The temperature of a pyrolysis reactor typically ranges between 350-400°C for high-temperature pyrolysis, which is essential for breaking down waste materials into valuable byproducts like pyrolysis oil, carbon black, and syn-gas. However, medium-temperature pyrolysis can occur at higher temperatures, between 600-700°C, depending on the specific process and materials being treated. The reactor relies on an external heat source and operates as a closed system, adhering to thermodynamic principles. Factors such as furnace temperature, residence time, and internal pressure significantly influence the efficiency and performance of the pyrolysis process, making proper control and maintenance critical for optimal results.
Key Points Explained:
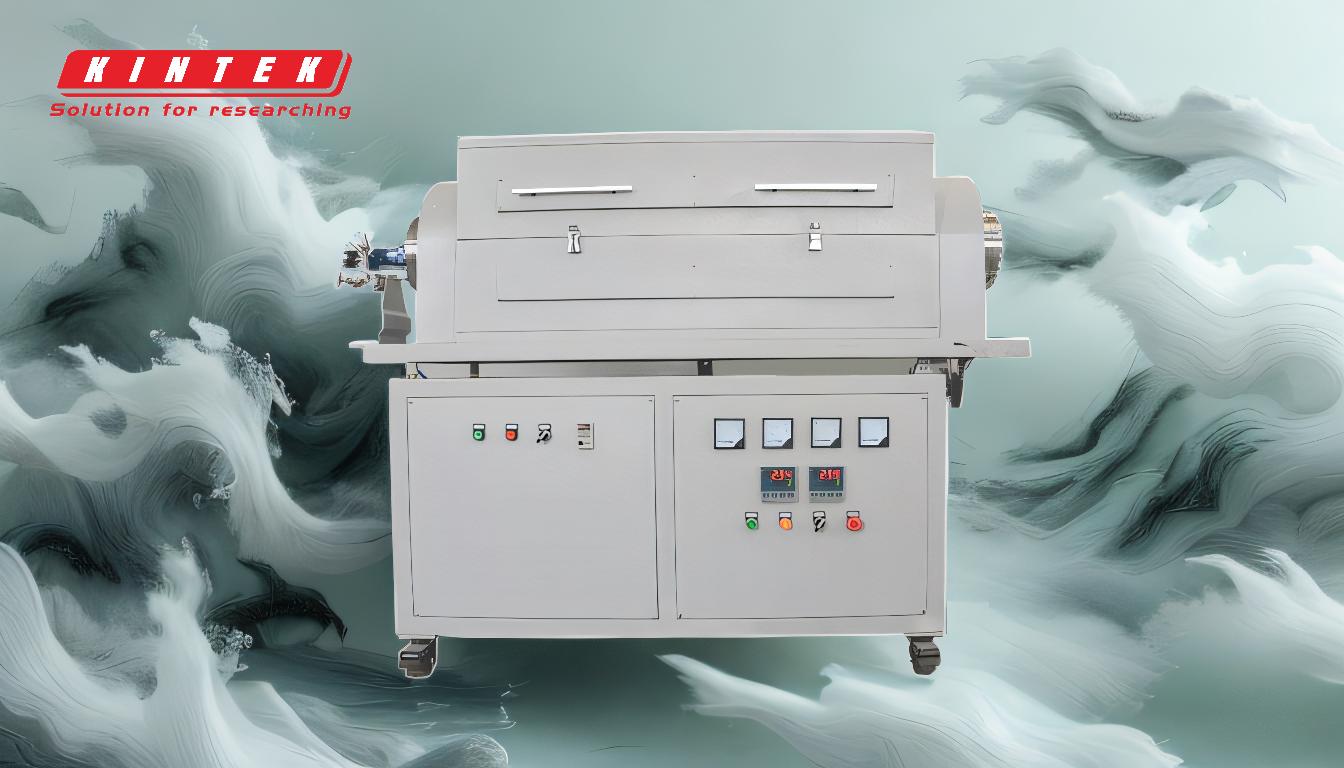
-
Temperature Range for Pyrolysis Reactors:
- High-temperature pyrolysis typically operates between 350-400°C. This range is necessary to ensure the decomposition of waste materials into valuable products such as pyrolysis oil, carbon black, and syn-gas.
- Medium-temperature pyrolysis can occur at higher temperatures, ranging from 600-700°C, depending on the type of feedstock and desired output.
-
Purpose of Temperature Control:
- The temperature is critical for initiating and sustaining the pyrolysis process, which involves the thermal decomposition of organic materials in the absence of oxygen.
- Higher temperatures ensure complete breakdown of complex molecules, leading to the production of useful byproducts.
-
External Heat Supply:
- Pyrolysis reactors rely on an external heat source to maintain the required temperatures. This ensures consistent and controlled heating, which is essential for efficient operation.
- The reactor operates as a closed system, meaning it is sealed to prevent oxygen entry, which could otherwise lead to combustion instead of pyrolysis.
-
Factors Affecting Efficiency:
- Furnace Temperature: Precise control of temperature is crucial for optimizing the pyrolysis process. Too low a temperature may result in incomplete decomposition, while excessively high temperatures can lead to unwanted byproducts.
- Residence Time: The duration that materials spend inside the reactor affects the extent of decomposition. Longer residence times may improve yield but can also increase energy consumption.
- Internal Pressure: Pressure control is important for maintaining the integrity of the reactor and ensuring safe operation. It also influences the rate of decomposition and the quality of the end products.
-
Importance of Proper Operation and Maintenance:
- Regular maintenance and proper operation are essential to ensure the reactor operates at peak efficiency and remains safe.
- Monitoring and controlling the temperature, residence time, and pressure are key to achieving consistent and high-quality outputs.
-
Thermodynamic Principles:
- Pyrolysis reactors operate based on thermodynamic principles, which govern the transfer of heat and the behavior of materials under high temperatures.
- Understanding these principles helps in designing and operating reactors that maximize energy efficiency and product yield.
By understanding these key points, equipment and consumable purchasers can make informed decisions about the specifications and maintenance requirements of pyrolysis reactors, ensuring optimal performance and safety.
Summary Table:
Key Factor | Details |
---|---|
High-Temp Pyrolysis | 350-400°C for breaking down waste into pyrolysis oil, carbon black, and syn-gas. |
Medium-Temp Pyrolysis | 600-700°C for specific feedstocks and processes. |
External Heat Source | Ensures consistent and controlled heating in a closed system. |
Critical Factors | Furnace temperature, residence time, and internal pressure. |
Maintenance | Regular monitoring ensures efficiency, safety, and high-quality outputs. |
Ready to optimize your pyrolysis process? Contact our experts today for tailored solutions!