The temperature range for sintering varies significantly depending on the material being processed, the desired characteristics of the final product, and the specific application. Generally, sintering temperatures can range from as low as 750°C to as high as 1,500°C or more. For example, dental sintering furnaces typically operate between 1,200°C and 1,400°C, while zirconia sintering can require temperatures closer to 1,500°C for optimal density. The process often involves precise control of heating and cooling rates, especially above 900°C, to achieve the best results. Additionally, the sintering atmosphere (inert, reducing, or oxidizing) and the use of shielding gases play critical roles in the process.
Key Points Explained:
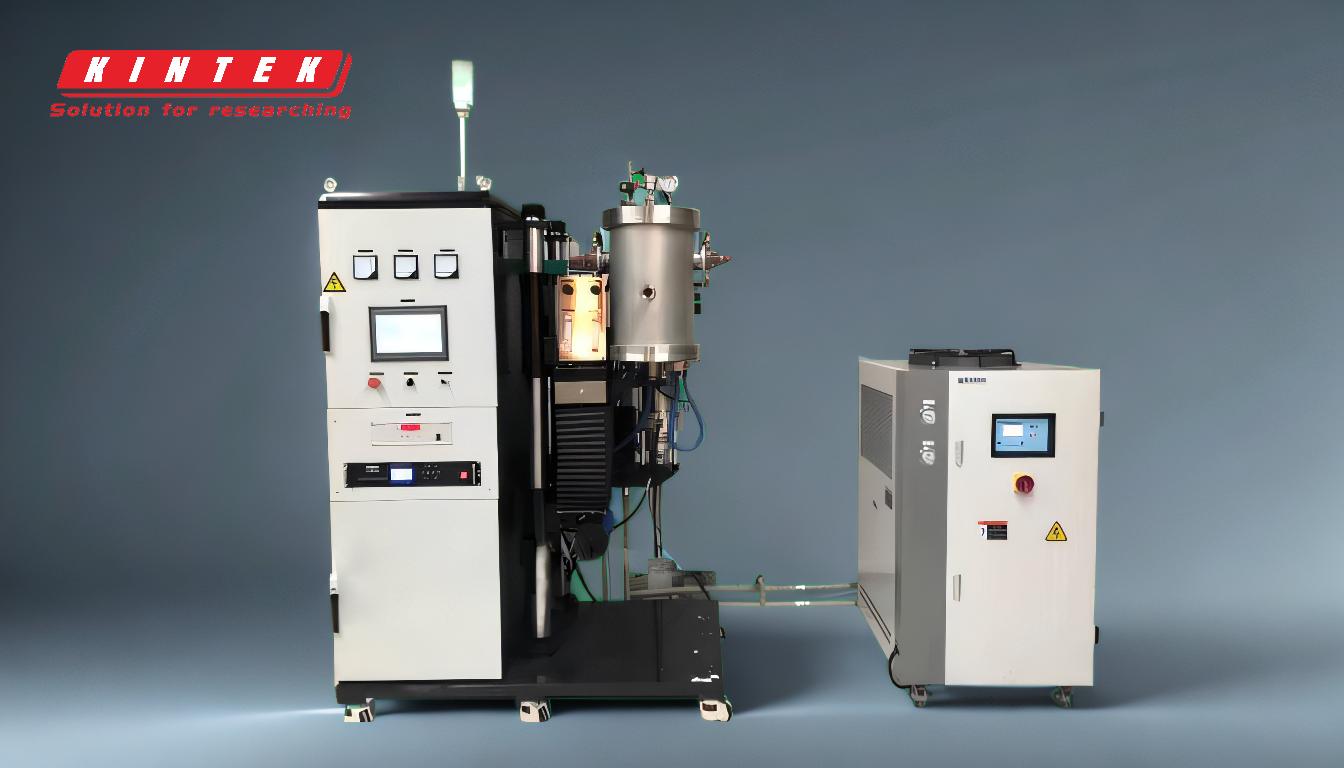
-
General Temperature Range for Sintering:
- Sintering typically occurs at elevated temperatures, usually above 750°C, and can extend up to 1,500°C or higher, depending on the material and application.
- For example:
- Dental sintering furnaces operate between 1,200°C and 1,400°C.
- Zirconia sintering often requires temperatures closer to 1,500°C to achieve high density (close to 99% of theoretical maximum density).
-
Material-Specific Temperature Requirements:
- Different materials have unique sintering temperature requirements:
- Metals, especially pure metals sintered in a vacuum, may require specific temperature ranges to avoid surface contamination.
- Zirconia undergoes a structural transformation from monoclinic to polytetragonal at around 1,100°C to 1,200°C, but higher temperatures (up to 1,500°C) are needed for densification.
- Different materials have unique sintering temperature requirements:
-
Critical Temperature Zones:
- From room temperature to 900°C, there is minimal effect on the material.
- The critical phase begins above 900°C, where the ramp rate (heating speed), consistency during the hold time, and cooling rate back to 900°C are crucial for achieving optimal results.
-
Atmosphere and Gas Shielding:
- Sintering is often conducted in controlled atmospheres (inert, reducing, or oxidizing) to prevent contamination and ensure proper material properties.
- For metals sintered at atmospheric pressure, shielding gases (e.g., endothermic gas) are used to protect the material.
-
Importance of Temperature Control:
- Precise control of temperature during sintering is essential to achieve the desired material properties, such as density, strength, and microstructure.
- Inconsistent temperatures or improper heating/cooling rates can lead to defects or suboptimal performance in the final product.
-
Application-Specific Considerations:
- In dental applications, sintering furnaces must accommodate specific temperature profiles to ensure the durability and aesthetics of dental restorations.
- For industrial applications, the sintering temperature is tailored to the material's properties and the intended use of the final product.
By understanding these key points, equipment and consumable purchasers can make informed decisions about sintering furnaces and related materials, ensuring they meet the specific requirements of their applications.
Summary Table:
Key Aspect | Details |
---|---|
General Temperature Range | 750°C–1,500°C+, depending on material and application. |
Dental Sintering | 1,200°C–1,400°C for dental restorations. |
Zirconia Sintering | Up to 1,500°C for high density (99% of theoretical maximum). |
Critical Temperature Zone | Above 900°C: Precise heating/cooling rates are crucial. |
Atmosphere Control | Inert, reducing, or oxidizing atmospheres prevent contamination. |
Shielding Gases | Used for metals sintered at atmospheric pressure (e.g., endothermic gas). |
Need help selecting the right sintering furnace? Contact our experts today for tailored solutions!