The magnetron sputtering process is a widely used thin film deposition technique that involves ejecting material from a target onto a substrate using a magnetic field and a plasma environment. It begins by introducing an inert gas, typically argon, into a vacuum chamber. A high voltage is applied to create a plasma, which ionizes the argon gas. The positively charged argon ions are then attracted to the negatively charged target material, causing atoms to be ejected from the target. These ejected atoms travel through the vacuum and deposit onto the substrate, forming a thin film. The process is enhanced by magnets that create a magnetic field, trapping electrons and increasing the efficiency of ion generation. This method is highly versatile, compatible with a wide range of materials, and offers high deposition rates.
Key Points Explained:
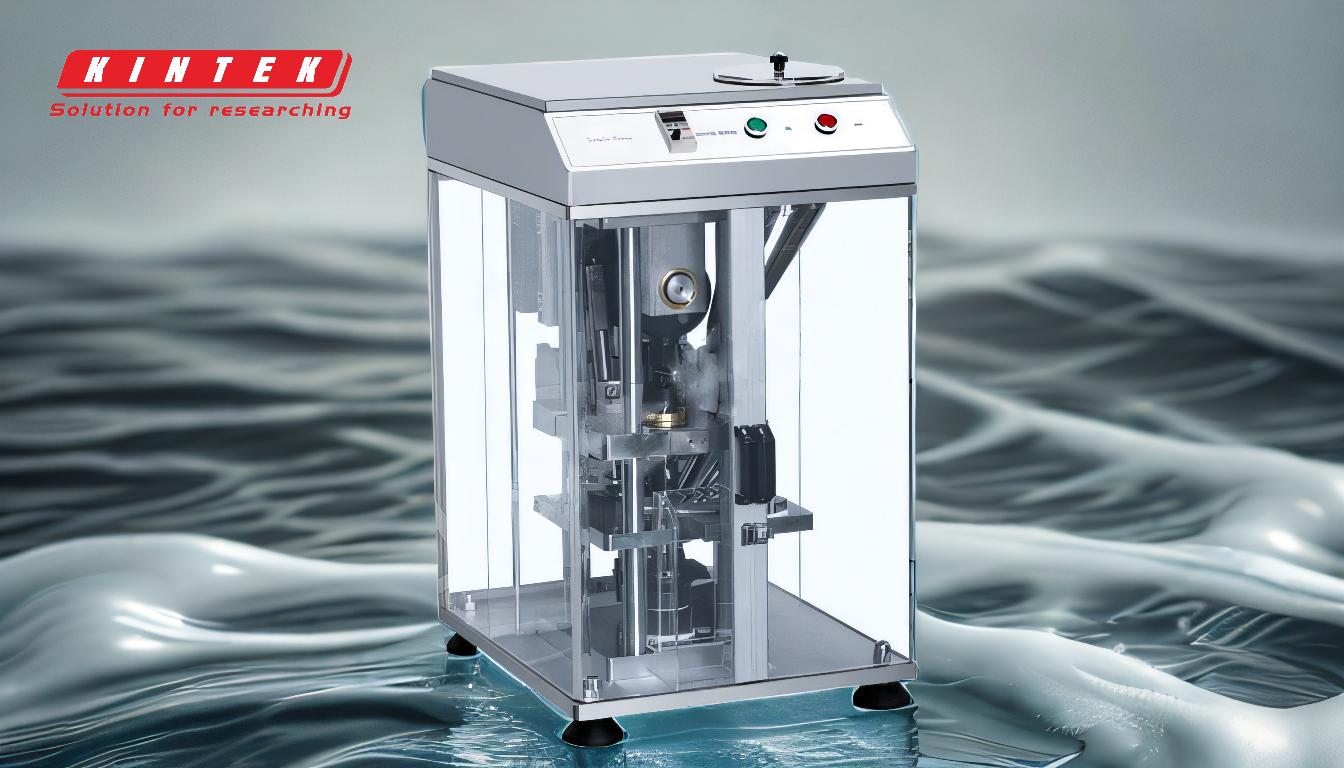
-
Introduction of Inert Gas:
- The process begins by introducing an inert gas, usually argon, into a vacuum chamber. This gas is essential for creating the plasma required for sputtering. Argon is chosen because it is chemically inert and readily ionizes under the applied voltage.
-
Creation of Plasma:
- A high voltage is applied to the system, creating a gaseous plasma near the target’s magnetic field. This plasma consists of argon gas atoms, argon ions, and free electrons. The plasma is crucial for generating the ions that will bombard the target material.
-
Ion Bombardment and Sputtering:
- The positively charged argon ions are attracted to the negatively charged target material. When these ions collide with the target, they eject atoms from the target’s surface. This process is known as sputtering. The ejected atoms are then free to travel through the vacuum chamber.
-
Magnetic Field Enhancement:
- A set of permanent magnets is placed behind the cathode/target to create a magnetic field. This magnetic field traps electrons near the target, increasing the efficiency of ion generation and enhancing the sputtering process. The magnetic field also helps in controlling the velocity and direction of the charged particles.
-
Deposition on Substrate:
- The ejected atoms from the target travel through the vacuum and deposit onto the substrate’s surface. This deposition forms a thin film on the substrate. The substrate is typically placed in a holder within the deposition chamber to ensure uniform coating.
-
Advantages of Magnetron Sputtering:
- High Deposition Rates: The magnetic field increases the density of the plasma, leading to higher deposition rates compared to other sputtering methods.
- Material Versatility: Magnetron sputtering is compatible with a wide range of materials, including metals, alloys, and compounds. It can deposit materials without requiring them to melt or evaporate.
- Maintained Composition: The process allows for the deposition of compounds and alloys while maintaining their original composition, which is crucial for applications requiring precise material properties.
-
Historical Context and Evolution:
- Sputtering was first observed in the 1850s but became commercially relevant in the 1940s with diode sputtering. However, diode sputtering had limitations such as low deposition rates and high costs. Magnetron sputtering was introduced in 1974 as an improved alternative, offering higher deposition rates and broader applications.
-
Key Components of the System:
- Substrate Holder: Holds the substrate in place during the deposition process.
- Load Lock Chamber: Allows for the introduction and removal of substrates without breaking the vacuum in the main chamber.
- Deposition Chamber: The main chamber where the sputtering process occurs.
- Sputter Gun with Target Material: The source of the material to be deposited.
- Strong Magnets: Create the magnetic field necessary for the process.
- Argon Gas Flow System: Introduces and controls the flow of argon gas into the chamber.
- High Voltage DC Power: Initiates and maintains the plasma.
By understanding these key points, one can appreciate the complexity and efficiency of the magnetron sputtering process, making it a preferred method for thin film deposition in various industrial and research applications.
Summary Table:
Key Aspect | Description |
---|---|
Inert Gas | Argon gas is introduced into a vacuum chamber to create plasma. |
Plasma Creation | High voltage ionizes argon gas, generating plasma for ion bombardment. |
Ion Bombardment | Argon ions collide with the target, ejecting atoms for deposition. |
Magnetic Field | Magnets trap electrons, enhancing ion generation and sputtering efficiency. |
Deposition | Ejected atoms deposit onto the substrate, forming a thin film. |
Advantages | High deposition rates, material versatility, and maintained composition. |
Key Components | Substrate holder, load lock chamber, sputter gun, magnets, argon flow system. |
Discover how magnetron sputtering can revolutionize your thin film deposition process—contact our experts today!