Sputtered thin films often experience internal stress due to the nature of the sputtering process and the materials involved. This stress arises from factors such as differences in thermal expansion coefficients between the film and substrate, intrinsic stress from the deposition process, and microstructural changes during film growth. The stress can be either tensile (pulling the film apart) or compressive (pushing the film together), depending on the deposition conditions and material properties. Managing this stress is critical for ensuring the durability, adhesion, and performance of the thin film in applications like solar cells, micro-electrochemical devices, and optical coatings. Understanding and controlling stress requires careful selection of materials, process parameters, and post-deposition treatments.
Key Points Explained:
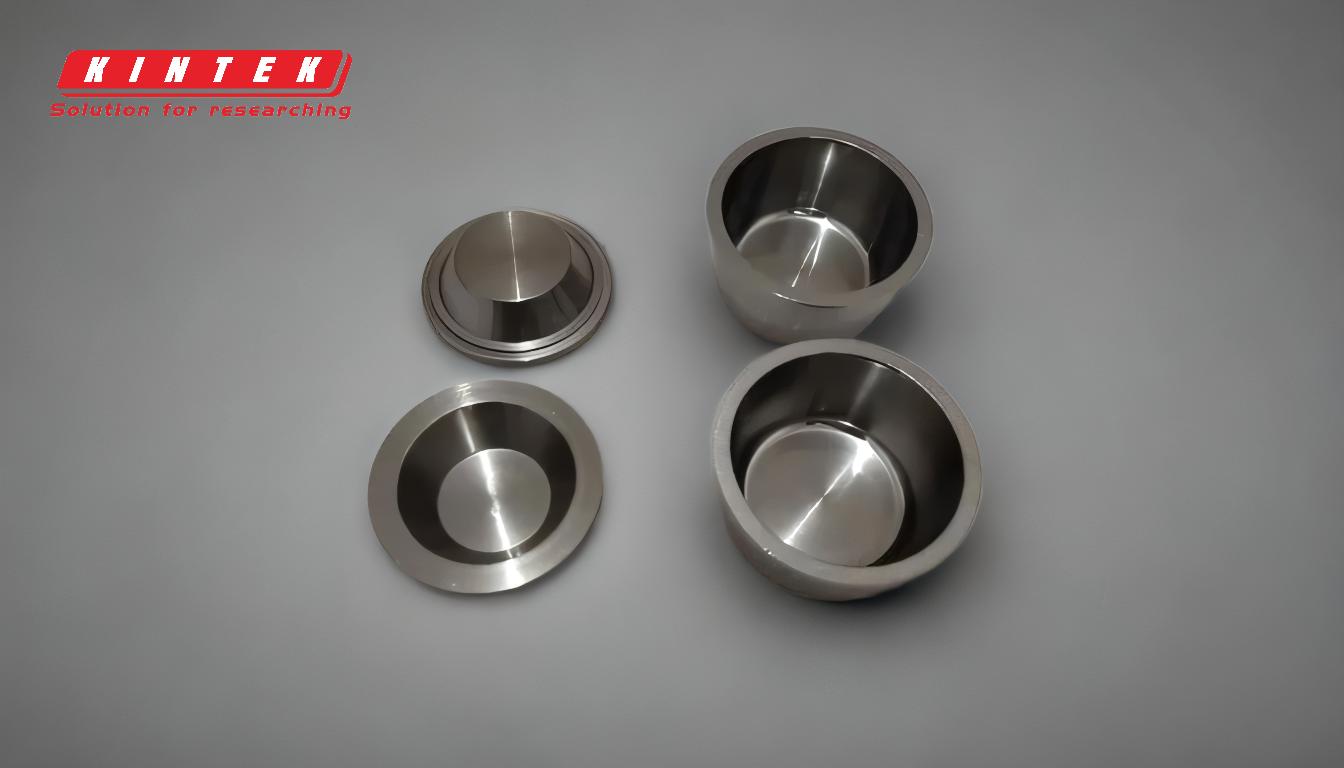
-
Origins of Stress in Sputtered Thin Films:
- Thermal Stress: Occurs due to differences in thermal expansion coefficients between the thin film and the substrate. When the film cools after deposition, mismatched expansion or contraction can lead to tensile or compressive stress.
- Intrinsic Stress: Arises from the deposition process itself. Factors like ion bombardment, adatom mobility, and grain growth during sputtering can create internal stresses within the film.
- Microstructural Stress: Results from defects, voids, or columnar growth structures in the film. These imperfections can alter the film's mechanical properties and contribute to stress.
-
Types of Stress:
- Tensile Stress: Pulls the film apart, often caused by shrinkage during cooling or insufficient adatom mobility during deposition.
- Compressive Stress: Pushes the film together, typically resulting from ion bombardment or incorporation of excess atoms during deposition.
-
Factors Influencing Stress:
- Deposition Parameters: Parameters like sputtering power, gas pressure, and substrate temperature can significantly affect stress levels. For example, higher sputtering power may increase compressive stress due to enhanced ion bombardment.
- Material Properties: The choice of target material and its properties, such as melting point and atomic structure, influence stress. For instance, metals with high melting points may exhibit higher intrinsic stress.
- Substrate Characteristics: The substrate's thermal and mechanical properties, such as thermal conductivity and rigidity, play a role in stress development.
-
Impact of Stress on Film Properties:
- Adhesion: Excessive stress can weaken the bond between the film and substrate, leading to delamination or peeling.
- Durability: High stress levels make the film more prone to cracking, scratching, or chemical degradation, especially in "soft-coat" sputtered films.
- Performance: Stress can alter optical, electrical, and mechanical properties, affecting applications like solar cells, optical coatings, and micro-electrochemical devices.
-
Strategies to Control Stress:
- Optimizing Deposition Conditions: Adjusting parameters like sputtering power, gas pressure, and substrate temperature can help manage stress levels.
- Post-Deposition Treatments: Annealing or heat treatments can relieve stress by allowing atoms to rearrange and reduce defects.
- Material Selection: Choosing materials with compatible thermal expansion coefficients and mechanical properties can minimize stress.
-
Applications and Stress Considerations:
- Solar Cells: Stress management is crucial for ensuring long-term stability and efficiency in thin-film solar cells.
- Optical Coatings: Uniform stress distribution is essential for maintaining optical performance and durability in sputtered films used for reflective or anti-reflective coatings.
- Micro-Electrochemical Devices: Stress control ensures proper adhesion and functionality of platinum or other metal coatings in devices like fuel cells and sensors.
By understanding the origins, types, and impacts of stress in sputtered thin films, manufacturers can optimize deposition processes and material choices to produce high-quality, durable coatings for advanced applications.
Summary Table:
Aspect | Details |
---|---|
Origins of Stress | Thermal stress, intrinsic stress, microstructural stress |
Types of Stress | Tensile (pulling apart), compressive (pushing together) |
Influencing Factors | Deposition parameters, material properties, substrate characteristics |
Impact on Properties | Adhesion, durability, performance |
Control Strategies | Optimize deposition, post-deposition treatments, material selection |
Applications | Solar cells, optical coatings, micro-electrochemical devices |
Optimize your sputtered thin films for superior performance—contact our experts today!