PVD (Physical Vapor Deposition) coating is a modern vapor deposition technology used to apply extremely thin, high-performance coatings to materials. These coatings are characterized by their high purity, uniformity, and excellent adhesion to the substrate. PVD coatings are typically 0.5 to 5 μm thick and offer significant improvements in surface hardness, chemical stability, wear resistance, and adjustability of product appearance. The process involves converting a solid material into its vapor phase in a vacuum, which then condenses to coat the workpiece. Key factors influencing PVD coating quality include line-of-sight transfer, surface pretreatment, cleanliness, and avoiding trapped air in tightly sealed holes. PVD coatings are known for their durability, corrosion resistance, and ability to eliminate the need for additional protective topcoats.
Key Points Explained:
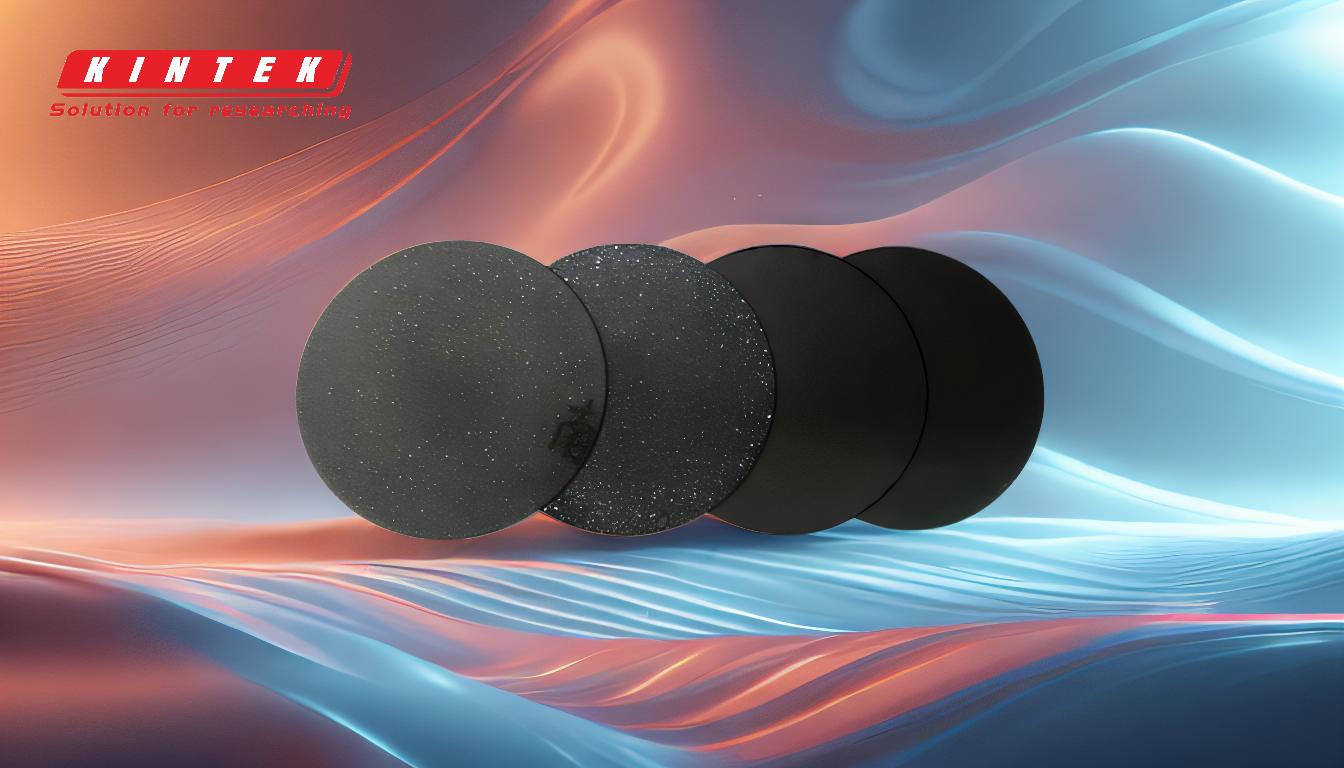
-
Coating Thickness and Uniformity:
- PVD coatings are extremely thin, typically ranging from 0.5 to 5 μm. This thinness allows for precise control over the coating's properties while maintaining the substrate's original dimensions.
