Induction heating is a process that uses electromagnetic induction to generate heat within a conductive material. The temperature achieved during induction heating can vary widely depending on several factors, including the material's properties, the frequency of the alternating current, and the specific application requirements. Generally, induction heating can achieve temperatures ranging from a few hundred degrees Celsius to over 2000°C, making it suitable for a variety of industrial applications such as metal hardening, brazing, and melting.
Key Points Explained:
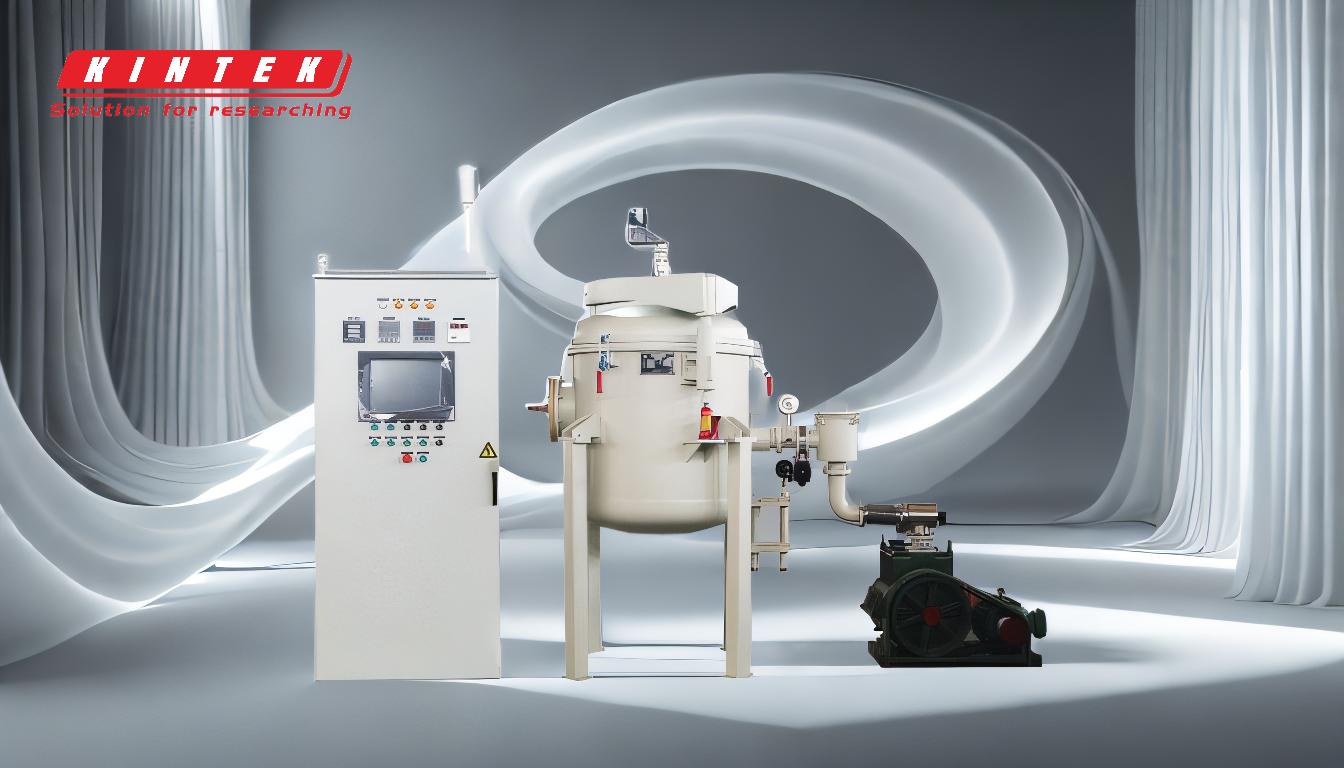
-
Material Properties Influence Heating Temperature:
- Conductivity and Resistivity: Materials with higher electrical conductivity, such as copper and aluminum, heat up more efficiently due to lower resistance to the flow of eddy currents. Conversely, materials with higher resistivity, like certain steels, may heat up more quickly but require more energy to reach the same temperature.
- Magnetic Properties: Magnetic materials, such as iron and some steels, generate heat through both eddy currents and hysteresis effects. This dual mechanism allows these materials to heat up more rapidly compared to non-magnetic materials.
- Size and Thickness: Smaller and thinner materials heat up faster because the induced currents have less material to penetrate. This is particularly important in applications where rapid heating is required, such as in surface hardening.
-
Frequency of Alternating Current:
- Higher Frequency: Higher-frequency alternating currents result in lower heating depth penetration, which is ideal for surface heating applications like case hardening. The skin effect causes the current to concentrate near the surface, leading to rapid surface heating.
- Lower Frequency: Lower frequencies are used for deeper penetration, which is necessary for through-heating applications like forging or melting. The choice of frequency is crucial in determining the heating profile and the final temperature distribution within the material.
-
Application-Specific Temperature Requirements:
- Metal Hardening: For processes like induction hardening, the temperature is typically raised to the austenitizing range (around 750-900°C for steel) to allow for the transformation of the microstructure, followed by rapid quenching to achieve the desired hardness.
- Brazing and Soldering: These processes require lower temperatures, typically between 450°C and 800°C, depending on the filler material used. The precise temperature is critical to ensure proper flow and bonding of the filler material without damaging the base material.
- Melting: In induction melting, temperatures can exceed 2000°C, especially when melting refractory metals like tungsten or molybdenum. The high temperatures are necessary to overcome the material's high melting point and achieve a molten state.
-
Vacuum Heat Treatment Considerations:
- Technical and Performance Requirements: In vacuum heat treatment, the heating temperature is carefully selected based on the technical requirements, service conditions, and performance needs of the workpiece. The goal is to minimize deformation while achieving the desired material properties.
- Minimizing Deformation: Lowering the heating temperature can reduce the risk of deformation, especially in complex or thin-walled components. However, the temperature must still be high enough to achieve the necessary metallurgical transformations.
-
Induction Furnace Features:
- Zero Voltage Startup: Modern induction furnaces often feature a zero voltage startup, which begins the heating process gently and with high initial power. This minimizes the impact on the electric network and allows for precise control over the heating process.
- Energy Efficiency: The ability to control the frequency and power of the induction heating process contributes to energy efficiency, as the heat is generated directly within the material rather than being transferred from an external source.
In summary, the temperature of the induction heating process is highly variable and depends on the material being heated, the frequency of the alternating current, and the specific application requirements. Understanding these factors is crucial for optimizing the induction heating process to achieve the desired results efficiently and effectively.
Summary Table:
Factor | Impact on Temperature |
---|---|
Material Properties | - Conductivity: Higher conductivity = efficient heating. |
- Magnetic properties: Magnetic materials heat faster due to eddy currents and hysteresis. | |
- Size & thickness: Smaller/thinner materials heat faster. | |
Frequency of Alternating Current | - Higher frequency: Better for surface heating (e.g., case hardening). |
- Lower frequency: Better for deep heating (e.g., melting). | |
Application Requirements | - Metal hardening: 750-900°C. |
- Brazing/soldering: 450-800°C. | |
- Melting: Up to 2000°C+ for refractory metals. |
Optimize your induction heating process today—contact our experts for tailored solutions!