Sputtered films, while offering excellent uniformity, density, purity, and adhesion, are subject to internal stresses that can significantly impact their performance and durability. These stresses arise from various factors, including the deposition process, thermal expansion mismatches, and the intrinsic properties of the materials used. Understanding and managing these stresses is crucial for optimizing the functionality and longevity of sputtered films in applications such as optical coatings, electronics, and protective layers.
Key Points Explained:
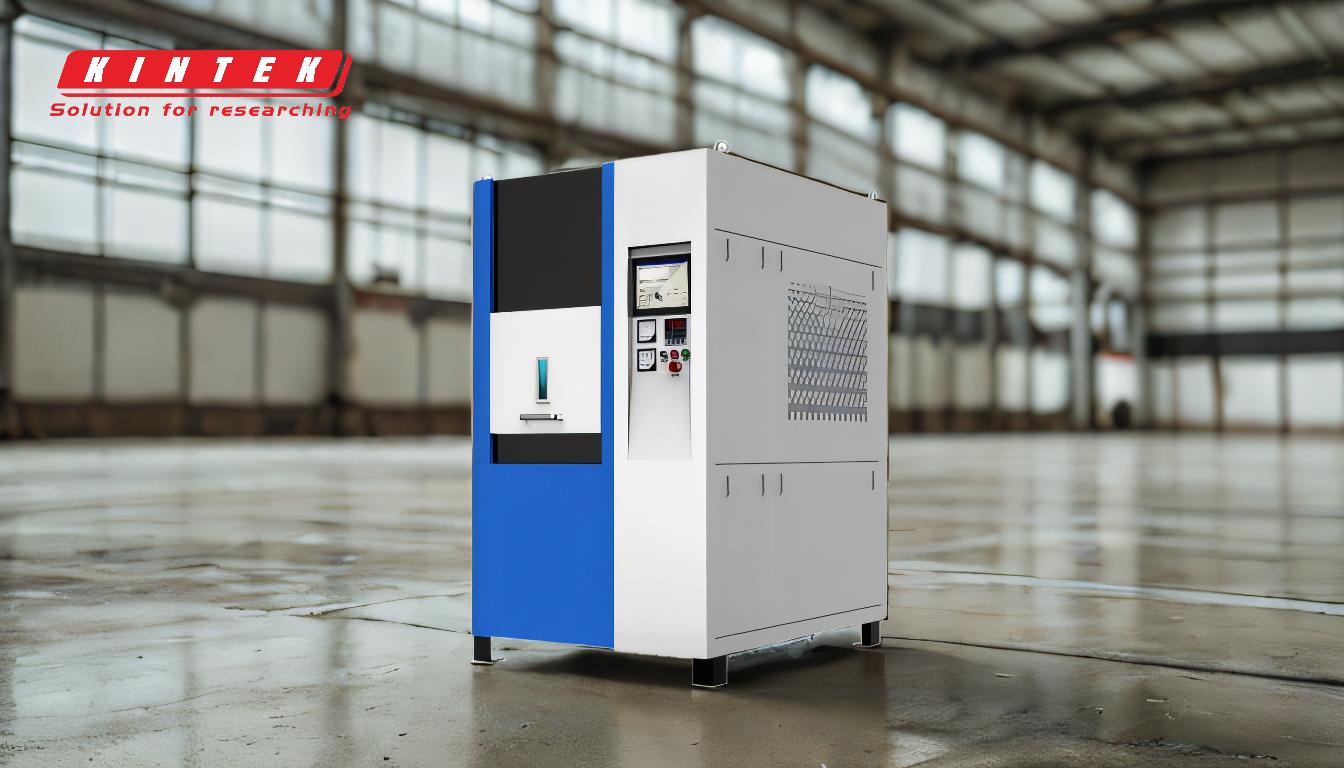
-
Types of Stress in Sputtered Films:
- Intrinsic Stress: This type of stress originates from the deposition process itself. It is caused by the energetic bombardment of ions during sputtering, which can lead to defects, dislocations, and lattice distortions in the film. Intrinsic stress can be either compressive or tensile, depending on the deposition conditions and material properties.