- The uniformity of the coating is crucial for ensuring consistent performance across the entire surface of the workpiece. High uniformity is achieved through controlled deposition processes in a vacuum environment.
-
Adhesion and Durability:
- PVD coatings exhibit excellent adhesion to the substrate, which is essential for their durability and performance. This strong bond ensures that the coating remains intact under mechanical stress, high temperatures, and corrosive environments.
- The durability of PVD coatings often eliminates the need for additional protective topcoats, making them a cost-effective solution for many applications.
-
Surface Hardness and Wear Resistance:
- PVD coatings are known for their high surface hardness, which significantly improves the wear resistance of the coated material. This makes them ideal for applications where the material is subjected to abrasive forces or high friction.
- The enhanced wear resistance extends the lifespan of tools and components, reducing maintenance costs and downtime.
-
Chemical Stability and Corrosion Resistance:
- PVD coatings offer excellent chemical stability, making them resistant to corrosion and degradation in harsh environments. This is particularly important for applications in industries such as aerospace, automotive, and medical devices.
- The corrosion resistance of PVD coatings ensures that the coated materials maintain their integrity and performance over time, even when exposed to corrosive substances.
-
Line-of-Sight Transfer and Surface Pretreatment:
- PVD coating is a line-of-sight process, meaning that only surfaces directly exposed to the vaporized material will be coated. This limitation requires careful consideration of the workpiece's geometry and the need for surface pretreatment.
- Surface pretreatment is essential to ensure proper adhesion and uniformity of the coating. This may involve cleaning, polishing, or other surface preparation techniques to remove contaminants and create an optimal surface for coating.
-
Surface Cleanliness and Trapped Air:
- Surface cleanliness is critical in PVD coating, as even small particles or contaminants can negatively affect the coating's quality and adhesion. Thorough cleaning processes are necessary to achieve the desired results.
- Trapped air in tightly sealed holes or cavities can interfere with the coating process, leading to uneven or incomplete coverage. Design considerations should avoid such features to ensure consistent coating quality.
-
Temperature and Environmental Considerations:
- PVD coatings are applied at relatively low temperatures compared to other coating methods, reducing the risk of thermal distortion or damage to the substrate. This makes PVD suitable for coating temperature-sensitive materials.
- The vacuum environment used in PVD coating minimizes contamination and ensures a high-purity coating, further enhancing the material's performance and longevity.
-
Aesthetic and Functional Properties:
- PVD coatings can be tailored to achieve various aesthetic effects, including metallic luster and color variations. These coatings do not require additional polishing to achieve a high-quality finish.
- The adjustability of the coating's appearance allows for customization to meet specific design requirements, enhancing both the functional and visual appeal of the coated material.
In summary, PVD coating standards emphasize thin, uniform, and durable coatings with excellent adhesion, hardness, and corrosion resistance. The process requires careful attention to surface preparation, cleanliness, and design considerations to achieve optimal results. PVD coatings offer a versatile and cost-effective solution for enhancing the performance and appearance of materials in various industries.
Summary Table:
Key Feature | Description |
---|---|
Coating Thickness | 0.5 to 5 μm, ensuring precision and minimal impact on substrate dimensions. |
Adhesion & Durability | Excellent bond strength, eliminating the need for additional protective topcoats. |
Surface Hardness | Significantly improves wear resistance, ideal for high-friction applications. |
Corrosion Resistance | High chemical stability protects against harsh environments. |
Line-of-Sight Transfer | Requires careful surface pretreatment and design considerations. |
Aesthetic Properties | Customizable metallic luster and color variations for functional and visual appeal. |
Upgrade your materials with PVD coating—contact us today for expert solutions!