The temperature of a pyrolysis reactor is a critical parameter that directly influences the efficiency and outcomes of the pyrolysis process. Pyrolysis reactors typically operate at high temperatures, often ranging between 350-400 degrees Celsius, to facilitate the thermal decomposition of waste materials into valuable products such as pyrolysis oil, carbon black, and syn-gas. This temperature range is necessary to ensure the breakdown of complex organic compounds into simpler molecules. Factors such as the composition of the material being processed, residence time, particle size, and heat supply also play significant roles in determining the optimal operating temperature and the overall efficiency of the reactor.
Key Points Explained:
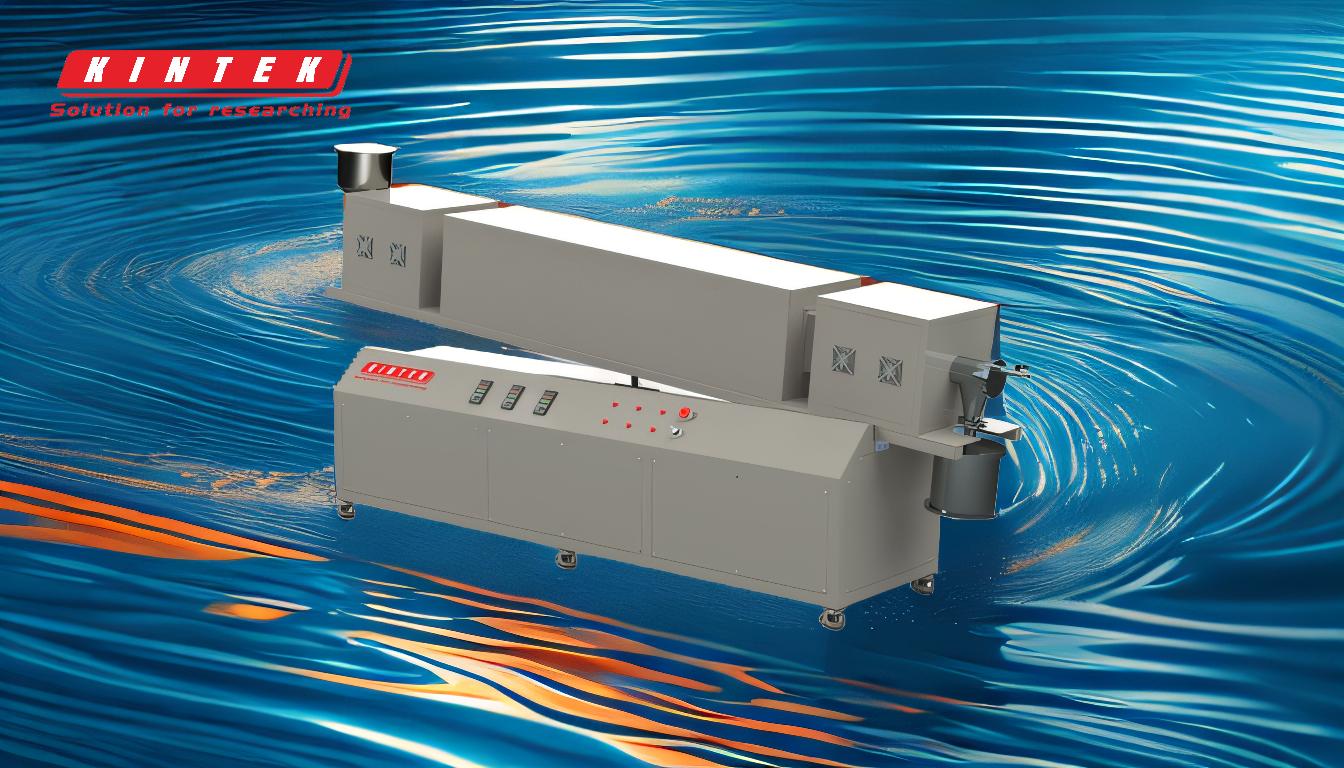
-
Typical Operating Temperature Range:
- Pyrolysis reactors generally operate at temperatures between 350-400 degrees Celsius. This range is essential for achieving the thermal decomposition of waste materials, which is the core objective of the pyrolysis process.
