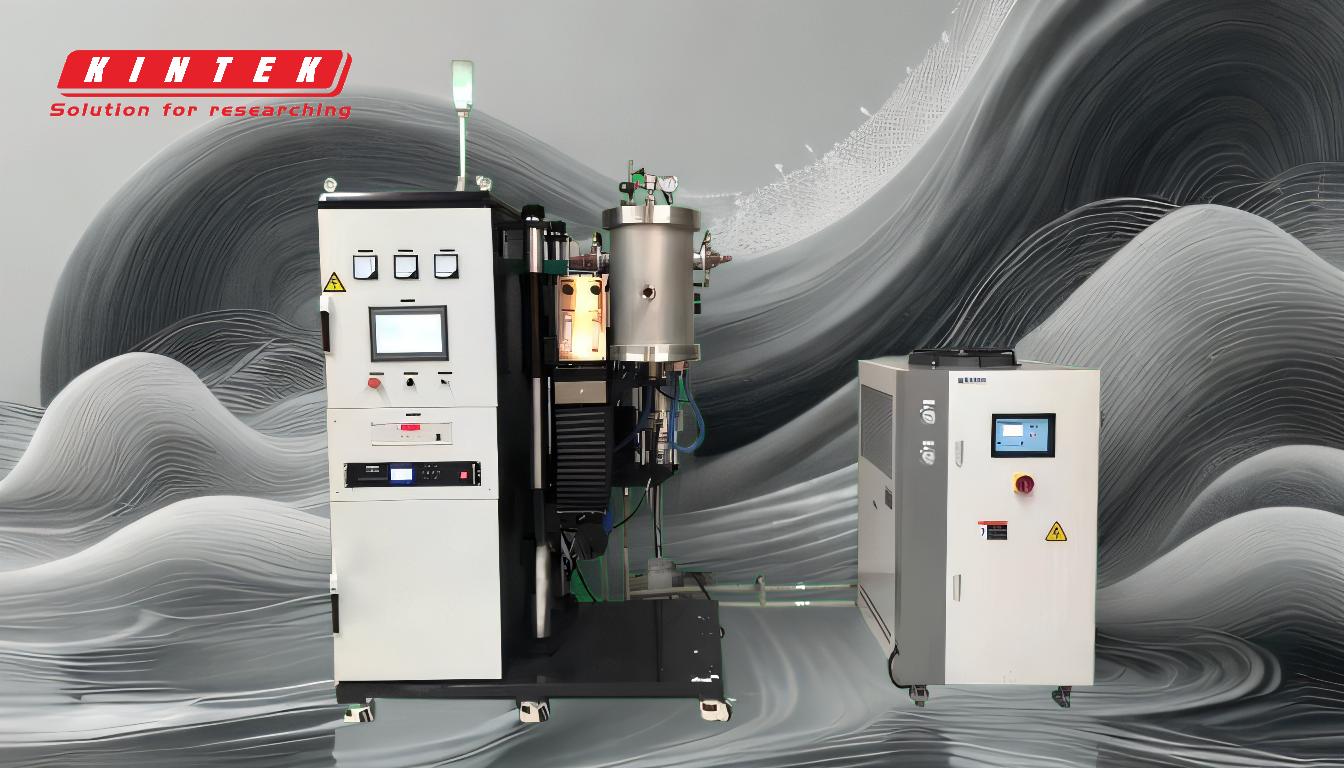
-
Purpose of Sputter Coating in SEM:
- Sputter coating is primarily used to prepare non-conductive or poorly conductive specimens for SEM analysis.
- It prevents specimen charging caused by the electron beam, which can distort images and damage the sample.
- The conductive layer improves secondary electron emission, enhancing the signal-to-noise ratio and producing clearer images.
-
Materials Used in Sputter Coating:
- Common materials include gold, platinum, gold/palladium, silver, chromium, and iridium.
- These metals are chosen for their conductivity and ability to form thin, uniform layers.
-
Thickness of Sputtered Films:
- The sputtered films are typically ultra-thin, ranging from 2 to 20 nanometers.
- This thickness is sufficient to provide conductivity without obscuring the sample's surface features.
-
Mechanism of Sputtering:
- The process involves bombarding a target material (cathode) with energetic ions, usually argon ions, in a vacuum chamber.
- The ions transfer energy to the target atoms, causing them to be ejected and deposited onto the specimen (anode).
- This creates a uniform conductive coating on the sample surface.
-
Benefits of Sputter Coating:
- Improved Conductivity: Reduces charging effects and ensures accurate imaging.
- Enhanced Image Quality: Increases secondary electron emission, improving the signal-to-noise ratio.
- Protection: Provides structural protection for beam-sensitive materials.
-
Applications in SEM:
- Sputter coating is essential for imaging non-conductive materials like polymers, biological samples, and ceramics.
- It is also used for challenging samples that are prone to charging or beam damage.
-
Technical Details of the Sputtering Process:
- A magnetron is used to generate a plasma of argon ions.
- A high negative voltage (typically -300V or more) is applied to the target, attracting positive ions.
- Collisions between ions and target atoms create primary recoil atoms, which eject surface atoms through collision cascades.
- The ejected atoms deposit onto the specimen, forming a thin, conductive layer.
By understanding these key points, a purchaser or user of SEM equipment can appreciate the importance of sputter coating in achieving high-quality imaging and protecting delicate samples. This technique is indispensable for working with non-conductive or beam-sensitive materials, ensuring accurate and reliable SEM analysis.
Summary Table:
Key Aspect | Details |
---|---|
Purpose | Prepares non-conductive samples, prevents charging, improves image clarity. |
Materials Used | Gold, platinum, gold/palladium, silver, chromium, iridium. |
Thickness | 2 to 20 nanometers. |
Mechanism | Argon ions bombard target material, ejecting atoms for uniform coating. |
Benefits | Improved conductivity, enhanced image quality, sample protection. |
Applications | Polymers, biological samples, ceramics, and beam-sensitive materials. |
Discover how sputter coating can optimize your SEM imaging—contact our experts today for more information!