Diamond-like carbon (DLC) films are a class of amorphous carbon materials that exhibit a combination of diamond-like (sp³) and graphite-like (sp²) carbon bonds. This unique structure gives DLC films their exceptional properties, such as high hardness, low friction, chemical resistance, and biocompatibility. The structure of DLC films is influenced by the deposition process and the substrate used, which affects their optical properties, thickness, and performance. DLC films are widely used in protective coatings, wear-resistant applications, and optical sensing due to their tailored properties.
Key Points Explained:
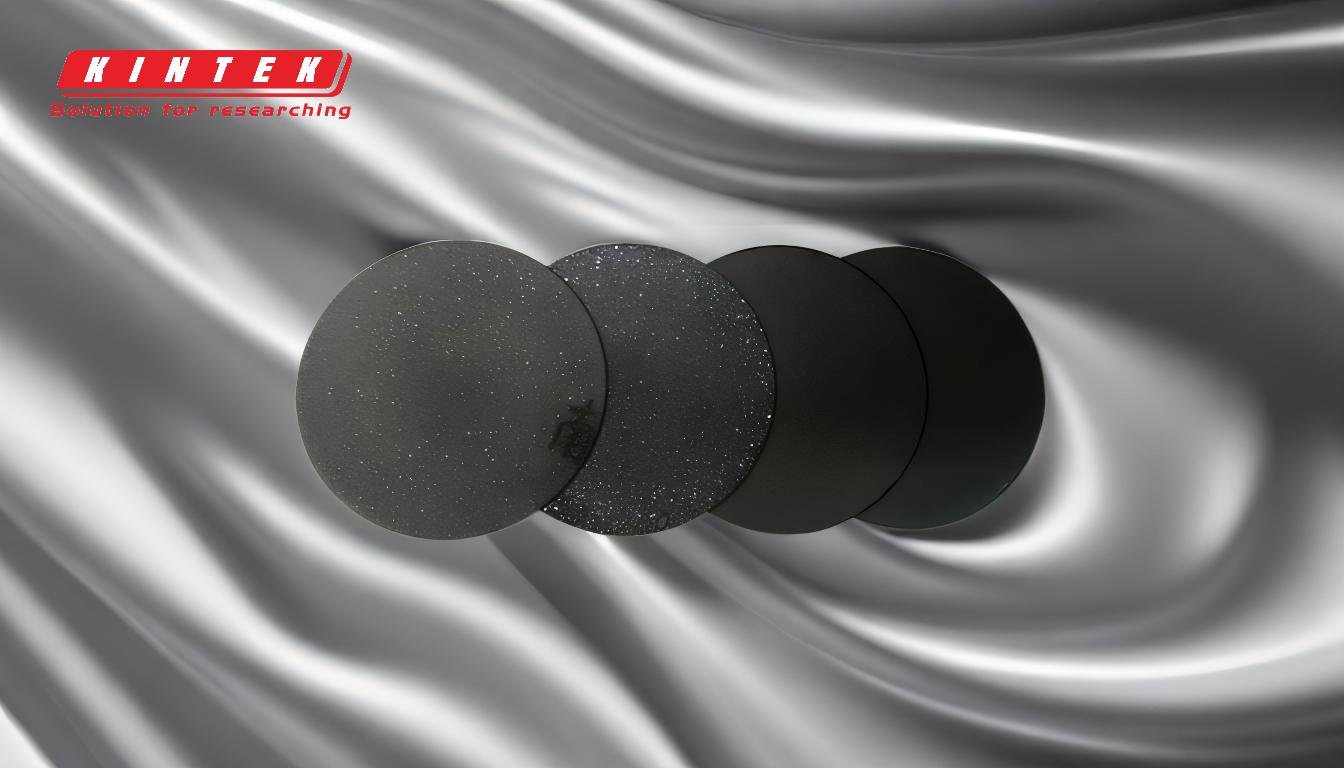
-
Composition and Bonding Structure:
- DLC films consist of a mixture of sp³ (diamond-like) and sp² (graphite-like) carbon bonds.
- The sp³ bonds contribute to the hardness and durability of the film, similar to diamond.
- The sp² bonds provide flexibility and low friction, similar to graphite.
- The ratio of sp³ to sp² bonds can vary depending on the deposition process, influencing the film's properties.
-
Amorphous Nature:
- Unlike crystalline diamond or graphite, DLC films are amorphous, meaning they lack a long-range ordered structure.
- This amorphous nature allows for a wide range of tunable properties, making DLC films versatile for various applications.
-
Deposition Process Influence:
- The structure and properties of DLC films are highly dependent on the deposition method, such as Plasma-Assisted Chemical Vapor Deposition (PACVD).
- Process parameters like temperature, pressure, and gas composition affect the sp³/sp² ratio, film thickness, and adhesion to the substrate.
-
Substrate Influence:
- The substrate material significantly impacts the optical properties, thickness, and adhesion of the DLC film.
- Proper substrate preparation and compatibility are crucial for achieving desired film performance.
-
Functional Properties:
- High Hardness: Due to the sp³ bonds, DLC films exhibit high hardness, making them suitable for wear-resistant applications.
- Low Friction: The presence of sp² bonds results in a low coefficient of friction, enhancing sliding properties.
- Chemical Resistance: DLC films are chemically inert, making them resistant to corrosion and suitable for harsh environments.
- Biocompatibility: The biocompatibility of DLC films makes them ideal for medical and biomedical applications.
-
Applications:
- Protective Coatings: DLC films are used to protect surfaces from wear, corrosion, and chemical attack.
- Optical Applications: Their precise control over thickness and refractive index makes them suitable for antireflective coatings and optical sensing.
- Biomedical Uses: The biocompatibility and low friction of DLC films make them ideal for medical implants and devices.
-
Scalability and Customization:
- The properties of DLC films can be tailored by adjusting the deposition process, making them scalable for industrial applications.
- This customization allows for the optimization of films for specific uses, such as enhancing sliding properties or improving optical performance.
In summary, the structure of DLC films is a complex interplay of sp³ and sp² carbon bonds within an amorphous matrix, influenced by deposition processes and substrate materials. This structure underpins their remarkable properties, making them invaluable in a wide range of industrial, optical, and biomedical applications.
Summary Table:
Key Aspect | Details |
---|---|
Bonding Structure | Mixture of sp³ (diamond-like) and sp² (graphite-like) carbon bonds. |
Amorphous Nature | Lacks long-range ordered structure, enabling tunable properties. |
Deposition Influence | Process parameters (temperature, pressure, gas) affect sp³/sp² ratio. |
Substrate Influence | Substrate material impacts optical properties, thickness, and adhesion. |
Functional Properties | High hardness, low friction, chemical resistance, and biocompatibility. |
Applications | Protective coatings, optical sensing, biomedical implants, and more. |
Scalability | Properties can be tailored for industrial and specific application needs. |
Discover how DLC films can enhance your applications—contact us today for expert guidance!