Microwave sintering is a process that uses microwave energy to heat ceramic materials to their sintering temperature, typically ranging from 1200°C to 1600°C, depending on the material. This method generates heat internally within the material, offering faster heating rates, energy efficiency, and improved product properties. The process involves several steps, including charging, vacuuming, microwave heating, insulation, and cooling. While microwave sintering is effective for small loads and maintaining fine grain sizes, it has limitations, such as limited penetration depth in conductive materials and challenges in cooling the equipment. Despite these drawbacks, it is a promising technique for high-speed sintering and maintaining material integrity.
Key Points Explained:
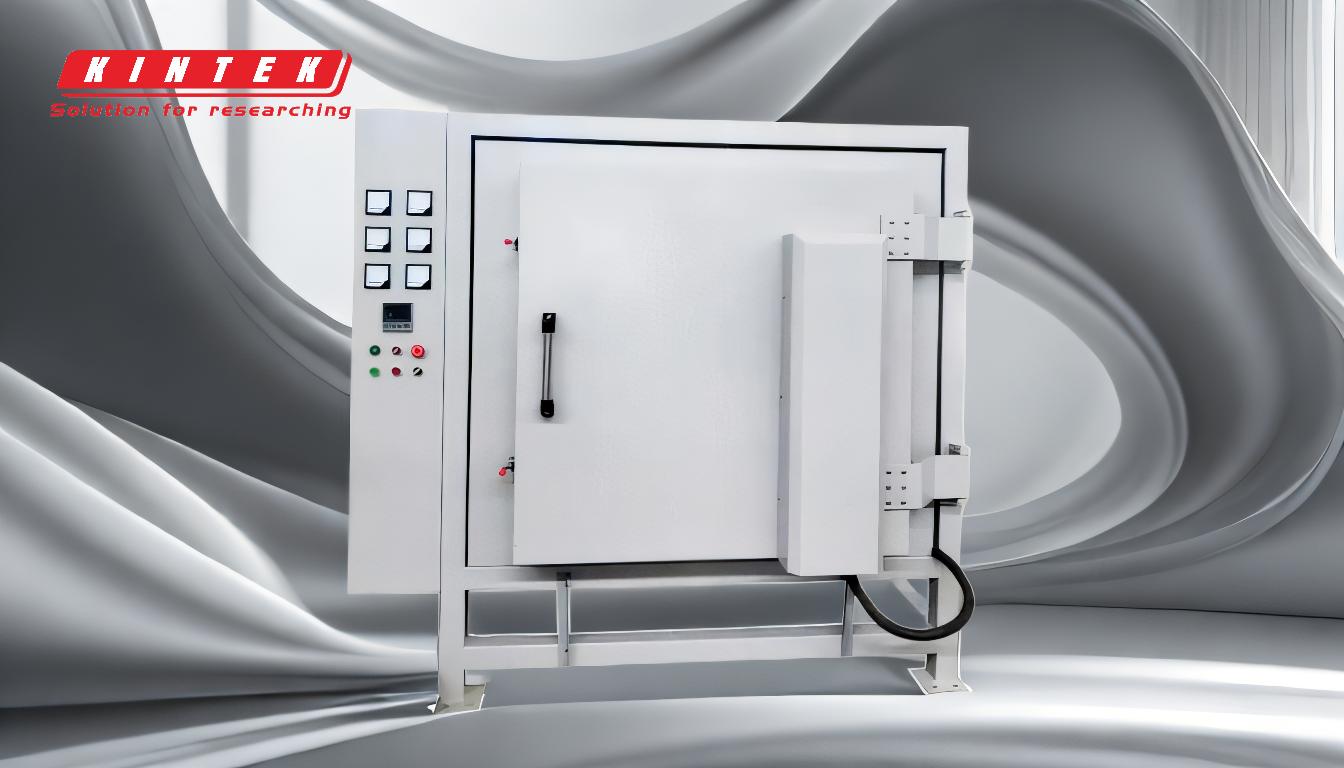
-
Temperature Range for Microwave Sintering:
- Microwave sintering typically operates at temperatures between 1200°C to 1600°C, depending on the material being sintered.
- This temperature range is critical for achieving densification, chemical reactions, and crystallization in ceramic materials.
-
How Microwave Sintering Works:
- Microwave sintering uses electromagnetic fields to couple with the microstructure of ceramic materials, generating heat internally rather than relying on external heat sources.
- The process involves:
- Charging: Placing the ceramic material into the furnace.
- Vacuuming: Removing gases and impurities to create a controlled environment.
- Microwave Heating: Applying microwave energy to raise the material to the sintering temperature.
- Insulation: Maintaining the temperature to allow chemical reactions and crystallization.
- Cooling: Gradually reducing the temperature to room temperature.
-
Advantages of Microwave Sintering:
- Faster Heating: Microwave sintering heats materials more quickly than conventional methods.
- Energy Efficiency: It consumes less energy by directly heating the material rather than the surrounding environment.
- Improved Product Properties: The process helps maintain fine grain sizes, which is particularly beneficial for bioceramics.
-
Limitations of Microwave Sintering:
- Limited Penetration Depth: Microwaves penetrate only a short distance in materials with high conductivity and permeability, requiring powders to have particle sizes similar to the penetration depth.
- Single-Compact Sintering: The process typically sinters one compact at a time, limiting overall productivity.
- Cooling Challenges: Operating equipment can overheat, requiring auxiliary cooling systems.
-
Equipment and Setup:
- A microwave sintering furnace consists of:
- A microwave source to generate the electromagnetic field.
- A heating cavity where the material is placed.
- A material transfer system for loading and unloading.
- Susceptor plates and materials are often used to absorb microwave energy and convert it to heat, especially for materials that do not couple well with microwaves.
- A microwave sintering furnace consists of:
-
Applications and Suitability:
- Microwave sintering is particularly effective for:
- Small Loads: Due to its ability to heat materials quickly and uniformly.
- Bioceramics: Maintaining fine grain sizes and material integrity.
- It is less suitable for large-scale production due to its single-compact sintering limitation.
- Microwave sintering is particularly effective for:
-
Future Prospects:
- Microwave sintering is a relatively new technique with potential for scaling up and improving productivity.
- Advances in cooling systems and susceptor materials could address current limitations and expand its applications.
By understanding these key points, purchasers and users of microwave sintering equipment can make informed decisions about its suitability for their specific needs and applications.
Summary Table:
Aspect | Details |
---|---|
Temperature Range | 1200°C to 1600°C, depending on the material |
Process Steps | Charging, vacuuming, microwave heating, insulation, cooling |
Advantages | Faster heating, energy efficiency, improved product properties |
Limitations | Limited penetration depth, single-compact sintering, cooling challenges |
Applications | Small loads, bioceramics, fine grain size maintenance |
Future Prospects | Potential for scaling up, improved cooling systems, and advanced materials |
Discover how microwave sintering can enhance your ceramic processing—contact our experts today!