The temperature of a plasma reactor varies significantly depending on its type and application. For example, in fusion reactors like ITER, plasma temperatures can reach up to 150 million °C to facilitate nuclear fusion. In contrast, plasma-enhanced chemical vapor deposition (PECVD) systems, used for thin-film deposition, operate at much lower temperatures, typically between 200°C and 500°C. The operating pressure in PECVD systems is also much lower, ranging from 0.1 to 10 Torr, which helps maintain film uniformity and minimize substrate damage. These differences in temperature and pressure are dictated by the specific requirements of the processes, such as the need for high-energy conditions in fusion versus the need for controlled chemical reactions in PECVD.
Key Points Explained:
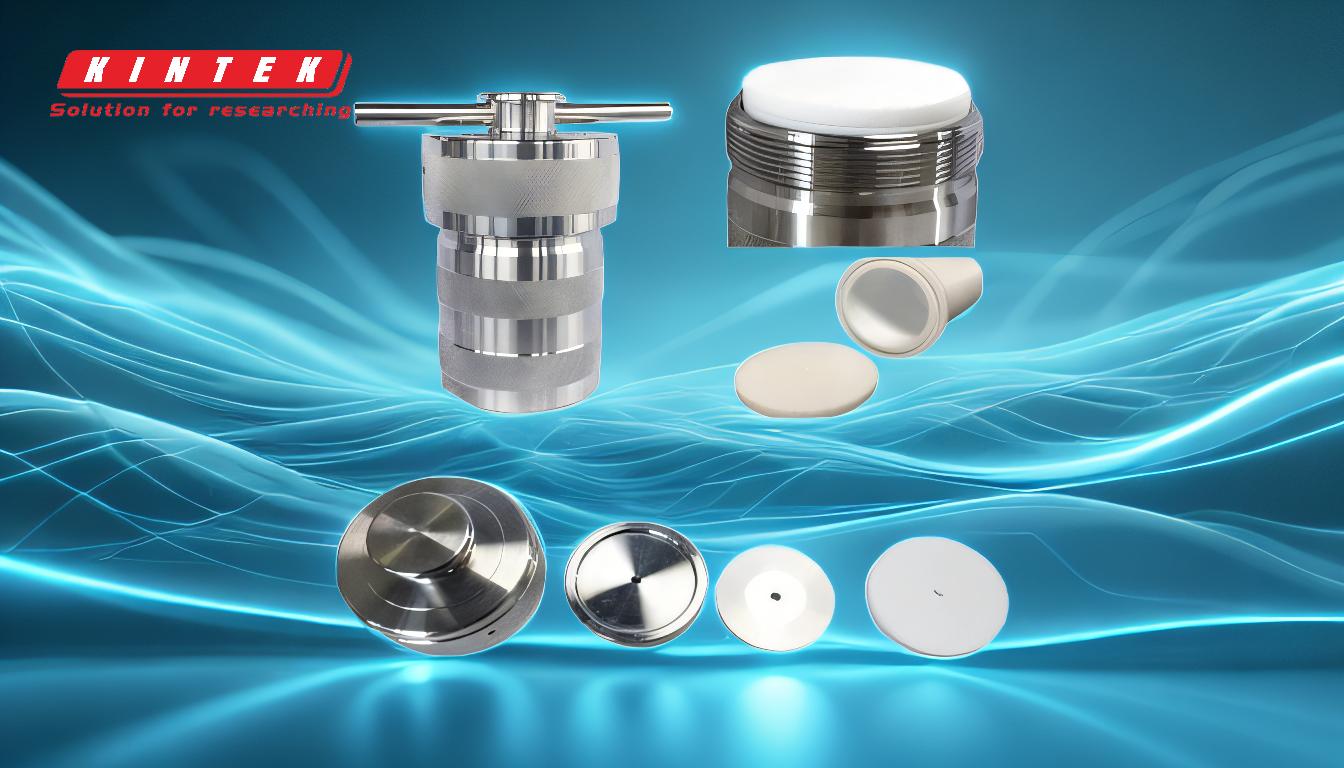
-
Fusion Reactors (e.g., ITER):
- Temperature: Plasma in fusion reactors like ITER reaches extremely high temperatures, up to 150 million °C. This is necessary to overcome the Coulomb barrier and enable the fusion of deuterium and tritium nuclei, releasing energy in the process.
- Purpose: The high temperature ensures that the kinetic energy of the particles is sufficient for nuclear fusion, which is the core objective of such reactors.
- Context: These reactors are designed for energy production through nuclear fusion, requiring extreme conditions that are not typical in other plasma applications.
-
Plasma-Enhanced Chemical Vapor Deposition (PECVD):
- Temperature: PECVD systems operate at much lower temperatures, typically between 200°C and 500°C. This range is suitable for thin-film deposition on substrates without causing thermal damage.
- Pressure: The operating pressure in PECVD is low, usually between 0.1 and 10 Torr. This low pressure reduces particle scattering and promotes uniform film deposition.
- Purpose: The lower temperatures and pressures in PECVD are optimized for chemical reactions that deposit thin films on substrates, making it ideal for semiconductor manufacturing and other applications requiring precise material deposition.
-
General Plasma Processing:
- Pressure Range: Plasma processing systems, including PECVD, typically operate at pressures ranging from a few millitorrs to a few torr. This range is suitable for maintaining plasma stability and facilitating the desired chemical or physical processes.
- Electron and Ion Densities: In PECVD, electron and positive ion densities are typically between 10^9 and 10^11/cm^3, with average electron energies ranging from 1 to 10 eV. These conditions are conducive to chemical reactions at lower temperatures compared to thermal CVD reactors.
- Flexibility: PECVD systems can operate at both lower and higher temperatures depending on the specific requirements of the process, offering flexibility in material deposition.
-
Comparison of Plasma Reactors:
- Fusion vs. PECVD: The temperature difference between fusion reactors and PECVD systems is stark, with fusion reactors requiring extreme heat for nuclear reactions, while PECVD systems operate at much lower temperatures for chemical deposition.
- Application-Specific Conditions: The operating conditions of plasma reactors are tailored to their specific applications. Fusion reactors require high temperatures and pressures to achieve nuclear fusion, whereas PECVD systems are optimized for controlled chemical reactions at lower temperatures and pressures.
In summary, the temperature of a plasma reactor is highly dependent on its intended application. Fusion reactors like ITER require extremely high temperatures to achieve nuclear fusion, while PECVD systems operate at much lower temperatures suitable for thin-film deposition. The operating pressure and other conditions are also tailored to the specific requirements of each process, ensuring optimal performance and results.
Summary Table:
Parameter | Fusion Reactors (e.g., ITER) | PECVD Systems |
---|---|---|
Temperature | Up to 150 million °C | 200°C to 500°C |
Pressure | High (fusion conditions) | 0.1 to 10 Torr |
Purpose | Nuclear fusion for energy production | Thin-film deposition for semiconductors |
Key Feature | Extreme heat for nuclear reactions | Controlled chemical reactions |
Need help selecting the right plasma reactor for your application? Contact our experts today!