The sputtering process is a surface treatment technique used to deposit thin films of material onto a substrate. It involves creating a vacuum environment, introducing an inert gas, and using high voltage to ionize the gas. The ionized gas then bombards a target material, causing atoms to be ejected and deposited onto a substrate, forming a thin film. This process is highly precise and is used in various industries to create coatings with specific properties such as reflectivity, electrical resistivity, or ionic resistivity. The key steps include creating a vacuum, introducing an inert gas, applying high voltage to ionize the gas, and depositing the sputtered material onto the substrate.
Key Points Explained:
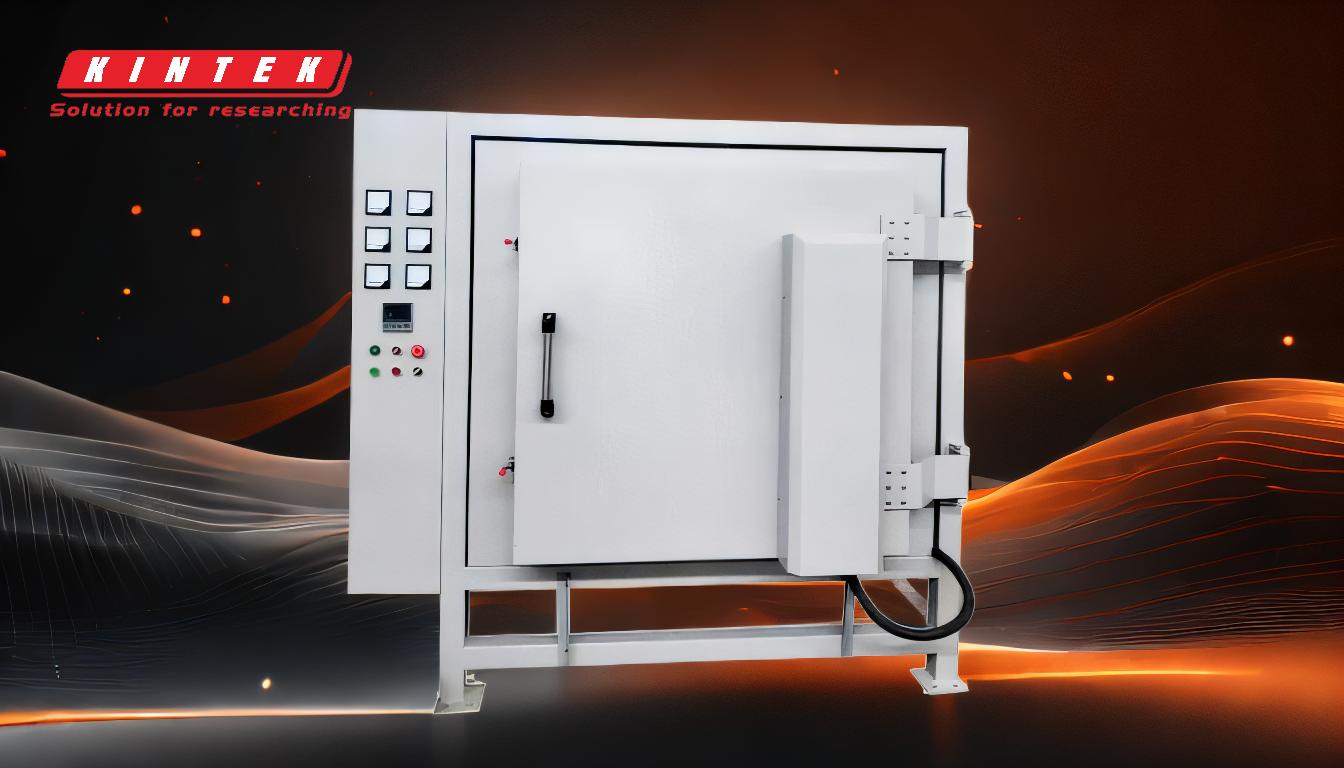
-
Vacuum Creation:
- Purpose: The first step in the sputtering process is to create a vacuum within the reaction chamber. This is done to remove any moisture and impurities that could interfere with the coating process.
- Pressure: The internal pressure is dropped to around 1 Pa (0.0000145 psi) to ensure a clean environment.
- Importance: A vacuum environment is crucial for preventing contamination and ensuring the quality of the thin film.
-
Introduction of Inert Gas:
- Gas Type: An inert gas, typically argon, is pumped into the chamber to create a low-pressure atmosphere.
- Role: The inert gas is used to create a plasma when ionized, which is essential for the sputtering process.
- Pressure: The gas is introduced at higher pressures (10-1 - 10-3 mbar) after the initial vacuum is created.
-
Heating the Chamber:
- Temperature Range: The chamber is heated to temperatures ranging from 150 – 750°C (302 – 1382°F), depending on the specific coating being applied.
- Purpose: Heating helps in achieving the desired properties of the thin film, such as adhesion and density.
- Control: Precise temperature control is necessary to ensure consistent film quality.
-
Creation of Magnetic Field:
- Setup: The tools (substrate) are placed between the metallic materials (target) and an electromagnet.
- Magnetic Field: A magnetic field is created around the tools to confine the plasma and enhance the sputtering efficiency.
- Effect: The magnetic field helps in directing the ionized gas towards the target, increasing the rate of sputtering.
-
Ionization of Gas:
- High Voltage Application: A high voltage (3-5 kV) is applied along the magnetic field to ionize the argon atoms.
- Plasma Formation: The ionized gas forms a plasma, which is essential for the sputtering process.
- Energy Transfer: The ions gain kinetic energy and are directed towards the target material.
-
Sputtering of Target Material:
- Bombardment: The positively charged argon ions collide with the target material, causing atoms to be ejected.
- Ejection: The ejected atoms form a vapor stream that travels through the chamber.
- Deposition: The sputtered atoms condense on the substrate, forming a thin film with specific properties.
-
Film Formation:
- Nucleation: The sputtered atoms nucleate on the substrate, forming a film.
- Properties: The film can have specific properties such as reflectivity, electrical resistivity, or ionic resistivity.
- Control: The process allows for precise control over film morphology, grain orientation, grain size, and density.
-
Advantages of Sputtering:
- Precision: The sputtering process is highly accurate and is used to produce precision products.
- Versatility: It can be used to deposit a wide range of materials onto various substrates.
- Quality: The thin films produced have high quality and uniformity, making them suitable for demanding applications.
By following these steps, the sputtering process ensures the deposition of high-quality thin films with precise control over their properties, making it a valuable technique in surface treatment and coating applications.
Summary Table:
Step | Key Details |
---|---|
Vacuum Creation | Pressure: 1 Pa; Removes moisture and impurities for contamination-free coating. |
Inert Gas Introduction | Argon gas introduced at 10-1 - 10-3 mbar; creates plasma for sputtering. |
Heating the Chamber | Temperature: 150 – 750°C; enhances film adhesion and density. |
Magnetic Field Setup | Confines plasma, directs ions toward the target for efficient sputtering. |
Ionization of Gas | High voltage (3-5 kV) ionizes argon, forming plasma for energy transfer. |
Target Sputtering | Ions bombard target, ejecting atoms that form a vapor stream for deposition. |
Film Formation | Sputtered atoms nucleate on substrate, creating films with controlled properties. |
Advantages | Precision, versatility, and high-quality coatings for demanding applications. |
Discover how sputtering can elevate your coating processes—contact our experts today!