The sputtering process in magnetron deposition is a physical vapor deposition (PVD) technique used to create thin films on substrates. It involves the use of a magnetic field to enhance the ionization of an inert gas, typically argon, which is then used to bombard a target material. The bombardment ejects atoms from the target, which then deposit onto a substrate to form a thin film. The process is highly controlled, involving vacuum conditions, precise temperature settings, and the application of high voltages to create plasma. This method is widely used in industries for coating materials due to its ability to produce high-quality, uniform films.
Key Points Explained:
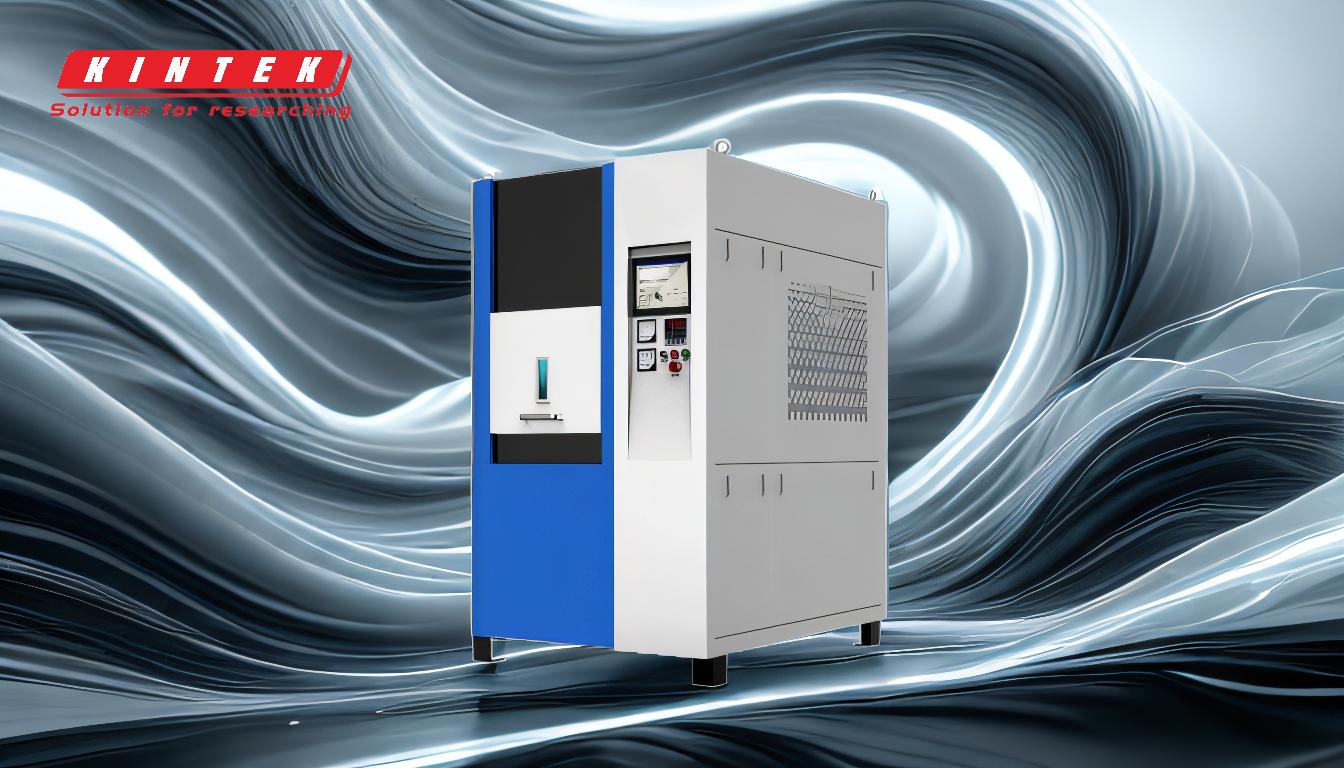
-
Introduction of Inert Gas:
- Argon Gas Flow: The process begins by introducing an inert gas, usually argon, into the vacuum chamber. This gas is chosen because it is chemically inert and does not react with the target material or the substrate.
-
Creation of Plasma:
- High Voltage Application: A high voltage is applied to create a plasma within the chamber. This plasma consists of argon ions, free electrons, and neutral argon atoms.
- Magnetic Field Influence: The magnetic field generated by the magnet arrays (magnetron) confines the electrons near the target surface, increasing the ionization rate of argon gas and enhancing the density of the plasma.
-
Ion Bombardment and Sputtering:
- Ion Acceleration: The positively charged argon ions are accelerated towards the negatively charged target due to the electric field.
- Energy Transfer: When these ions collide with the target, they transfer their kinetic energy to the target atoms. If the transferred energy exceeds the binding energy of the target atoms, they are ejected from the target surface.
-
Deposition of Sputtered Atoms:
- Atom Ejection: The ejected target atoms are neutral and travel through the vacuum chamber.
- Film Formation: These atoms eventually land on the substrate, where they condense and form a thin film. The uniformity and quality of the film are influenced by factors such as the angle of incidence, the energy of the sputtered atoms, and the substrate temperature.
-
Role of Secondary Electrons:
- Electron Emission: Secondary electrons are emitted from the target surface during ion bombardment. These electrons are trapped by the magnetic field and contribute to sustaining the plasma by ionizing more argon atoms.
-
Process Control Parameters:
- Vacuum Conditions: The chamber is maintained at a high vacuum (around 1 Pa) to minimize contamination and ensure a clean deposition environment.
- Temperature Regulation: The substrate and chamber may be heated to specific temperatures (150 – 750°C) depending on the material being deposited, to improve film adhesion and quality.
- Power Supply: A DC power supply is used to apply the necessary high voltage (3-5 kV) to the target, which is crucial for the ionization of argon and the sputtering process.
-
Advantages of Magnetron Sputtering:
- High Deposition Rates: The magnetic field increases the ionization efficiency, leading to higher sputtering rates.
- Uniform Coatings: The process allows for the deposition of uniform and dense films, which are essential for applications requiring precise thickness and high-quality finishes.
- Versatility: Magnetron sputtering can be used with a wide range of materials, including metals, alloys, and ceramics, making it a versatile technique for various industrial applications.
By understanding these key points, one can appreciate the complexity and precision involved in the magnetron sputtering process, which is essential for producing high-performance coatings in industries such as semiconductors, optics, and decorative finishes.
Summary Table:
Step | Description |
---|---|
Inert Gas Introduction | Argon gas is introduced into the vacuum chamber for ionization. |
Plasma Creation | High voltage generates plasma; magnetic field enhances ionization. |
Ion Bombardment | Argon ions bombard the target, ejecting atoms for deposition. |
Film Formation | Sputtered atoms deposit on the substrate, forming a thin film. |
Secondary Electrons | Electrons sustain plasma by ionizing more argon atoms. |
Control Parameters | Vacuum, temperature, and high voltage ensure precision and quality. |
Advantages | High deposition rates, uniform coatings, and material versatility. |
Discover how magnetron sputtering can enhance your coating processes—contact us today!