Vacuum casting is a manufacturing process used to create high-quality prototypes or small batches of parts using silicone molds and polyurethane resins. The temperature during vacuum casting typically ranges between 30°C to 70°C, depending on the material being used and the specific requirements of the process. This temperature range ensures proper curing of the resin while maintaining the integrity of the silicone mold. Higher temperatures may accelerate curing but risk damaging the mold, while lower temperatures may result in incomplete curing or longer cycle times. The process is highly dependent on the material properties, mold design, and desired outcome.
Key Points Explained:
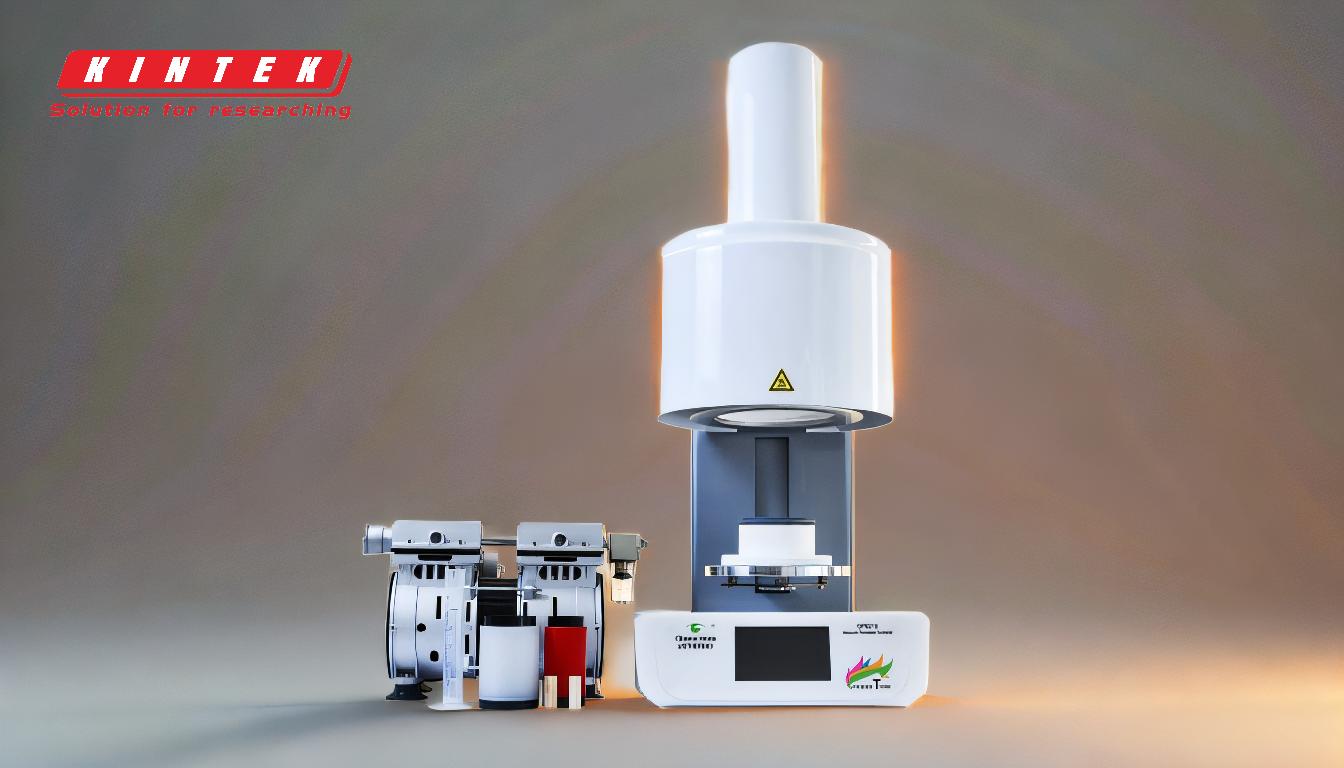
-
Temperature Range for Vacuum Casting:
- The temperature for vacuum casting generally falls between 30°C to 70°C.
- This range is optimal for curing polyurethane resins without degrading the silicone mold.
- Higher temperatures (closer to 70°C) are used for faster curing but require careful monitoring to avoid mold damage.
- Lower temperatures (closer to 30°C) are used for delicate materials or when extended curing times are acceptable.
-
Factors Influencing Temperature Selection:
- Material Properties: Different resins have specific curing temperature requirements. For example, some resins cure faster at higher temperatures, while others require lower temperatures to prevent warping or cracking.
- Mold Durability: Silicone molds have a limited tolerance for high temperatures. Exceeding 70°C can cause the mold to degrade, reducing its lifespan.
- Part Complexity: Complex parts with fine details may require lower temperatures to ensure accurate replication and minimize stress on the mold.
- Cycle Time: Higher temperatures reduce curing time, which is beneficial for high-volume production but must be balanced against mold wear.
-
Process Details:
- The vacuum casting process involves pouring liquid resin into a silicone mold under vacuum conditions to remove air bubbles.
- The mold is then placed in a temperature-controlled oven or chamber to cure the resin.
- The curing time varies based on temperature and resin type, typically ranging from 1 to 24 hours.
-
Importance of Temperature Control:
- Precise temperature control ensures consistent part quality and minimizes defects such as bubbles, warping, or incomplete curing.
- Temperature fluctuations can lead to variations in part dimensions and mechanical properties.
-
Material Considerations:
- Polyurethane resins are the most commonly used materials in vacuum casting due to their versatility and ability to mimic various engineering plastics.
- The choice of resin affects the required curing temperature. For example, rigid resins may require higher temperatures, while flexible resins may need lower temperatures.
-
Equipment Requirements:
- A temperature-controlled oven or chamber is essential for maintaining the desired curing temperature.
- Vacuum chambers are used to degas the resin and remove air bubbles before casting.
-
Applications of Vacuum Casting:
- Vacuum casting is widely used in industries such as automotive, aerospace, consumer electronics, and medical devices for prototyping and low-volume production.
- The process is valued for its ability to produce parts with high dimensional accuracy and surface finish.
-
Advantages of Vacuum Casting:
- Cost-effective for small batches compared to injection molding.
- High flexibility in material selection and part design.
- Short lead times for prototyping.
-
Limitations of Vacuum Casting:
- Limited mold lifespan (typically 20-25 uses).
- Not suitable for high-volume production due to slower cycle times compared to injection molding.
- Temperature sensitivity requires careful process control.
-
Best Practices for Temperature Management:
- Use a calibrated thermometer or temperature sensor to monitor the curing environment.
- Follow the resin manufacturer’s guidelines for curing temperature and time.
- Avoid rapid temperature changes to prevent thermal stress on the mold and part.
By understanding the temperature requirements and their impact on the vacuum casting process, manufacturers can optimize part quality, mold longevity, and production efficiency.
Summary Table:
Key Aspect | Details |
---|---|
Temperature Range | 30°C to 70°C |
Optimal Curing | Ensures resin cures without degrading silicone molds |
Higher Temperatures | Faster curing but risks mold damage |
Lower Temperatures | Suitable for delicate materials or extended curing times |
Curing Time | 1 to 24 hours, depending on temperature and resin type |
Key Applications | Automotive, aerospace, consumer electronics, medical devices |
Advantages | Cost-effective, flexible material selection, short lead times |
Limitations | Limited mold lifespan, not ideal for high-volume production |
Need help optimizing your vacuum casting process? Contact our experts today for tailored solutions!