- At these temperatures, complex organic compounds in the feedstock break down into simpler molecules, producing valuable outputs like pyrolysis oil, carbon black, and syn-gas.
-
Influence of Temperature on Pyrolysis Outcomes:
- Higher temperatures (within the 350-400°C range) tend to increase the production of non-condensable gases, such as hydrogen, methane, and carbon monoxide.
- Lower temperatures favor the production of high-quality solid products, such as biochar or carbon black.
- The temperature must be carefully controlled to optimize the yield of desired products, as different components of biomass and waste decompose at varying temperatures.
-
Factors Influencing Temperature Requirements:
- Composition of the Material: Different materials (e.g., plastics, biomass, rubber) have varying thermal decomposition thresholds, which affect the required reactor temperature.
- Residence Time: The duration that the material spends in the reactor influences the degree of thermal conversion. Longer residence times may require lower temperatures to avoid over-decomposition.
- Particle Size: Smaller particles decompose more quickly, potentially allowing for lower operating temperatures or shorter residence times.
- Heat Supply: External heat sources are often used to maintain the reactor temperature, and the efficiency of heat transfer can impact the required operating temperature.
-
Reactor Design and Temperature Control:
- Pyrolysis reactors are designed to maintain consistent temperatures through external heat sources and closed-system operation, ensuring efficient heat transfer and minimal heat loss.
- The mode of heat application (e.g., direct or indirect heating) and the geometry of the reactor (e.g., rotary kiln, tubular reactor) also play roles in determining the optimal temperature and heat distribution.
-
Thermodynamic Principles:
- Pyrolysis reactors operate based on thermodynamic principles, where the input of heat drives the endothermic reactions necessary for thermal decomposition.
- The reactor must balance heat input with the energy required to break chemical bonds in the feedstock, ensuring efficient conversion without excessive energy consumption.
-
Impact of Temperature on Process Efficiency:
- The temperature of the reactor directly affects the efficiency of the pyrolysis process. For example, in a rotary-kiln reactor, the speed of rotation and heat supply must be optimized to ensure uniform heating and decomposition.
- In a tubular reactor, the flow velocity of the substrate and the heat supply must be carefully controlled to achieve the desired temperature profile along the reactor length.
-
Practical Considerations for Equipment Purchasers:
- When selecting a pyrolysis reactor, purchasers should consider the temperature range and control mechanisms to ensure compatibility with the intended feedstock and desired products.
- The ability to adjust and maintain precise temperatures is crucial for achieving consistent product quality and maximizing process efficiency.
In summary, the temperature of a pyrolysis reactor is a key operational parameter that varies depending on the type of reactor, the feedstock, and the desired products. Understanding the interplay between temperature and other factors such as residence time, particle size, and heat supply is essential for optimizing the pyrolysis process and achieving high-quality outputs.
Summary Table:
Key Factor | Impact on Pyrolysis |
---|---|
Temperature Range | 350-400°C ensures thermal decomposition of waste into pyrolysis oil, carbon black, and syn-gas. |
Higher Temperatures | Increases production of non-condensable gases (e.g., hydrogen, methane). |
Lower Temperatures | Favors high-quality solid products like biochar or carbon black. |
Material Composition | Different feedstocks (plastics, biomass, rubber) require specific temperature thresholds. |
Residence Time | Longer times may need lower temperatures to avoid over-decomposition. |
Particle Size | Smaller particles decompose faster, potentially reducing required temperatures. |
Heat Supply | Efficient heat transfer is critical for maintaining optimal reactor temperature. |
Ready to optimize your pyrolysis process? Contact our experts today for tailored solutions!