- Thermal Stress: Thermal stress arises due to differences in the thermal expansion coefficients between the film and the substrate. As the film cools after deposition, the mismatch in expansion rates can induce significant stress, which may lead to cracking or delamination if not properly managed.
-
Factors Influencing Stress in Sputtered Films:
- Deposition Parameters: The energy and angle of the incoming ions, as well as the deposition rate, can significantly affect the stress levels in the film. Higher energy ions tend to increase compressive stress, while lower energy ions may lead to tensile stress.
- Substrate Temperature: The temperature of the substrate during deposition plays a critical role. Higher temperatures can reduce stress by allowing atoms to find more stable positions, but excessively high temperatures may exacerbate thermal stress.
- Material Properties: The choice of target material and its inherent properties, such as melting point and crystal structure, influence the stress. Materials with high melting points, like tantalum, can be more prone to stress due to their complex deposition dynamics.
- Gas Pressure and Composition: The type and pressure of the sputtering gas can alter the stress profile. For example, using reactive gases like oxygen or nitrogen can lead to the formation of compounds with different stress characteristics compared to pure metal films.
-
Impact of Stress on Film Performance:
- Adhesion: Excessive stress can compromise the adhesion of the film to the substrate, leading to peeling or delamination. This is particularly critical in applications where the film must withstand mechanical or thermal cycling.
- Durability: High stress levels can make the film more susceptible to damage, such as scratching or cracking, reducing its overall durability and lifespan.
- Optical and Electrical Properties: Stress can alter the optical and electrical properties of the film, affecting its performance in applications like solar coatings or electronic devices.
-
Mitigation Strategies:
- Optimizing Deposition Conditions: Adjusting parameters such as ion energy, deposition rate, and substrate temperature can help control stress levels. For instance, using a lower deposition rate and moderate substrate temperature can reduce intrinsic stress.
- Post-Deposition Annealing: Annealing the film after deposition can relieve stress by allowing atoms to rearrange into more stable configurations. This process can also improve the film's mechanical and thermal stability.
- Use of Interlayers: Introducing intermediate layers with compatible thermal expansion coefficients can mitigate thermal stress. These interlayers act as buffers, reducing the stress transmitted to the main film.
- Material Selection: Choosing materials with similar thermal expansion coefficients to the substrate can minimize thermal stress. Additionally, selecting materials with lower intrinsic stress tendencies can improve overall film quality.
-
Measurement and Characterization of Stress:
- X-ray Diffraction (XRD): XRD can be used to measure the lattice parameters of the film, providing insights into the stress state. Changes in lattice spacing can indicate the presence of compressive or tensile stress.
- Curvature Method: This method involves measuring the curvature of the substrate before and after deposition. The change in curvature is directly related to the stress in the film.
- Raman Spectroscopy: For certain materials, Raman spectroscopy can detect stress-induced shifts in vibrational modes, offering a non-destructive way to assess stress levels.
In conclusion, stress in sputtered films is a multifaceted issue that requires careful consideration of deposition parameters, material properties, and post-deposition treatments. By understanding and controlling these factors, it is possible to produce high-quality sputtered films with minimal stress, ensuring their reliability and performance in various applications.
Summary Table:
Aspect | Details |
---|---|
Types of Stress | Intrinsic (from deposition) and Thermal (from thermal expansion mismatch) |
Key Influencing Factors | Deposition parameters, substrate temperature, material properties, gas type |
Impact on Performance | Adhesion, durability, optical & electrical properties |
Mitigation Strategies | Optimize deposition, post-deposition annealing, interlayers, material choice |
Measurement Techniques | XRD, curvature method, Raman spectroscopy |
Discover how to enhance your sputtered films' performance—contact our experts today!